Welding Wire For Aluminum Explained
Aluminum is a lightweight metal renowned for its versatility, durability, and corrosion resistance, which makes it widely used in various industries. However, many welders find welding aluminum a challenging task.
To successfully MIG weld aluminum, you will need to follow a couple of steps, and one of the most crucial ones is choosing the best aluminum wire. The choice of welding wire plays a pivotal role in achieving flawless welds, and in this article, we'll explain types of aluminum wire and their effect on the finished weld.
What Is Welding Wire, And Why Is It Used?
Welding wire is a filler metal that is commonly used in wire welding processes (MIG Welding and Flux Core welding). As the name states, wire is a slim metallic rod that creates the arc and fills the gap between two metals. Wire usually comes in coils or spools, and it is fed by a wire feeding system through a liner and MIG gun to the contact tip.
Welding wires can be divided into two groups: solid wires and flux core wires. Solid wires are used in MIG welding, and they require an external shielding gas, while flux-cored wires contain flux that shields the weld. These are some of the most straightforward explanations you'll need to understand if you are new to the world of welding, but if you wish to learn more, make sure you check out our MIG Welding Wire Types article.
If we look at the types of wires, they are usually separated into the group of metals that they are designed to weld. Therefore, you can find steel, stainless steel, and aluminum wires. Our topic today will closely turn to aluminum wires, their types, differences, and requirements for welding.
MIG Welding Aluminum Wire
MIG welding aluminum is one of the most straightforward methods for beginners and hobbyists since it requires less skill compared to TIG welding aluminum, which is often a go-to choice for professionals. When MIG welding aluminum, you will need a proper aluminum filler metal.
Now, this is easier said than done since aluminum alloys come in various grades, which then have different properties which you'll need to match with your wire. Matching the properties of two welded pieces and your wire is crucial in achieving a sound weld.
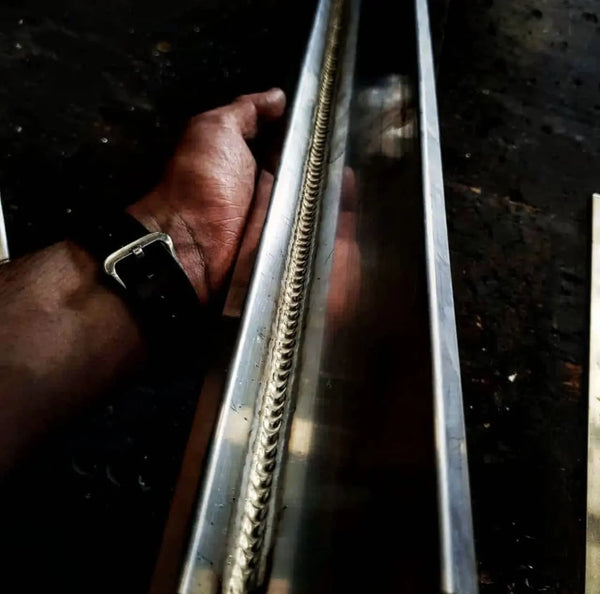
Photo by @woodweldfabrication (Ins)
However, on the good side, as a hobbyist or occasional welder, you are less likely to deal with specific or rare industrial aluminum grades, so choosing the correct wire for aluminum welding is not a daunting task. For your MIG welding process on aluminum, you are likely to use ER4043 or ER5356 aluminum welding wires.
ER4043 MIG Aluminum Welding Wire
ER4043 is a general-purpose, all-position aluminum welding wire. It is one of the oldest and most widely used welding and brazing alloys. You can use it to weld 2014, 3003, 3004, 4043, 5052, 6061, 6062, and 6063 aluminum alloys, which can be found in many common welding applications, such as bicycles, trucks, trailers, and automotive parts and equipment.
ER4043/1LB-0.8 1LB Spool .030" Silicon Aluminum MIG Welding Wire
This aluminum alloy usually contains 5% of silicon additives (AWS A5.10 specification allows 4.5-6%), which results in improved fluidity (wetting action) of the weld pool. High fluidity will allow you to achieve spray transfer and produce a weld less sensitive to cracking and a better appealing bead profile and bright weld.
As a hobbyist, you are likely to use .030 and 0.035 aluminum wires in 1-2 lb spools. But keep in mind that they come in industrial grade sizes such as up to 1/16" and spools larger than 10 lbs. However, you are less likely to use thicker wire than 0.035, as aluminum usually comes in thinner gauges.
