Improving FCAW With Gas - Gas Shielded Flux Core Welding
Flux-cored arc welding (FCAW) is one of the newer welding methods introduced in the 1950s, and it was developed as a combination of MIG welding and Stick welding. This welding process provides ease of use of MIG welding and the ability to weld without shielding gas, like with MMA (or Stick welding process).
However, the inventors didn't stop there. They found ways of improving FCAW with gas, resulting in dual shield welding or shielded Flux-cored arc welding. This highly versatile and productive welding method is valued for its speed and high deposition rates, which we'll explain thoroughly in this article.
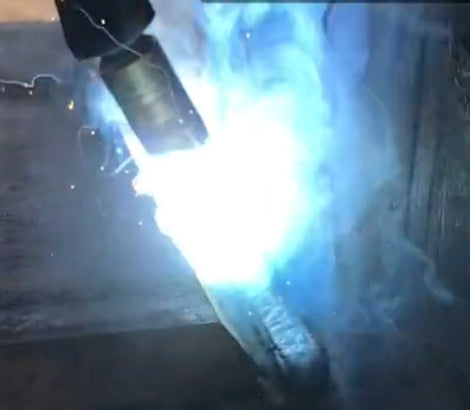
Fundamentals Of Flux Cored Arc Welding
Flux-cored arc welding (FCAW) is a semi-automated welding process that combines the advantages of Gas Metal Arc Welding (GMAW) and Shielded Metal Arc Welding (SMAW). This process utilizes the heat of an electric arc to melt and fuse base metal and flux-cored wire. A tubular electrode filled with flux is automatically fed into the welding joint.
Since it uses the same semi-automated feeding principle and typically the same welding machine as MIG welding, FCAW is considered easy to use and master. Meanwhile, a Flux-cored electrode wire is similar to a Stick electrode. Unlike solid wire, continuous wire-fed electrode has a layer of flux that protects the weld pool from contamination without needing external shielding gas.

As a beginner and hobby welder, you have likely seen or used FCAW with your MIG welder. However, there are ways of improving FCAW welding with gas.
Dual Shield Welding (Flux Core Welding With Gas)
Flux-cored arc welding can be improved by introducing a shielding gas and using special gas-shielded flux-cored wires. This welding wire is specifically designed to work with gas but also has a tubular filler wire core filled with flux.
Like regular FCAW, a continuously fed tubular electrode produces a welding arc and melts the pieces into the weld joint. But with dual shield welding, molten metal is protected by both flux from filler metal and external shielding gas, typically 100% carbon dioxide or a mixture of 75% Argon and 25% CO2.
The wire adds the desired level of alloy elements to the puddle, which affects the structural properties of the weld metal. Meanwhile, dual shielding protects the molten pool from atmospheric contamination, transfers the desired heat, and provides arc stability.
Unlike self-shielded FCAW, most dual shield welding wires, like MIG, will require DCEP or DC+ polarity. DCEP will produce more heat on the tip of the electrode, which will intensively melt more wire to ensure high deposition rates. This way, you can achieve the desired spray transfer while the heat is transferred back to the weld joint, creating high penetration and high-quality welds.
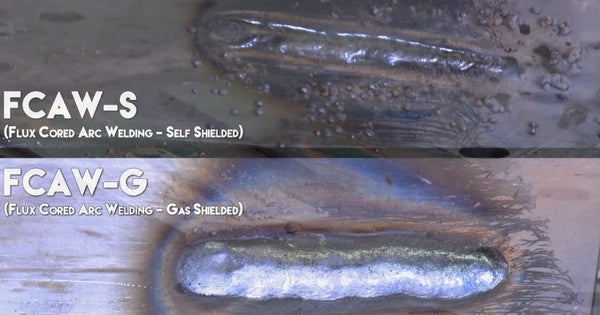
Why Do Welders Use FCAW With External Shielding Gas?
Since most welders use FCAW for simple on-field repairs or once they need to get the job done quickly without dragging a gas cylinder around, many wonder why you even use dual shielded flux core. This welding method was primarily developed for welding structural steels in applications requiring high speed, penetration, and deposition rates.
In identical welding parameters, shielded FCAW provides welds with more consistent mechanical properties and fewer defects than Stick or MIG/MAG welding processes. This welding operation is suitable for thicker metals that require more heat. Compared to MIG and Stick, gas shielded Flux Cored arc welding is more suitable for all position welding.

