Butt Welds Explained
In the realm of welding and metal fabrication, butt welds stand as a fundamental and widely employed metal preparation technique. This is one of the most straightforward weld joint designs you will likely use as a beginner or new welder.
This article delves into the core of butt welds, unraveling their significance and the intricate process behind their execution. From understanding the basic concept of butt welds explained, we navigate through the essentials of various types and applications.
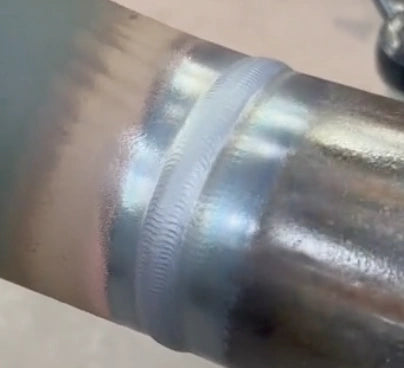
What Is A Butt Weld?
A butt weld is one of the most straightforward and widely used weld joint designs. The joint design determines how two pieces of metal are aligned before the welding. The butt joint is formed by placing two pieces of metal end-to-end and then welding along the joint.
What makes butt welding the easiest way to join metal is the fact the surfaces of the workpieces are on the same plane. The weld metal remains within the planes of the surfaces, while workpieces are nearly parallel and do not overlap like in lap joints.

Source: https://www.structuralbasics.com/butt-weld/
As a result, butt weld joints are used to join a plate, pipe, tubing, or in any other application where a smooth, flush weld face is required. As a beginner, you can use any welding process, such as MIG, TIG, or Stick welding. Additionally, welders can successfully apply arc welding, resistance welding, and high-energy beam welding in advanced applications.
Why Is Butt Welding Easy?
Butt joints are the easiest to weld since the gravity is working for you. Most butt welding joints are parallel and placed in a flat position, and you simply weld on top of them. As you weld, gravity pulls the molten weld puddle inside the welding joint, which allows you to fill the gap appropriately.
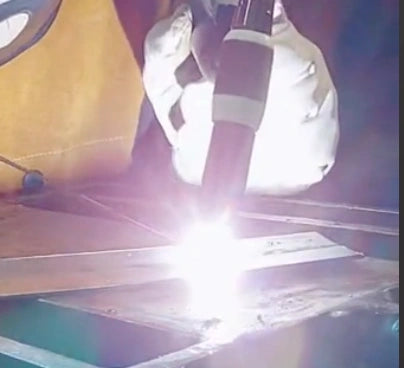
TIG welding a butt joint
Photo by @rootsrockryan (TikTok)
Properly filling the weld joint is crucial for achieving strong, even, and uniform welds with proper penetration and tie-in. When it comes to welding parameters, you can use the recommended heat input without a need to reduce the amperage, like in fillet welds.
Simply aligning and welding two pieces of metal without making too many adjustments to achieve proper tie-in and weld penetration is crucial when you need to get the job done quickly and easily. These advantages make a butt weld joint one of the easiest to prepare and weld on.
Types Of Butt Joint
Butt welds can be used when welding both thin sheet metal and thick metal, but there are specific steps in weld preparation. The thickness of the metal pieces will indicate whether the butt joints are square or beveled. A square butt weld and a beveled or groove butt weld are two commonly used techniques or types of butt weld.
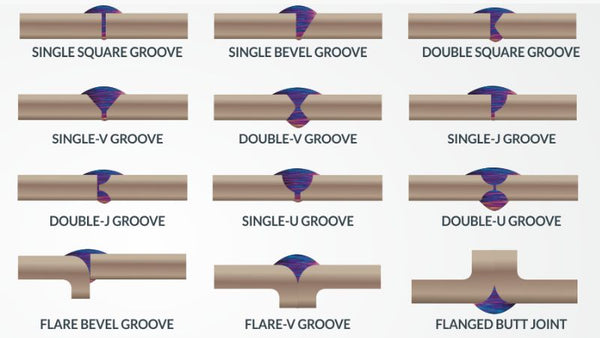
Square Butt Joints
When welding medium-thickness metals up to 3/16″, you can use a square butt weld, which is done simply by aligning two pieces of metal. The opening between them is typically 1/8 inch, which is enough to allow the molten metal to penetrate both parts. If the gap is too narrow, the molten metal will sit on top of the surface without properly penetrating both pieces. Meanwhile, if the gap is too broad, there can be a bulky seam on the reverse side.