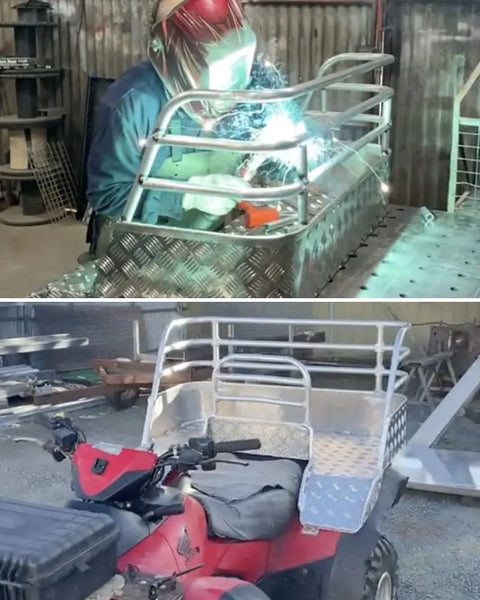
Typical mechanical properties of ER4043:
- Melting Range: 1065°F-1170°F (574°C-632°C)
- Ultimate Tensile Strength (psi): 21,000-33,000 psi
- Yield Strength (psi): 10,000-27,500 psi
- Percent Elongation in 2”: 5-12%
- Density: 0.097 lbs/in3
- Post Anodize Color: Gray
ER5356 MIG welding aluminum wire
ER5356 is another general-purpose aluminum wire that shows great versatility. As 4043, there are many common structural aluminum base alloys that can be welded with 5356. However, compared to ER4043, ER5356 wire usually contains 5% of magnesium additives (AWS A5.10 specification allows 4.5-5.5%).
ER5356/1LB-0.8 1LB Spool .030" Magnesium Aluminum MIG Welding Wire
The addition of magnesium to aluminum helps improve the weldability of the metal. This wire has a low melting point and strong weld penetration. This makes it ideal for welding thick materials or materials that are difficult to weld. Additionally, magnesium brings high shear strength and offers excellent corrosion resistance when exposed to saltwater.
ER5356 has a typical tensile strength is 29,000-45,000 psi (200 to 310 MPa), and a Yield strength is 12-30 Ksi (83 to 207 MPa). One of the advantages of 5356 filler wire is a much closer color match after anodizing.
Typical mechanical properties of ER5356 wire:
- Melting Range: 1060°F-1175°F (571°C-635°C)
- Ultimate Tensile Strength (psi): 29,000-45,000 psi
- Yield Strength (psi): 12,000-30,000 psi
- Percent Elongation in 2”: 10-18%
- Density: 0.096 lbs/in3
- Post Anodize Color: White
ER4043 vs. ER5356 Which One To Choose?
To help you make the right choice, here is a head-to-head comparison of crucial aspects of ER4043 and ER5356 wires.
ER4043 |
ER5356 |
|
Additives: |
5% silicon |
5% magnesium |
Weld puddle fluidity: |
higher fluidity |
good, but lower than 4043 |
Service temperatures: |
suitable for service temperatures above 150 Deg. F |
not suitable for elevated temperature applications |
Color match: |
dark gray after the anodizing process |
much brighter color after anodizing |
Typical tensile strength: |
21,000-33,000 psi |
29,000-45,000 psi |
Shear strength: |
lower shear strength |
high shear strength |
Softness: |
softer wire |
more rigid |
Weldability: |
a higher rating for weldability and slightly lower crack sensitivity |
rigid and easier to feed but with somewhat harder weldability |
Aluminum Weld Appearance: |
improved cosmetic appearance, smoother surfaces, less spatter, and less smut |
higher tensile strength and penetration for thicker pieces which might seem less appealing |
Welding Equipment For Aluminum Wires
Like its parent metal, aluminum wire has unique properties that make it harder to use and feed. Most importantly, the aluminum filler metal is soft, which makes it highly challenging to feed without interruptions, clogging, or bird nests. Therefore, you will need special welding equipment to achieve smooth wire feed, which is crucial for quality welds. Additionally, the wire must remain clean. Contaminated wire can affect the quality of the weld, even if you cleaned the aluminum oxide with stainless steel brush prior to welding.
