Most Common MIG Welding Defects
In the intricate world of Metal Inert Gas (MIG) welding, achieving flawless welds takes time, skill, practice, and precision. Although MIG is considered a beginner-friendly method, even seasoned welders encounter challenges and common MIG welding defects.
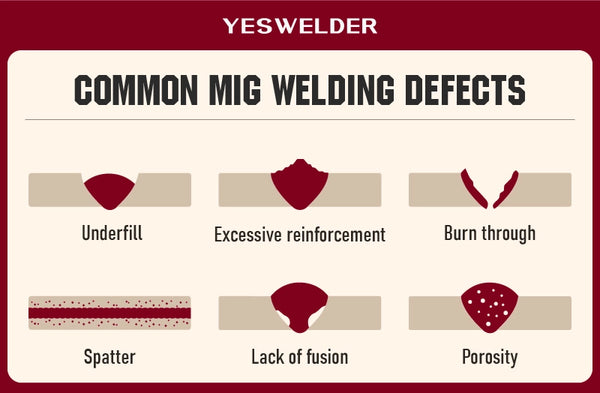
From porosity and spatter to incomplete penetration, this article delves into the pervasive issues that can compromise the structural integrity and aesthetic appeal of MIG welded joints. Understanding the root causes, identifying visual cues, and implementing effective troubleshooting techniques are essential for welders striving to elevate their craft.
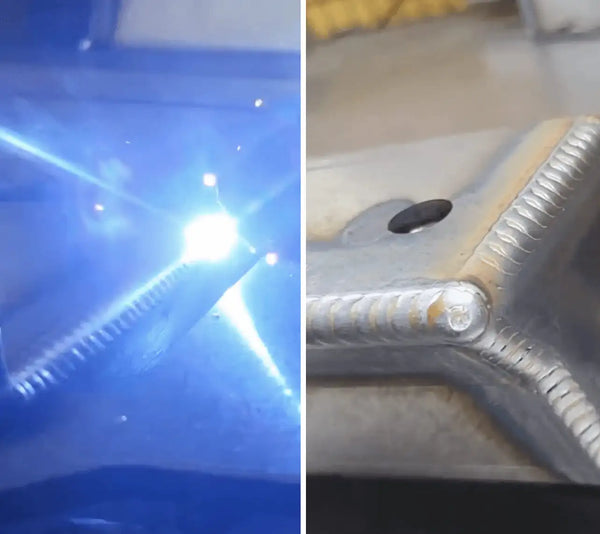
Photo by @weldsbyzen (TikTok)
What Are The Weld Defects?
Weld defects are imperfections or irregularities that can occur during the welding process, potentially compromising the strength, integrity, and appearance of the welded joint. Even the slightest overlook in terms of weld preparation, cleaning, shielding the weld, or welding parameters and technique can cause a weld defect that can compromise the integrity of the weld, leading to weldment failure.
There are two common types of weld defects:
- Surface irregularities
- Weld discontinuation.
Surface irregularities are the surface conditions that contain changes in the thickness or appearance of the weld. This type of defect is often referred to as an external weld defect since it can be seen with the naked eye. The most common surface irregularities are uneven weld beads, convex or concave welds, excessive reinforcement, underfill, uneven fillet weld legs, etc.
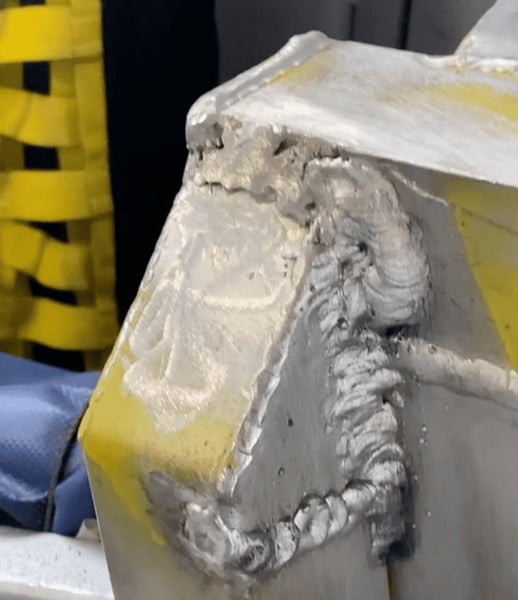
Weld discontinuation is the interruption of the structural integrity of the weld in terms of mechanical, metallurgical, or physical characteristics. Discontinuations are often called internal defects since they occur inside the weld. Typical internal defects are porosity, slag inclusions, lack of fusion, burn-through, and hot and cold cracks.