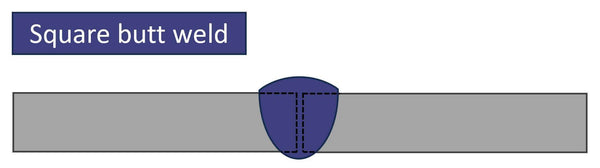
Source: https://www.structuralbasics.com/butt-weld/
However, if you are welding thin sheets down to 20 ga., you can use closed square butt joints. In this joint design, two pieces of metal are aligned with little to no gap. Since thin sheets can be vulnerable to high heat, which causes distortion and warping, typically, no filler metal is used. The heat of the arc itself melts both pieces, creating a method known as fusion welding or autogenous welding.
Groove Butt Welding Joints
Once the metal thickness goes over 3/16", you can struggle to achieve proper penetration and fusion by simply using a square butt joint design. These applications will require higher heat and larger electrodes, but it is often impossible to get 100% penetration without some type of square groove being used.
So, when welding thick metal, welders decided to create a root opening by beveling or grooving the edges. That way, the root opening is reduced to 1/16" or 1/8", and it is welded by a root pass with moderate parameters and a welding rod. The rest of the gap is filled with a series of fill passes in an operation known as multi-pass welding.
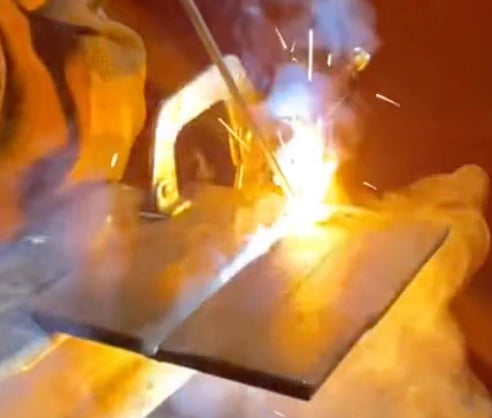
Depending on the appearance of the sides of the butt weld, the groove butt welds can be:
- Single bevel butt weld
- Double bevel butt weld
- Single J butt weld
- Double J
- Single V
- Double V butt weld
- Single U groove butt weld
- Double U grooves
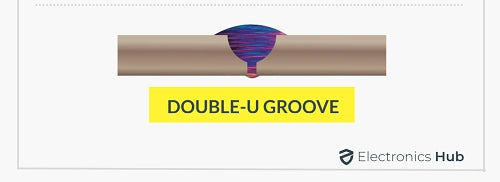
Source: https://www.electronicshub.org/butt-weld/
Each weld joint design is used in various applications, usually specified by Welding Procedure Specification. For example, a V-groove joint design is typically used for medium to thick metals (approximately 1/4). For even thicker metal plates, welders use U-groove butt welding and J-groove to provide good penetration of welded metal. Whether a fully penetrating or partially penetrating weld is required, different groove configurations must be used.
Butt Welding Symbols
Each butt weld has its designated symbol that is closely related to the shape of the bevel. The basic square groove butt weld symbols represent two parallel lines that illustrate the appearance of two pieces aligned at a square butt. Meanwhile, J, V, or U groove butt welds are represented with symbols that exact the appearance of the bevel or the same letters J, V, or U.
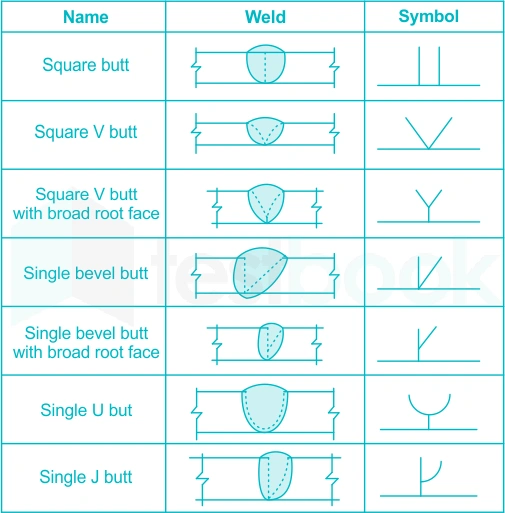
Single butt weld symbols are located on one side of the reference line, explaining the location of the bevel. Meanwhile, double-bevel butts are illustrated by using the required welding symbol on both sides of the reference line.
Butt Weld Vs. Fillet Weld
Fillet or tee welding joints are formed when two pieces intersect at a 90° angle, and this is another popular geometry used in the welding process. The edges are centered in a plate or component in a ‘T’ shape, but they can also be prepared as a corner joint or lap joint where two pieces of metal overlap. Unlike lap joints, butt welds do not overlap; they are parallel.