Spool Gun
A spool gun is a unique piece of welding equipment that recently become mandatory when mig welding aluminum. A spool gun is a pistol grip-style gun with a compartment for a wire spool roll to be attached directly to the gun. This gun has an independent wire feeding system with drive rolls designed to feed the sensitive wires.
LBT150 150AMP Aluminum Welding Spool Gun
So why is the spool gun such a good accessory for aluminum filler metal? The main reason is the significantly shorter way that wire travels from the spool, through the gun, and into the weld. By shortening the course and applying higher wire feed speed, there are minimal chances that soft aluminum wire can tangle on its way to the weld.
As a result, spool guns became necessary for MIG welding aluminum today. However, there are a few drawbacks. The spool gun is limited to a 1 lb aluminum wire spool, and it can be heavy on the hand. As an alternative to weight and spool limitation, some use push-pull gun with added feeding system inside. However, like spool gun, these push-pull systems are considered an accessory you'll have to buy separately.
Graphene liner
Graphene liner is a cheaper alternative to a spool gun, which solves some of the issues with wire feeding. The liner is a tube or helically wound wire inside the torch that guides the filler wire through torch leads and into the weld. Typically, your MIG torch is equipped with a steel liner which is more than fine when MIG welding steel and solid wires. However, as the soft aluminum filler metal passes through it, it can get damaged or tangled, or an aluminum oxide layer on the wire can strip, resulting in contamination or poor wire feed.
SMX-1.0/1.2 Graphene Aluminum MIG WeldingWire Feed Liner
By replacing steel with a graphene liner, you eliminate most of the issues with aluminum wire feed. Even though the path between the spool and weld remains longer, the risks of wire tangling during the feed are minimal. Still, many don't find it as effective as a spool gun, but if you are on a tight budget, you can always consider it.
How to Change a MIG Gun Liner - YesWelder MIG 250 Pro
MIG Welder For Aluminum
Besides skill, MIG welding is an often preferred method for aluminum welding over TIG welding aluminum due to lower costs. The aluminum welding machine isn't the most complex piece of equipment, as you don't need fancy features or AC capability like with TIG. Equipment-wise, the main thing you should worry about when doing aluminum MIG is the wire feed.
Therefore, you will need a MIG welder that is spool gun compatible such as YesWelder MIG-205DS-BS, or a welder that supports high wire feed speed (450-750 imp for thinner wires and spray transfer mode). Most commonly, these are advertised as "MIG welder for aluminum" or "Spool gun compatible", so you cannot do too much wrong.
YesWelder MIG-205DS-B Multi-Process MIG Aluminum Welder
Unlike TIG, you can MIG weld aluminum alloys with DC polarity. Aluminum wires require DCEP polarity but also an argon shielding gas.
Source: https://yeswelder.com/blogs/yeswelder/how-to-setup-and-use-your-mig-welder-for-the-first-time
Here are typical MIG welding parameters that work with both ER4043 and ER5356 wires:
Diameter |
WFS (ipm) |
Amperage |
Volts |
Consumption (lb/100 ft) |
Argon (cfh) |
.030” |
480-625 |
60-175 |
15-24 |
0.65-1.25 |
25-30 |
.035” |
450-750 |
70-185 |
15-27 |
1.0-4.25 |
30-35 |
3/64” |
330-500 |
125-260 |
20-29 |
1.0-4.25 |
35-45 |
1/16” |
250-450 |
170-300 |
24-30 |
3.8-6.6 |
45-775 |
Can You Flux Core Weld Aluminum?
Theoretically, you can use flux cored arc welding method to join aluminum, but the technological solutions are still not commercialized or even used outside the laboratory. The main issue with flux core welding is the composition of flux that should protect the weld. The typical fluxes developed for stainless steel or mild steel are not chemically more active than aluminum, so the scientists had to start working on new ones.
The new types of fluxes were developed and presented in the labs that work on pure aluminum or aluminum alloys, but due to drawbacks, they never reached commercial use. These fluxes are very corrosive, so every bit of them must be removed from each weld pass before proceeding. Additionally, aluminum fluxes absorb water from the air, which makes storing extremely challenging. Finally, the chemicals in the fluxes are highly environmentally unacceptable.
Other possible issues with flux core aluminum welding emerge with the wire feeding and unpredictable weld results. The aluminum wires are fundamentally softer than solid wires, which makes them hard to feed. Making the wire hollow to fit the flux would make the feeding highly challenging and require special drive rolls and feeding mechanisms. Additionally, combining the fluidity of aluminum and the higher spatter of FCAW can result in very messy welds.