Weldable Materials
Dual shield welding will work well with most carbon steels, cast iron, stainless steel, and hard-facing/surfacing alloys. The method was developed for structural steel, showing the best results when working on it.
Meanwhile, most gas-shielded flux-cored wires are not developed for non-ferrous materials or exotic metals such as aluminum, magnesium, and nickel alloys. While that's also common for regular FCAW, MIG and MMA, have classified electrodes and filler wires for it.
Advantages Of Dual Shield Welding
Like other processes, dual shield or double shielded FCAW has its good and bad sides. The advantages of dual shield welding include:
- High deposition rates
- Deep penetration
- Easy to use
- Regular welding equipment
- Good for out-of-position welding
- Cost efficient
- Good weld quality and appearance
So, let's discuss the advantages thoroughly.
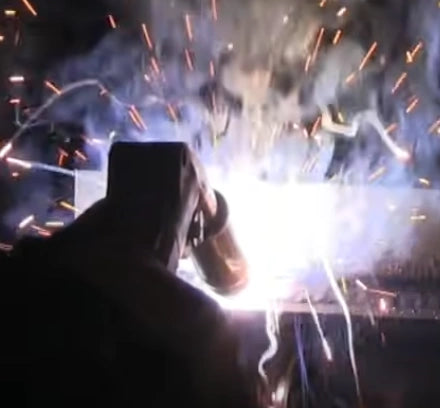
High Deposition Rates
Dual Shield flux-cored wire electrodes have relatively high current density, which affects the overall deposition rates. The resistance heating is concentrated in a minimal area due to the thin primary current path, so the flux-cored electrode quickly reaches its melting point.
With the added DCEP polarity, the heat is also focused on the tip of the electrode. As the wire reaches the melting point quickly, it is easier to achieve the spray transfer that is known for its welding speed. Besides speed, spraying droplets also transfer more heat, resulting in higher penetration.
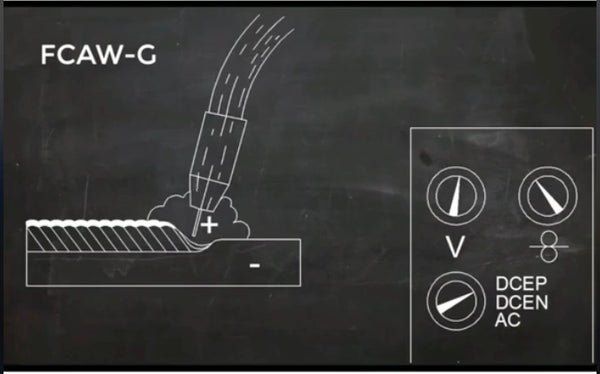
Deep Penetration
A thin cross-sectional current path creates a more columnar pattern of an arc, which leads to deep penetration. In addition, the combination of flux and shielding gas in dual-shielded FCAW allows for deep penetration into the base metal. Adding shielding gases such as CO2 creates maximum penetration, which is suitable for thicker materials.
Deeper penetration also increases the effective throat of a fillet joint. If the effective throat of the fillet is increased because of deep penetration, the strength of the joint is not dependent as much on the exterior size of the weld.
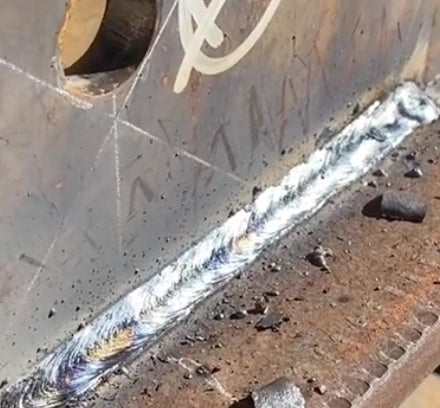
Easy To Use
Gas shield welding is a semi-automated process that is easy to master and use. You dial in the wire feeder and voltage, and the machine keeps it consistent throughout the process. The wire is fed automatically, so you have a free hand, and you can focus on your welding technique.
The practice has shown that training a new welder to weld in all positions with flux-cored electrodes is much easier compared to other welding processes. Employers always appreciate less time to prepare and lack of poor weld quality, but also beginner welders who want to get into the world of welding.