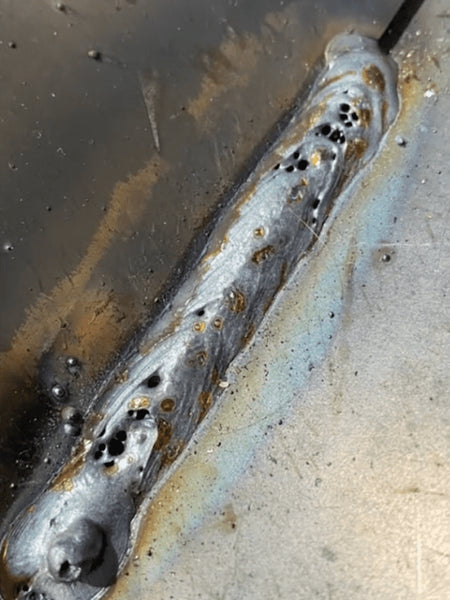
Keep in mind that both surface irregularities and weld discontinuation can compromise the integrity of the weld, but internal welding defects are considered more dangerous. Still, a Welding Procedure Specification in specific applications can allow a permissible range of extent to which there is no need for rework, even though minor defects are present.
How Do You Detect Weld Defects?
In critical applications, all welds are subjected to a series of destructive or non-destructive tests to check for defects and determine if the weld structure and strength suit the specifications. Non-destructive tests include visual inspection, X-ray, penetrant, and dye testing to check for cracks or holes in the surface and internal welds. Destructive tests include breaking the joint or testing its tensile and yield strength through a series of bending tests.
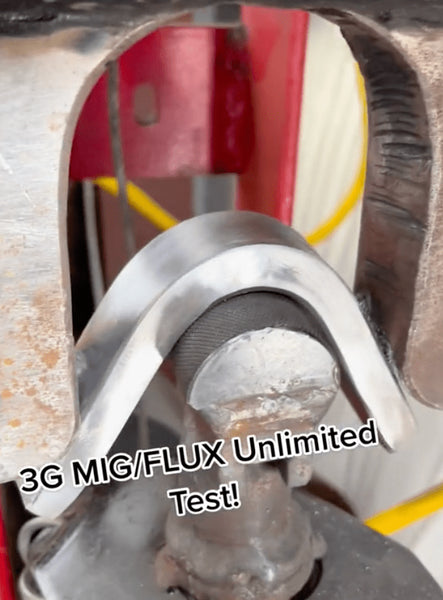
Photo by @precisionweldingacademy (TikTok)
As a hobbyist or DIY welder, you can detect most weld defects by looking at the weld (visual inspection). You don't need special machines to notice holes, welding cracks, or uneven welds. Excellent and strong MIG welds are uniform and even, without spatter, porosity, too much filler material, or too little weld metal. If you see anything other than that, it might be a sign that something is wrong with your weld.
Common MIG Welding Defects And How To Prevent Them
MIG welding is a semi-automated process highly appreciated among beginners and hobby welders. Compared to manual methods such as Stick or TIG welding processes, the welder automatically feeds the wire, so there is one less thing to worry about. The easier the process is, the fewer chances you'll encounter weld defects. However, welding takes time and practice, so dealing with imperfections and irregularities is not uncommon.
The most common MIG welding defects are:
- Porosity
- Lack of fusion
- Burn through
- Excessive spatter
- Convex and concave welds
- Underfill and excessive reinforcement
Photo by @welddotcom (TikTok)
Understanding why each defect occurs is crucial for troubleshooting and minimizing the need for frequent reworks on your projects. So, let's dive into it.
1. Porosity In MIG Welding
Porosity is among the most common welding defects across all methods, including MIG welding. It can occur due to various reasons, and that's why it's that frequent. Porosity shows as the tiny holes that appear in the weld, and it is usually depicted as surface porosity, which is easily noticeable. Pores or voids weaken the weld, potentially leading to reduced structural integrity and performance.
The porosity in MIG welding occurs once the gas becomes trapped in the weld metal during the welding process. Once atmospheric gasses such as nitrogen, oxygen, or hydrogen enter the molten weld puddle, they start burning and escaping from the weld, forming gas bubbles. This can result from inadequate shielding gas or improper gas flow rates.
