How To Weld Copper - MIG, TIG, And Stick Welding Copper Overview
You can weld almost all copper alloys and pure copper using arc welding processes. But you can also solder or braze copper and its alloys to achieve a joint in certain applications.
Welding copper is quite a challenge if you don't know its properties and some key steps of the copper welding process. However, welding copper becomes fairly simple if equipped with the proper knowledge.
In this article, you'll learn how to weld copper, when to weld it as opposed to soldering or brazing it, why welding copper is challenging, and the crucial information about pre-welding preparation.

Photo by @focusonthearc
Welding vs. Soldering vs. Brazing Copper
Not all copper joining requires a genuine fusion welding process (melting the two base metals and the filler metal together into a welded joint). Sometimes, it's good enough to solder or braze copper. But, since people can mistake these three joining processes, let's quickly address them in the context of joining copper.
Soldering Copper - Soldering copper is performed using temperatures below 840ºF. The copper never melts in the process; only the filler metal melts and forms a capillary joint where capillary forces force the filler metal to flow into the capillary space. The most common filler metals for soldering are tin (Sn) alloys. This is the most common way to join small diameter copper pipes.

Photo by @plumbingjourney
Brazing Copper - Brazing works much like soldering. It also relies on capillary action and never melts the copper joint. However, brazing temperatures go above 840ºF, so you can braze with stronger filler metals and achieve a higher strength joint. Typically, "BCuP" and "BAg" filler metals are used for brazing copper alloys.

Photo by @titan_steel_fabrication
Welding Copper - Welding copper and copper alloys produces the strongest joints because the copper parts actually fuse together with the filler metal. Besides higher joint strength and fatigue resistance, welding copper provides electrical continuity. So, if you need to repair busbars or other kinds of electrically conductive elements, you should weld them together with a copper based filler metal.

Photo by @the.fabricator
Why is Welding Copper Difficult?
Welding copper is challenging because there is a vast array of copper alloys, and many require special attention. In addition, copper has a very high thermal and electrical conductivity and a low melting point, making it very tricky to weld.
"Free-Machining" copper alloys containing tellurium and selenium shouldn't be welded because they are very susceptible to cracking. But most other copper alloys are weldable.
Copper and many of its alloys have incredibly high thermal conductivity. As a result, the heat will rapidly dissipate through the welded part and away from the joint. If the heat moves away from the joint, you may not be able to achieve the necessary penetration, especially if welding thick copper parts. But we'll discuss how to solve this issue soon.
You should also take steps to avoid warping and distortion because copper has a high coefficient of thermal expansion. However, it's possible to minimize distortion using fixtures, clamps, and making tack welds with enough space between them.

Source: https://weldguru.com/tack-welding/
Some copper alloys like copper-nickel and copper-tin are very susceptible to hot cracking as the weld solidifies. Extreme shrinkage stresses emerge because of a wide temperature range between the liquid and solid copper states in these alloys. Therefore, it's paramount to let the weld cool slowly and avoid restraining the joint as much as possible.

Typical location of centreline and flare solidification cracks
Source: https://www.twi-global.com/technical-knowledge/faqs/faq-what-is-hot-cracking-solidification-cracking
Copper and its alloys are prone to oxides, especially if alloyed with aluminum. But silicon bronze also develops mill scale. In addition, alloying elements like cadmium, phosphorous, and zinc have low boiling points. These elements are highly likely to cause weld porosity as they vaporize during the welding process. It's important to select a filler metal low in these compounds to counteract their evaporation and use a high travel speed.
Finally, copper is often alloyed with elements dangerous to the welder's health. In particular, zinc, aluminum, cadmium, arsenic, chromium, and lead can cause severe health issues. All of these elements are found in copper alloys. So, you must ensure a healthy work environment where all OSHA rules for controlling hazardous welding fumes and gasses are followed.
Pre-cleaning and Oxide Removal
Since many copper alloys are highly sensitive, cleaning the welding joint rigorously is crucial. Remove all oils, paints, grease, dust, grime, or other contaminants from the material.
But, some copper alloys like copper-aluminum, copper-nickel, and copper-beryllium create surface oxides. For example, aluminum reacts with oxygen in the air and produces an aluminum oxide that makes welding aluminum very challenging. However, copper-aluminum alloys experience pretty much the same issue. Therefore, it's crucial to remove the surface oxides using a wire brush or grind wheels. But, only use tools dedicated explicitly to copper. Otherwise, you can contaminate the joint with other metals.