The primary difference between these two joint designs is the working angle. In fillet welds, the filler metal is deposited at a triangular section of the joint, creating an angle of 45 degrees. While gravity doesn't have that high impact, like in vertical welding, TIG alloy filler material can be pulled into one side of the joint, which leads to improper penetrating between both parts of the joint.
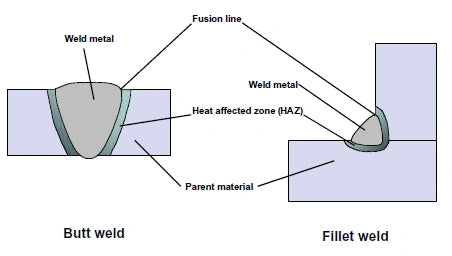
Fillet welding of thicker metal pieces is also done in multi-pass operation, but usually, the joints are not beveled. The welds are just deposited on top of each other without creating grooves. Similar to butt weld, fillet weld can cause distortion due to shrinkage as the filler metal cools down.
Butt Welds In Different Positions
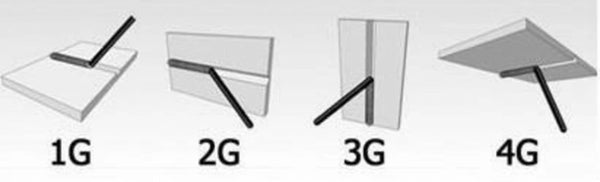
Butt weld joint design is typically laid on a flat surface and performed at a flat position (1G). This is the most straightforward butt weld position we talked about, and it includes welding a squared metal piece from the top using any welding process and recommended techniques and parameters.
In the horizontal butt position (2G), things get a bit tricky. The plates are placed vertically on top of each other, while the weld axis is roughly horizontal, ergo the name horizontal position. The gravity drags the weld puddle from the joint, so you'll have to decrease the heat and slightly favor the top edge of the joint.
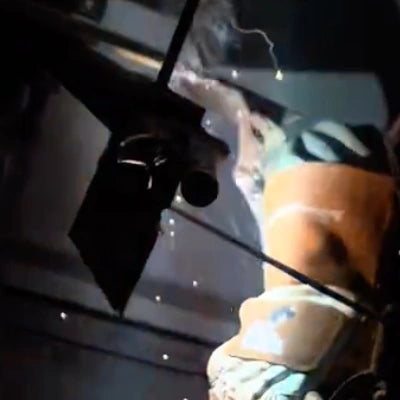
Vertical butt welding position (3G) includes welding vertically, and the best practice is from the bottom to the top (vertical up) to ensure proper control over the puddle and proper penetration. You will have to reduce the heat to help the molten metal solidify faster and don't flow down the butt joint.
Overhead butt welds (4G) are the hardest, as you are welding a butt joint above your head. Gravity will pull the molten metal down, so be prepared for lots of droplets, spatter, and molten metal flying into your face. You'll need a similar approach to vertical welds, which include weaving the torch and reducing the heat.
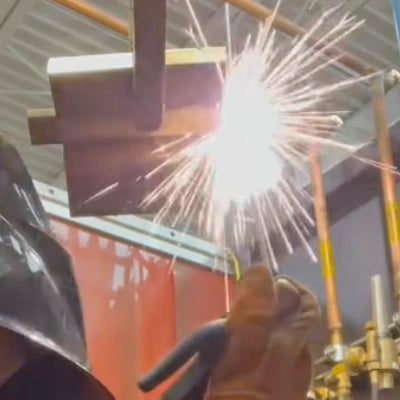
Applications Of Butt Welds
Butt welds find extensive applications across various industries due to their versatility and ability to create strong, seamless connections between metal components. The widespread use of butt welds across these industries highlights their importance in creating reliable, seamless connections that meet the stringent requirements of different applications. Some common applications include:
Piping and Pipeline Systems: Butt welds are widely used in the construction of pipelines for transporting liquids and gases. The seamless connection between butt-welded pipe fittings ensures structural integrity and prevents leakage.
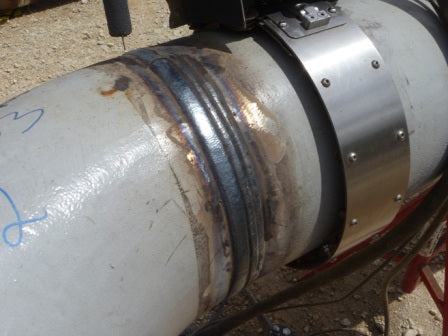
Pressure Vessels: Butt welding is often used in the fabrication of pressure vessels in industries such as chemical processing, oil and gas, and power generation. The welded joints provide the necessary strength to withstand internal pressure.