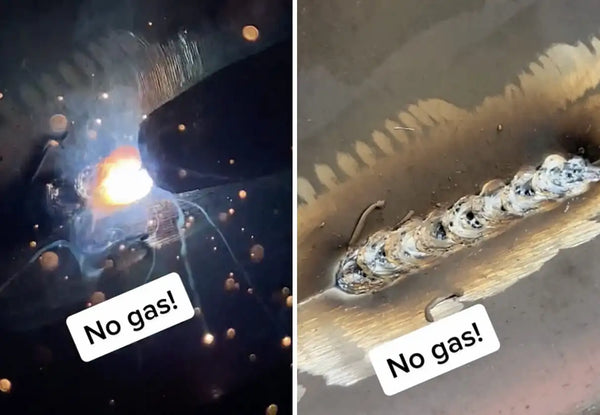
Porosity in MIG welding can also occur due to contamination and dirt. MIG welding is ineffective in burning through dirt, rust, or paint, so that contaminants can create small holes inside or on the surface of your weld. Improper welding techniques can also cause porosity, including excessive gun angle and extended stickout.
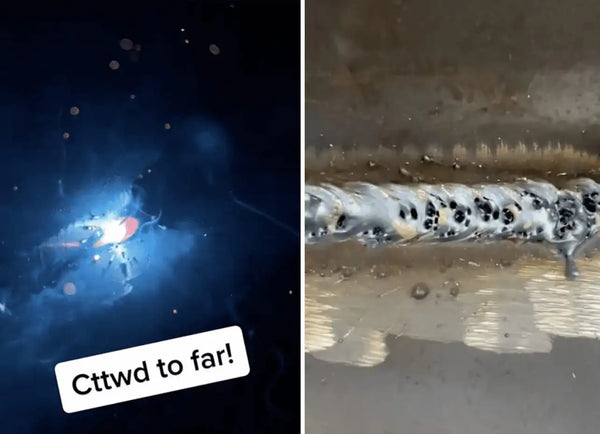
Photo by @dr.weldz (TikTok)
How To Prevent Porosity In MIG Welding
To prevent porosity, you must protect your weld from contamination by applying proper shielding gas coverage and cleaning the pieces before welding. Check the regulator or flow meter for adequate gas flow of 20-30 CFH. When welding in draft or windy conditions, you should increase the flow. However, keep in mind that more is not always better. Too high gas flow can cause turbulence in the weld, causing it to suck air inside instead of protecting the weld.
Also, use a large enough nozzle to shield the weld pool completely. Keep the nozzle clean and free of spatter. If porosity occurs even though you use proper flow and a clean nozzle, the cause can be wet or contaminated shielding gas cylinders. Remember to clean the pieces before welding. Surface contamination can easily form porosity, so make sure everything is clean.
Improper welding techniques can also cause porosity. So, avoid using an excessive MIG gun angle and stickout that is too long. The correct MIG torch angle is 0-15 degrees, and the stickout shouldn't be longer than 1/2 inch from the top of your nozzle.
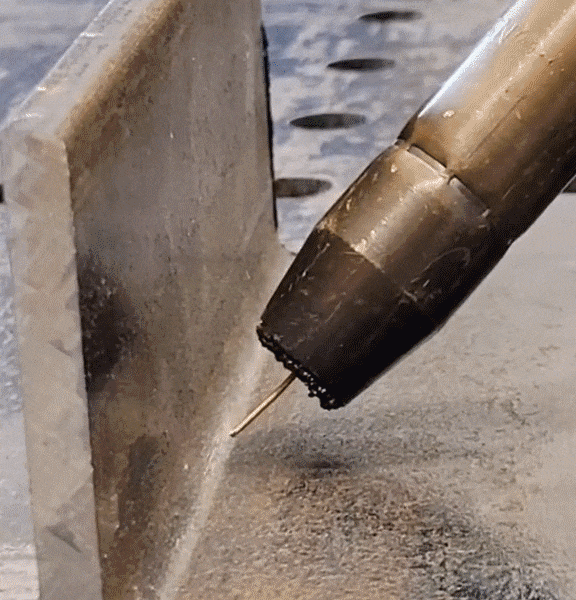
2. Lack Of Fusion In MIG Welding
Lack of fusion in MIG welding refers to a welding defect with inadequate bonding between the filler metal and the base metal or adjacent weld beads. This lack of fusion can compromise the strength and integrity of the welded joint, making it susceptible to failure under load or stress.