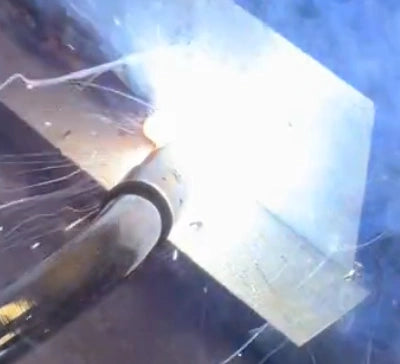
Less Specialized Equipment
Running a dual shield flux wire doesn't require fancy or expensive welding equipment. However, there are specific precautions you should keep in mind.
Firstly, you should know that gas-shielded flux wires often come in larger diameters, such as .045" and higher, so you should make sure your wire feeder can support it. The wire feeder should have knurled rolls that can feed soft, tubular wire. A welding gun should have a good liner to provide smooth feed, which is essential for good results.
Luckily, most reputable brands today, including YesWelder, make their MIG/Flux core machines with reliable feeders and high quality to provide adequate wire feed.
Suitable For Out Of Position Welding
Welding in flat and horizontal positions is considered straightforward, but things get tricky once you have to weld vertically or above your head. Solid wires in overhead and vertical welding require lower diameters and less heat to reduce the pool fluidity, allowing it to fill the joint and fight gravity correctly.
Meanwhile, gas-shielded flux wires have a fast freezing slag that holds the weld puddle or weld pool in place. As a result, you can use these wires for higher welding currents in out-of-position work to maximize the penetration and ensure proper fusion. Fast-freezing slag will solidify fast, so a molten puddle won't drip or escape the joint.
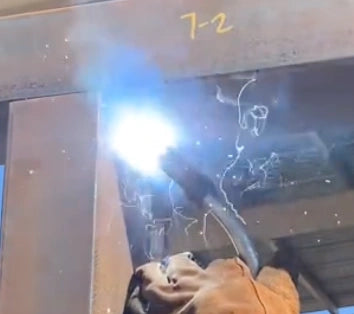
Cost Efficient
High deposition rates with deep penetration and less time for training and rework in out-of-position welding means higher cost efficiency of dual shielded FCAW wire. For you as a hobby welder or beginner, this might be less impactful, as it will take time to justify the investment.
However, even the slightest saving in filler material can positively impact the overall costs in large-scale welding and industrial applications. By saving on training time and welding time, large-scale manufacturers can notice long-term cost savings that are essential and presented by choosing the right filler metals.
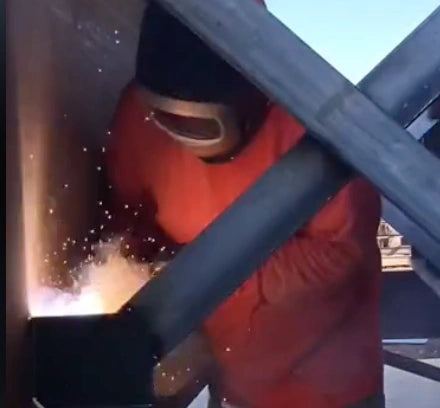
Good Weld Quality
A gas-shielded flux core produces a good weld quality with smooth beads with almost no ripple. With proper parameters and technique, you can achieve uniform welds with good tie-in and very little spatter, significantly reducing clean-up time.
As we noted in part about the ease of use and costs, the best part about this process is that you can achieve visually appealing welds even with less experience and time spent on training. This is also good for your confidence as an absolute beginner because getting beautiful welds with little time spent training is always satisfying.