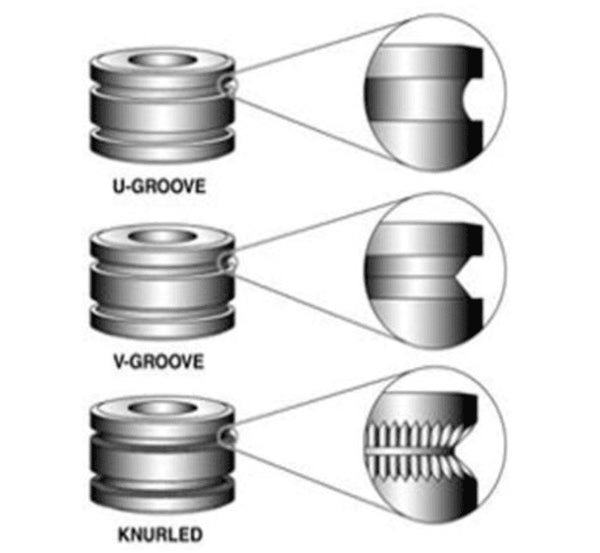
So even if it is theoretically possible, flux core arc welding is not a preferred method for aluminum.
Do Flux Core Aluminum Welding Wires Exist?
If you browsed the wire market, you might have come across the products advertised as "Flux core aluminum welding wire". If we take a look at the American Welding Society Filler Wire Specification By Material and Welding Process, we can see there is no match for Flux-cored arc welding and aluminum.
Therefore, it is clear that there is yet no flux core welding wire for aluminum that would have its composition and properties specified by AWS or any reputable organization. Even if you find and buy this kind of wire, there is no guarantee you will successfully flux core weld aluminum without tangling, wire burning, spattering, or burning through. That's why we recommend sticking to traditional aluminum welding wires and methods such as MIG or TIG.
Conclusion
Welding wires are an essential part of any weld, and when welding aluminum, you will need to choose a filler wire with similar composition and properties to the base metal. Even though there are various grades of aluminum, as a hobbyist, you are likely to use ER4043 or ER5356 wires. These are both general-type, all-position welding wires that provide good results and desirable weld properties on a wide variety of aluminum alloys, and the choice will differ on specific applications.
The main issue with aluminum welding wires is feedability. Aluminum wires are soft, so they require specialized equipment such as a spool gun, push-pull system, or specific liners. These are considered accessories, which means they are an added cost, but the overall investment is significantly lower compared to TIG.
🧐Welding Wire For Aluminum Explained - FAQ
1.What is ER4043 MIG aluminum welding wire?
ER4043 is a general-purpose, all-position aluminum welding wire. It is one of the oldest and most widely used welding and brazing alloys. You can use it to weld 2014, 3003, 3004, 4043, 5052, 6061, 6062, and 6063 aluminum alloys, which can be found in many common welding applications, such as bicycles, trucks, trailers, and automotive parts and equipment.
2.What is ER5356 MIG aluminum welding wire?
ER5356 is another general-purpose aluminum wire that shows great versatility. As 4043, there are many common structural aluminum base alloys that can be welded with 5356. However, compared to ER4043, ER55356 wire usually contains 5% of magnesium additives (AWS A5.10 specification allows 4.5-5.5%).
3.ER4043 vs. ER5356 Which One To Choose?
ER4043 |
ER5356 |
|
Additives: |
5% silicon |
5% magnesium |
Weld puddle fluidity: |
higher fluidity |
good, but lower than 4043 |
Service temperatures: |
suitable for service temperatures above 150 Deg. F |
not suitable for elevated temperature applications |
Color match: |
dark gray after the anodizing process |
much brighter color after anodizing |
Typical tensile strength: |
21,000-33,000 psi |
29,000-45,000 psi |
Shear strength: |
lower shear strength |
high shear strength |
Softness: |
softer wire |
more rigid |
Weldability: |
a higher rating for weldability and slightly lower crack sensitivity |
rigid and easier to feed but with somewhat harder weldability |
Aluminum Weld Appearance: |
improved cosmetic appearance, smoother surfaces, less spatter, and less smut |
higher tensile strength and penetration for thicker pieces which might seem less appealing |
Leave a comment