The leading causes of lack of fusion in MIG welding are improper welding electrode angle, incorrect travel speed, and insufficient heat input. Welding parameters are crucial in avoiding incomplete penetration and lack of fusion. Low voltage and wire feed speed will result in a lack of heat, leading to a lack of fusion.
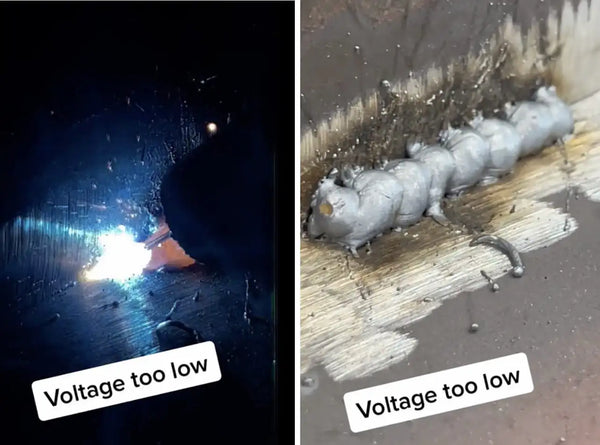
Welding technique shouldn't be disregarded. Even though you have the right equipment and proper parameters, if you go too fast, there won't be enough time for the molten metal to penetrate and fuse the pieces. In addition, improper arc position caused by a wrong travel angle can create a lack of fusion.
How To Avoid Lack Of Fusion
To avoid a lack of fusion in MIG welding, use the proper parameters, travel speed, and torch angle. Adjust the voltage and wire feed speed according to the manufacturer's recommendations, type, and thickness of the metal you are welding. As a beginner, it might take some time to get everything right, and if you are looking for a head-start, look for a MIG welder with synergic or auto-set features such as YesWelder MIG205DS-B.
YesWelder MIG-205DS-B Multi-Process MIG Aluminum Welder
Adjust the travel speed. Going too slow can cause excessive heat into the weld joint, and going too fast will cause a lack of penetration. Welding is all about moderation, so make sure you are using consistent travel speed or adjust it if you notice arc issues. Also, make sure you control the arc by using the correct travel angle and keep the arc on the leading edge of the weld pool.
3. Burn through In MIG Welding
Quite the opposite of lack of penetration, burn-through in MIG welding is a welding defect characterized by the formation of holes or craters in the welded joint due to excessive penetration of the weld metal through the base metal. This issue can compromise the integrity of the weld and, if not adequately addressed, may lead to structural weaknesses.
Burn-through in MIG welding occurs due to excessive heat provided by improper welding parameters or slow welding speed. This defect is common in thin materials and metals that are prone to heat buildup, such as aluminum. Even though MIG is not as hot as Stick or Submerged arc welding, the slightest mistake can result in burning through the pieces, leading to eventual weld failure.
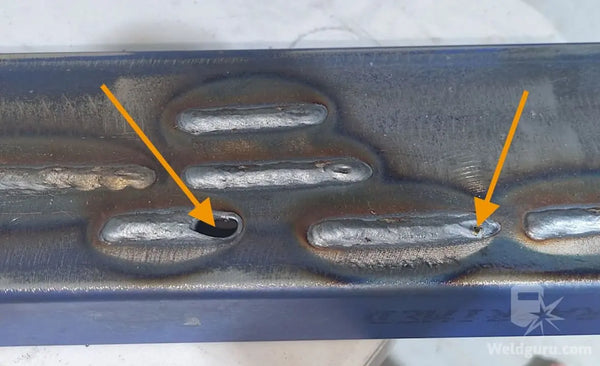
Source: https://weldguru.com/welding-burn-through/
How To Prevent Burn-Through
To prevent burn-through in MIG welding, make sure you control the heat input and avoid going too slow. High voltage and wire feed speed will produce excessive heat input in the molten weld pool, causing it to completely burn through the base metal. Therefore, if you notice you are burning holes in the weld, lower the welding parameters, but try not to get too low since you can get a lack of penetration.
Additionally, you can burn through the pieces if your welding speed is too low. Even if the amperage and arc voltage are moderate, spending too much time in one place will eventually burn through the pieces. So, if you notice that the weld bead is getting too hot, try increasing the travel speed, but not too much, since you can get improper penetration.