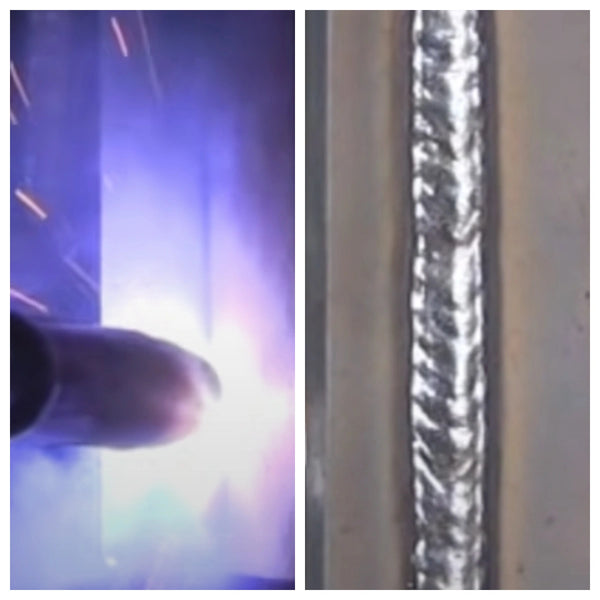
Drawbacks Of Gas Shielded Flux Cored Welding
While there are a lot of advantages and reasons to use dual shielded wires, you should also know there are specific drawbacks. The most notable disadvantages of the gas-shielded FCAW process are:
- High initial cost: Gas-shielded FCAW wires are initially more expensive than regular flux-cored wires. Even though they show cost-saving advantages in large-scale applications, they can be costly for occasional hobby or DIY welding projects at home. Also, adding a shielding gas can also present an additional cost, but since you can use pure CO2, these costs are lower.
- Only for some outdoor uses: Using a shielding gas covering in outdoor applications is not always the best, as the wind or draft can easily blow away the shielding. Poor shielding is a primary cause of defects such as porosity, spatter, etc., so you want to return to the FCAW process when working on-field jobs.
- Proper storing: Like some SMAW electrodes, gas-shielded FCAW wires need to be stored more carefully. Moisture and atmospheric contaminants can damage the flux protection, once again causing imperfections and inclusions.
- Harmful Gases: Flux melting can create toxic fumes and poisonous gases. Remember that when welding in confined spaces, and ensure proper ventilation to keep yourself safe.
- Not for thin materials: Deep penetration and high deposition rates do not mix well with light gauge metals. That's why most wires also come at larger diameters and require higher heat. Adding gas to improve FCAW on thin pieces will result in burn-through or distortion.

Tips On Improving The FCAW With Gas
- Make sure you clean slag formation after every substantial pass.
- Store your wire carefully.
- Choose the filler material diameter and composition based on the type and thickness of the base metal.
- Increase welding travel speed when working overhead or on vertical welds.
- Knurled drive rolls ensure smooth wire feed with soft flux-cored wire
- When welding thinner metals, go vertically down to reduce penetration. For metals thicker than 1/4″, weld up to promote penetration.
- When welding significantly thick materials, add pure CO2 shielding method to boost penetration and heat transfer.
- Choose 75% argon and 25% carbon dioxide when weld aesthetics and appearance are more important.
- When working inside, make sure there is adequate ventilation to avoid harmful gases from shielding and flux piling up.
- Ensure proper shielding gas flow to prevent a lack of shielding or overshielding that attracts contaminants into the joint.
- When working with flat welds, weld at 90 degrees and 10 degrees back. For T Joints, the angle should be 45 degrees, while Lap joints require welds at 60-70 degrees.
- Limit wire stick out to avoid excessive spatter.
-
Secure the high-pressure gas cylinder to prevent it from falling or becoming damaged.
Conclusion
Dual shielded Flux-Cored Arc Welding (FCAW) stands out as a versatile and efficient welding process. Its flux-cored electrode and external shielding gas combination provides welders with increased deposition rates, deep penetration capabilities, and adaptability to various materials and welding positions.
This makes it a preferred choice for applications requiring productivity, out-of-position welding, and cost-effectiveness. The self-generated shielding gas and flux properties contribute to reduced post-weld cleanup, enhancing overall efficiency. Dual-shielded FCAW continues to be a valuable technique, offering a balance of performance, flexibility, and cost-effectiveness in diverse welding scenarios.
🧐Improving FCAW With Gas - Gas Shielded Flux Core Welding FAQ
1. What is dual shield welding?
Dual shield flux-cored arc welding improves upon regular FCAW by using a tubular electrode filled with flux and shielded by both external gas and flux. This combination enhances weld quality, structural properties, and deposition rates, producing high-penetration, high-quality welds with DCEP or DC+ polarity.
2. What are the advantages of dual shield welding?
The advantages of dual shield welding include:
- High deposition rates
- Deep penetration
- Easy to use
- Regular welding equipment
- Good for out-of-position welding
- Cost efficient
- Good weld quality and appearance
👏 You may be interested in the following:
Leave a comment