Structural Fabrication: In construction and structural engineering, butt welds are used when welding structural steel components, ensuring the stability and integrity of buildings, bridges, and other large structures.
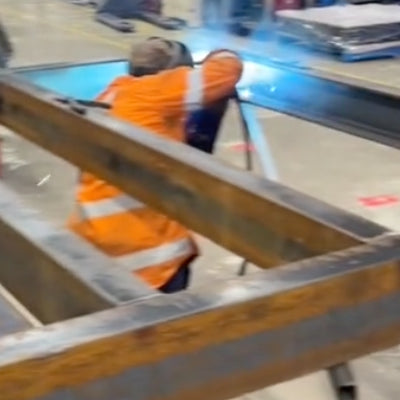
Butt Welds in Structural Fabrication
Photo by @j1ngles64 (TikTok)
Automotive Industry: Butt welding is utilized in the assembly of automotive components, including chassis and body structures. It contributes to the overall strength and safety of the vehicle.
Shipbuilding: Butt welds are prevalent in the shipbuilding industry, where they are employed in the assembly of various metal components, including hulls, decks, and bulkheads.
Pros And Cons Of Butt Welds
Like any other welding geometry, butt welding has its advantages and drawbacks. The benefits of butt welding are:
- Strong and uniform welds: Welds in the butt joint create a strong and durable bond, often achieving the full strength of the parent materials. The welded connection is integral and continuous.
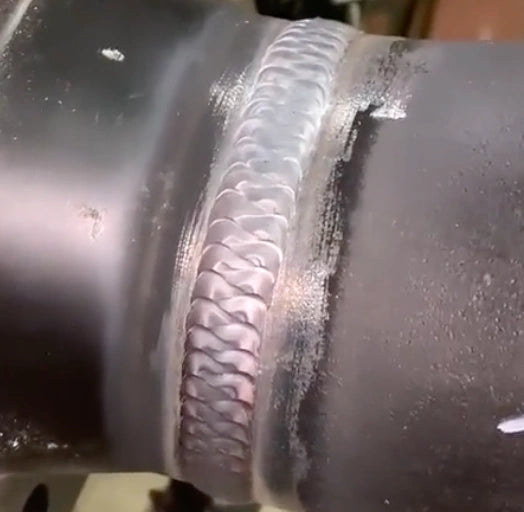
- Aesthetic appearance: Butt welding produces a flush and seamless joint, contributing to a neat and aesthetically pleasing finish, which is crucial in applications where appearance matters.
- Versatile: Butt welding is versatile and can be used to join a wide range of materials, including metals of different thicknesses and compositions.
- Efficient: The process of butt welding is relatively quick and efficient, making it a preferred choice for applications where speed and productivity are important. That's why in factories, butt welding has shown promising results.
- Reduced material waste: Compared to other joining methods that may involve additional materials like fasteners or adhesives, butt welding often results in minimal material waste.
- Suitability for high-pressure applications: Butt welds are well-suited for applications where joints must withstand high pressure, such as in pipelines and pressure vessels.
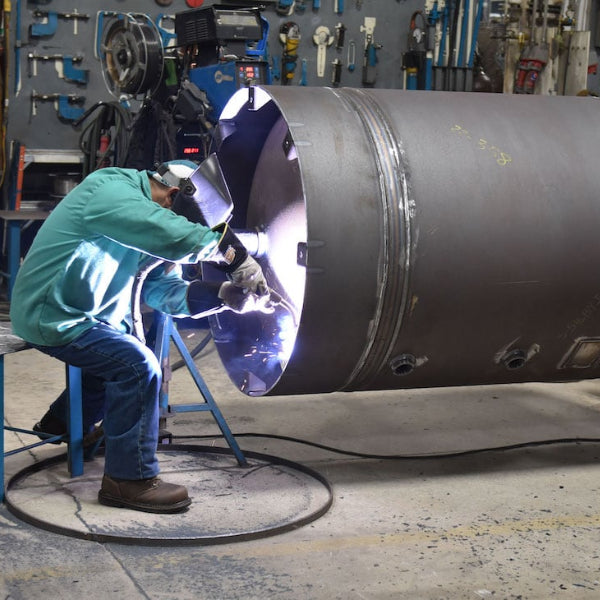
Source: https://www.bassettmechanical.com/news/safe-reliable-pressure-vessel-fabrication/
- Easy to weld: square butt joint is one of the easiest designs to weld on since gravity works for you. You can fill the joint and get proper penetration without reducing the heat.