4. Excessive Spatter Weld Defect
Even though MIG welding produces less spatter than Stick or flux-cored wire welding, it can still occur due to contaminated wire, dirty base metal, high heat, or poor shielding. Spatter represents small droplets of molten metal that are expelled from the welding arc and adhere to surfaces surrounding the weld.

Source: https://www.weldingis.com/welding-discontinuities/
While spatter won't affect the structural integrity of the weld, it can lead to a range of issues, including reduced weld quality, increased post-weld cleanup, and potential safety hazards. Hard spatter can be hard to clean, and it will affect the quality of the weld. Additionally, lots of flying droplets can burn you or start a fire in a shop.
Preventing Excessive Spatter
To prevent excessive spatter flying around, make sure you check your welding wire. Contaminated, rusty, or moist electrode wire will spatter a lot, so store them correctly and away from the moisture. Also, always use high-quality wires such as YesWelder ER07S-6 solid wire. Besides porosity, dirty and contaminated surfaces can also create spatter. As the paint or rust starts burning due to the heat of the arc, it can begin spatting around, so try to keep things clean.
ER70S-6/10LB-0.8 .030" 10LB Spool Carbon Steel Solid MIG Welding Wire
Spatter can also form due to high voltage and wire feed speed. Even though you want to increase them to achieve fast spray transfer, spraying can create lots of spatter and burn through the thinner pieces. Meanwhile, flux-cored or metal-cored wires can also produce excessive spatter due to low voltage.
In addition, preventing welding defects such as spatter will require proper shielding and wire stickout. Like with porosity, adjust the gas flow according to welding conditions, and make sure your stickout is not longer than 1/2 inch. When switching from solid to flux core wire, pay attention to polarity. Flux core works at DCEN (electrode negative) or straight polarity, while MIG is DCEP. Using the wrong polarity will cause an inconsistent arc with lots of spatter.
5. Convex And Concave Welds
In MIG welding, convex and concave are terms used to describe the appearance of the weld bead profile, and they are associated with certain welding defects. A convex weld bead has a raised and rounded profile, resembling a hump in the center of the weld. A concave weld bead has a depressed or sunken profile in the center, creating a trough-like appearance.
Convex weld beads are high, rope-like welds that generally occur in flat and horizontal welding positions but can also happen in fillet welds. Besides the appearance, convex weld beads typically have poor fusion of the toes, so they can also affect the integrity of the weld.
Concave welds are particularly prevalent when welding in vertical-down applications due to gravity. The gravity pulls down the molten metal, creating a sunken profile. Excessive concavity can lead to incomplete penetration and fusion, compromising the strength and integrity of the weld joint.
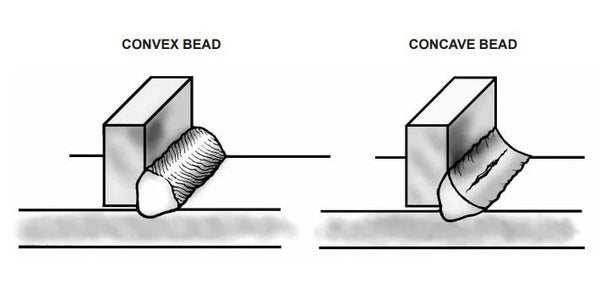
Source: https://www.reddit.com/r/Welding/comments/12jkqwe/welding_word_wednesday_convexity_v_concavity/
How To Prevent Convex And Concave Welds
Concavity typically occurs when the welding current or heat input is insufficient for the selected welding speed. When welding in a vertical position, lower the heat so the weld pool is less fluid. Lower fluidity will fight against gravity and help you fill in the joint. If a concave weld bead appears in the flat or horizontal position, reduce the voltage, increase the wire feed speed, and reduce the travel speed.
Convexity is often caused in flat and horizontal welding by excessive welding current or heat input relative to the welding speed. This can result in the weld metal being pushed up and away from the base metal, creating a convex shape. So, increase the voltage to prevent convex beads, use proper shielding gas for the material, and use the correct polarity for the wire.
6. Underfill And Excessive Reinforcement
Underfill and excessive reinforcement are closely related to filler material deposition. Excessive reinforcement, also known as excessive buildup or overwelding, occurs when there is an excess of weld metal beyond the desired surface level of the joint. Underfill, or insufficient reinforcement, refers to a weld bead that does not adequately fill the joint or falls below the specified surface level.