Source: https://www.youtube.com/watch?v=t2JZYn819DQ
Preheating The Copper
Aluminum-copper (aluminum-bronze), copper-tin, and copper-nickel alloys should not be preheated.
However, pure copper and many other copper alloys should be preheated to improve welding results. Since this material dissipates heat rapidly as you weld, you can enhance weld penetration by preheating the entire part. That way, the heat difference between the weld zone and the rest of the copper part will be reduced. As a result, less energy from the welding arc will flow to the entire part's volume, and more energy will be used to melt and fuse the joint.

Source: https://www.youtube.com/watch?v=zqhmKshcPt0
Here is a simple way to picture this: if the welded part is at a room temperature of 20°C or 68°F, and you are trying to weld the joint at about 1085°C, or 1985°F (copper melting temperature), you'll rapidly lose the heat to the surrounding, cold metal. The rest of the metal at room temperature will receive a considerable portion of the arc's energy. But, if you preheat the rest of the part to about 100-450°C, or 212-842°F (depending on the joint thickness), there will be a significantly reduced "force" trying to transfer the arc's heat from the joint to the surrounding material.
Many factors influence the required preheating temperature. But, the general rule of thumb is that the thicker the copper part, the higher the required preheat temperature. Experiment with scrap pieces first to determine if the selected preheat temperature helps you achieve full penetration. In addition, pure copper is a prime candidate for preheating. On the other hand, copper alloys can usually be welded without preheating, but if the alloy can be preheated and the joint is thick, consider preheating to improve weld fusion.
Selecting a Copper Welding Process
We recommend using a TIG (GTAW) welding process for most copper welding jobs. But, you can also use a MIG (GMAW) or stick (SMAW) arc welding processes to join copper.
Copper Welding Wire Selection
Filler metal selection for copper welding is complex. But here is a general rundown of the filler metals for welding pure copper and copper alloys:
- Use filler metals with deoxidants like the ERCu and ERCuSi-A when welding pure copper.
- The ERCuAl-A2 filler metal is designed for welding aluminum bronze, and welding copper to dissimilar metals.

Aluminum bronze overlay on a hydraulic tube
Photo by @abom79
- The ERCuNi filler metal is used for welding most copper-nickel alloys.
- The ERCuSi-A filler metal works for pure copper, copper-silicon, and copper-zinc alloys.
TIG Welding Copper
We recommend TIG welding thin to medium thick copper joints. You can TIG weld up to about 1/2 in. thick copper, but you'll need to significantly preheat the part before welding such high thicknesses (about 650°F). MIG welding works better for high thickness copper, but the TIG process has the advantage of precision and narrow heat affected zone (HAZ).
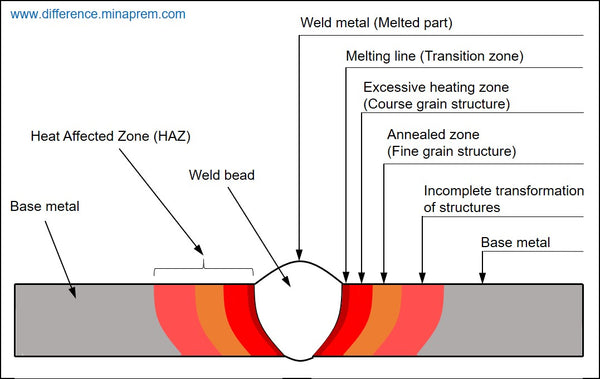
Source: http://www.difference.minaprem.com/joining/difference-between-weld-metal-and-heat-affected-zone-haz/
While you can use argon as a shielding gas, we suggest using 100% helium or 75% helium and 25% argon mixtures for joints above 1.5mm thick. Helium amplifies the arc's heat and significantly improves weld penetration, which is paramount when welding copper. Using helium will help avoid excessive heat losses to the surrounding metal.
Use forehand or backhand welding techniques with a relatively high travel speed. However, excessive travel speed can cause underfill along the edges. Stringer beads are preferred when welding copper because arc oscillation can expose bead edges to the atmosphere and unnecessary oxidation.