- Easy to inspect: the simplicity of the design and geometry of butt joints also allows for easier inspection.
However, butt welding is not without its drawbacks, and it cannot be used in every application. The cons of butt welding are:
- Geometry challenges: Butt welding may be challenging in areas with limited accessibility, as it often requires access to both sides of the joint for welding. In specific applications, welding geometry can simply limit the versatility of this design.
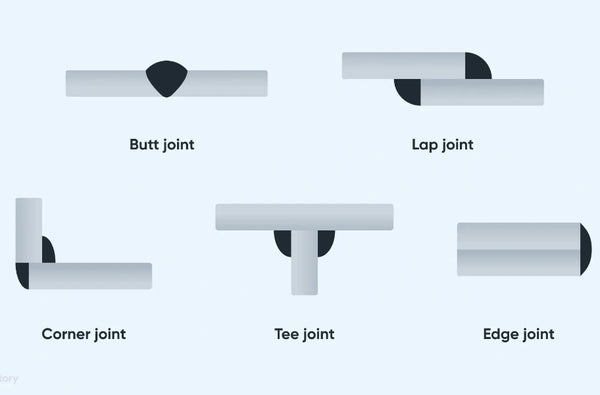
- Not suitable for thin materials: Butt welding is not always suitable for very thin materials, as excessive heat input can lead to distortion and burn-through. When thinner pieces of metal are joined, fusion welding methods without filler metal are used.
- Requires fixturing or backing: You will need to clamp or back the base metal before welding, as the plates can deform or distort as you apply heat. The heat-affected zone (HAZ) can also spread the heat of the melted metal area to the surrondings.
- Complex edge preparation on grooved welds: While square butt welds are easiest to perform and suitable for beginners, beveling thicker pieces in particular shape will require more expertise to achieve complete fusion and proper results.
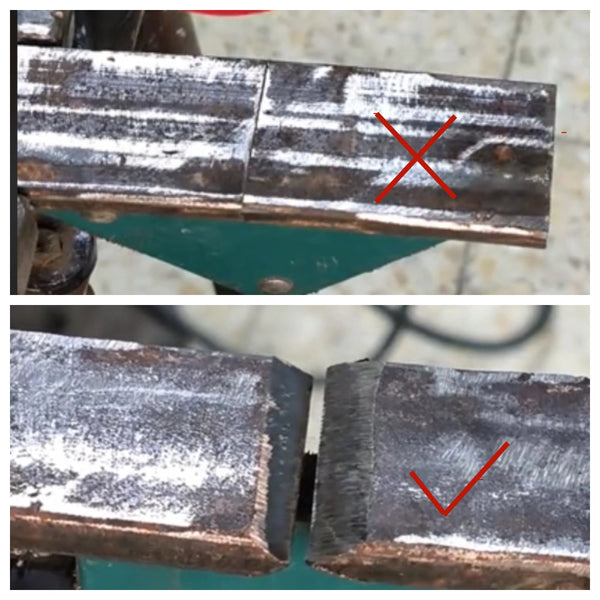
Conclusion
Butt weld joints are one of the most straightforward joint designs that will yield strong, reliable, and visually appealing welds. Welders use them in various applications, from structural and commercial welding through everyday tasks to hobby and DIY welding projects.
From simple, square butt weld joints to beveled edges, butt weld joint design can cover most of your everyday needs, whether it is on thinner metals or thick steel rails. Yes, they still have drawbacks, and their geometry is not suitable for all applications, but as a beginner, mastering the world of butt welding will open the doors for years of reliable welds with proper fusion and full penetration.
🧐Butt Welds Explained FAQ
1. What are types of butt joint?
A square butt weld and a beveled or groove butt weld are two commonly used techniques. Groove butt welds can be classified based on the appearance of their sides. These classifications include: single bevel butt weld, double bevel butt weld, single J butt weld, double J butt weld, single V butt weld, double V butt weld, single U groove butt weld, and double U groove butt weld.
2. What are the advantages of butt welding?
The benefits of butt welding are: strong and uniform welds, aesthetic appearance, versatility, efficiency, reduced material waste suitability for high-pressure applications, ease of welding, and ease of inspection.
👏 You may be interested in the following:
Leave a comment