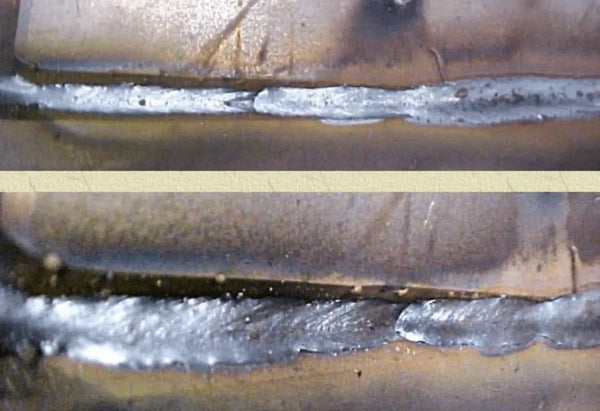
Excessive reinforcement can lead to stress concentrations and potential failure points in the weld. Wasting too much filler material will increase overall costs and produce poor-looking welds. High-stress concentration levels build up in the toes of the welds, so this weld defect presents appearance, structural, and economic issues.
Underfill can result in reduced joint strength and compromised structural integrity. Since the weld joint is not filled, underfill can lead to incomplete fusion between the filler and base metal. Incomplete fusion creates weak connections that are prone to cracking. Additionally, the joint may not meet design or code requirements.
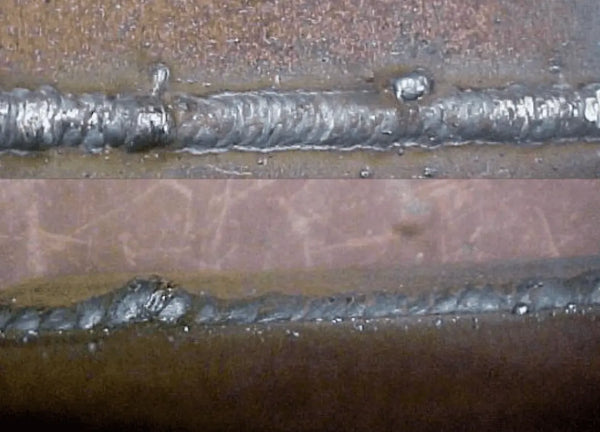
Preventing Underfill And Excessive Reinforcement Issues
Since underfill and over-welding result from improper filler material deposition, you must adjust the parameters, including voltage and wire feed speed, and adopt the proper technique.
Excessive reinforcement in MIG welding occurs due to high welding current or voltage settings, slow travel speed, and excessive wire feed rate. Therefore, you will want to lower the parameters and increase the travel speed, but in moderation, where you don't risk a lack of penetration.
Underfill in MIG welding occurs due to low welding current, voltage, and fast travel speed. If you don't have enough heat or are going too fast, the weld metal deposition is too low to fill the entire joint. Therefore, try to increase the wire feed speed and voltage and go slower, but not to the rate that would risk over-welding or burning through the pieces.
Final Thoughts
Understanding and mitigating common defects are paramount for ensuring MIG weld quality and structural integrity. From porosity and incomplete penetration to excessive spatter and bead irregularities, these challenges demand meticulous attention to welding parameters and techniques.
You don't have to be an expert to notice holes, cracks, uneven or simply ugly-looking weld beads. If you are an absolute beginner, there are high chances you'll encounter any of these. But don't be disappointed.
As welders strive for precision and excellence, continuous learning, adherence to best practices, and a commitment to quality control remain the linchpins in achieving impeccable MIG welds and robust, reliable structures.
🧐Most Common MIG Welding Defects - FAQ
1. What Are The Weld Defects?
There are two common types of weld defects:
- Surface irregularities
- Weld discontinuation.
Surface irregularities are the surface conditions that contain changes in the thickness or appearance of the weld. This type of defect is often referred to as an external weld defect since it can be seen with the naked eye. The most common surface irregularities are uneven weld beads, convex or concave welds, excessive reinforcement, underfill, uneven fillet weld legs, etc.
Weld discontinuation is the interruption of the structural integrity of the weld in terms of mechanical, metallurgical, or physical characteristics. Discontinuations are often called internal defects since they occur inside the weld. Typical internal defects are porosity, slag inclusions, lack of fusion, burn-through, and hot and cold cracks.
2. What are the most common MIG welding defects?
The most common MIG welding defects are:
- Porosity
- Lack of fusion
- Burn through
- Excessive spatter
- Convex and concave welds
- Underfill and excessive reinforcement
👏 You may be interested in the following:
Leave a comment