Source: https://weldguru.com/push-or-pull-when-mig-welding/
When performing multi-pass welds (welding thick sections), clean all oxidized welds before each pass.
You should use a DCEN polarity and thoriated tungsten for most copper welding jobs. However, to weld copper-aluminum alloys, you can use AC TIG to help break aluminum oxides on the material's surface. We sell a couple of TIG welders with the AC TIG output like the YesWelder CT2050 and the YesWelder TIG-250P ACDC.
YesWelder FIRSTESS CT2050 Powerful 7-in-1 Welder & Cutter
It may take a while for the copper joint to start melting, especially if you weld thick parts using a TIG welder with an insufficient amperage output. But once you get the puddle going, it keeps melting with ease.
MIG Welding Copper
The MIG welding process is preferred to weld thick copper pieces. Plus, you can use a bit lower preheating temperatures when MIG welding copper. In addition, MIG welding requires far fewer manual skills than TIG welding and allows significantly higher welding speeds.
Depending on if you'll melt and fuse the base metal with the MIG welding process, you can MIG weld or MIG braze copper and copper alloys. Most often, you'll actually MIG braze copper alloys like bronze using a silicone bronze MIG wire as an example.
Silicone bronze MIG brazing is quite popular in car shops because car autobody often must be repaired by brazing only. Since some cars are made from galvanized steel or aluminum coated steel, they cannot be melted as a part of the joining process. Furthermore, some car manufacturers mandate car body repairs via brazing only.

Silicon Bronze MIG Brazing
Source: https://www.youtube.com/watch?v=CaUkzcdHmws
To MIG weld/braze using copper filler wire, you should use U-knurl drive rolls and preferably a graphene MIG gun liner to prevent the wire from tangling inside the MIG welder. Since the copper-based filler wires are much softer than steel wires, like aluminum wires, they can easily kink through the feeding process and create a birdnest inside the welder.
Graphene Liner for Aluminum Welding
Use DCEP polarity to MIG weld or braze copper; this is your standard polarity you'd use to MIG weld steel.
The shielding gas should be either 100% argon or an argon/helium mixture. The more helium you use, the hotter the arc and the deeper the penetration.
Use stringer beads or narrow weave beads when MIG welding copper with a spray transfer. Just like with TIG welding, too much arc oscillation can oxidize bead edges. You can also use pulsed MIG welding to achieve better spray transfer and even weld copper in a vertical position (uphill). Our YesWelder YWM-211P offers the pulsed MIG welding process that may be able to help you when welding copper by allowing better puddle control.
YesWelder YWM-211P Double Pulse Aluminum MIG Welder
Stick Welding Copper
It's also possible to stick weld copper but with far worse results in weld quality compared to TIG and MIG welding.
Stick welding copper only makes sense when you need to work outside where it's not possible to achieve sufficient shielding gas coverage with TIG or MIG welding processes. Sometimes, SMAW can also be helpful if the joint has limited access and you can only reach it with a long stick welding rod.
There is a high chance of porosity and oxide inclusions when stick welding copper, especially when working with oxygen-free and tough-pitch coppers.
Use DCEP polarity and weld in the flat position only. You can use a stringer or a weave bead with the backhand welding technique.

Source: https://weldguru.com/welding-beads/
Conclusion
Copper is a tricky material to join, but if you apply the techniques we discussed, you'll have a higher chance of success. It may take some trial and error since this material generally requires a high travel speed, making it more difficult to control the outcome.
TIG welding copper gives you the best control over the weld puddle and the highest arc visibility. Plus, the focused TIG arc provides the best heat input and reduces the amount of heat that dissipates into the surrounding material. But MIG welding is easier and lets you weld faster.
We don't recommend stick welding copper for critical jobs. Use a stick welding process as a fallback method for minor repairs when MIG or TIG are not an option. Copper and its alloys can also be welded using oxy-acetylene, but the arc welding processes provide superior results.
This was a relatively quick overview of welding copper and its alloys. There are many details left to discuss for each specific copper alloy. Therefore, we recommend conducting thorough research when welding any copper alloy critical parts because individual chemical compositions can vary significantly. As a result, your preheat temperatures, filler metal selection, and welding techniques can differ from standard recommendations.

Custom copper box. Photo by @vermontcopper
Leave a comment