How to stick weld different thickness metals
Stick/Arc welding is one of the oldest methods, but it still finds its way into various industrial applications such as pipeline, structural welding, heavy-duty repair, and many more.
Even though there are more advanced welding processes today, Stick welding is many welders' favorite due to its ease of use, versatility, high deposition rates, and low expenses.
Besides industry, hobbyists, DIYers, and small shop owners also love the Arc welding process. However, those less experienced often ask how to weld different thickness metals.
In this article, we will explain how Stick welding deals with a thin metal, medium metal thickness, and thick stock and what you will need to weld it successfully.
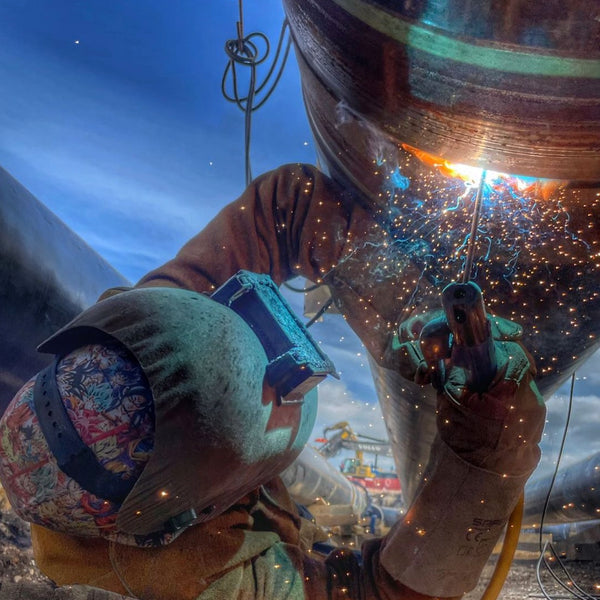
Photo by @welding_land
Stick Welding Different Thickness Metals
Stick welding is a straightforward process that doesn't require too much skill or special equipment like TIG welding processes, and it can be used to weld on the field in windy conditions. Stick electrodes have a layer of flux that protects the weld puddle from contamination and can burn through rust, paint, and dirty metals.
With added high deposition rates and low costs, it is not a surprise why Stick welding is a go-to method when project or repair work needs to be done quickly and cheaply. However, appearance-wise, stick welding cannot match significant TIG welds.
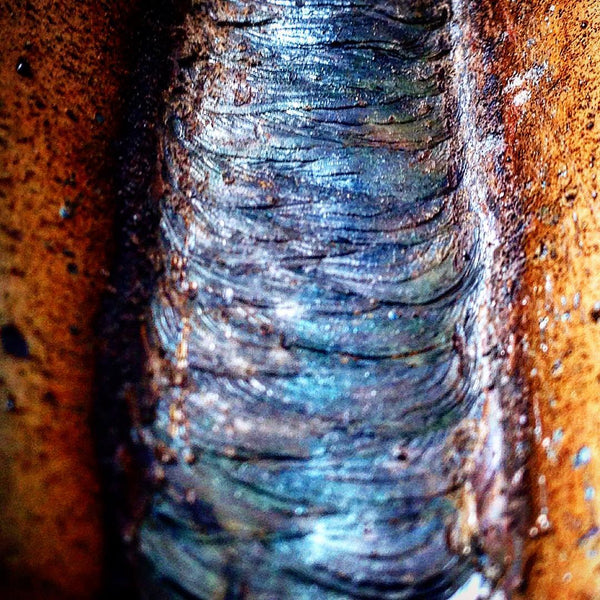
Photo by @arc_trainer
Regarding the different thickness metals, Stick welding does exceptionally well with medium-thickness and thick metal, but it is less commonly used to weld thin metal. No features could limit the heat output like in MIG welding or TIG welding processes, but higher penetration handles thick metal very well.
Let's see what you need and how to weld different metal thicknesses using Stick welding.
Stick Welding Thin Metal
Stick welding thin metal, or any metal thinner than 1/8″, is quite challenging, and even if you do everything right, there is no guarantee that you will succeed. The sole reason is the heat output of stick welding, which is rarely lower than 20-30 amps. In addition, there are no features such as pulsed MIG or TIG, which would help you to limit the heat-affected zone within the thin metal.
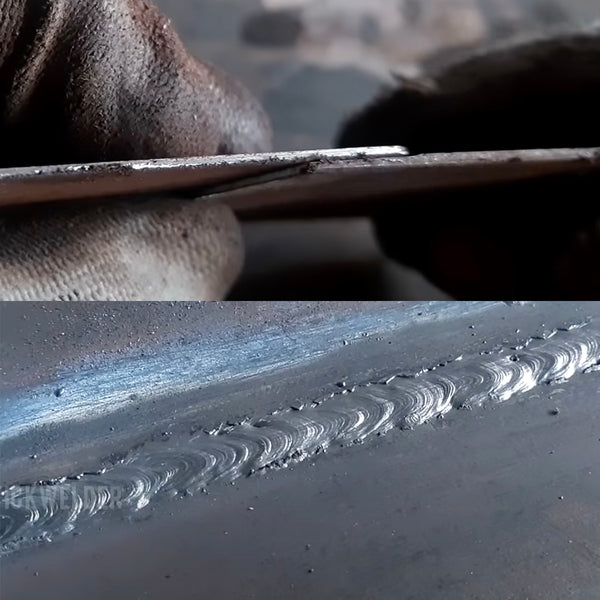
6013 Rod 2.0mm with 55 AMP DCEP
Source: https://www.youtube.com/watch?v=w1_MEx8CU-A
As a result, you might encounter wrapping, burn-through, or distortion. In addition, you might have an issue with starting an arc due to low amperage, and the solution is to increase it, which works against welding thin metals.
However, some practical advice might help you with higher gauge sheet metal.
Stick Welding Equipment To Weld Thin Metal
Like other welding methods, you won't need the most powerful Stick welder to weld thin sheet metal. Instead, you can do it with a YesWelder ARC-125DS DC Stick welder, rated at 20-125 amps with an easy arc start technology.
This feature can help you compensate the power for the low amp start that you will need for thin mild steel. You will need to set the machines low enough not to burn through base metal but still high enough to get an arc start.
ARC Welder 125A Stick Welding Machine | YesWelder
The next step will be selecting the right Stick welding rod. You don't want to go higher than 1/8″ or 1/16″ diameter electrodes, as they will extend the heat-affected zone, leading to wrapping or distortion. You should use an E6011 or an E6013 rod for the best results.
E6011 rod is more suitable when you don't need good-looking welding in thin or sheet metal, and they work well with painted, rusted, or dirty metal. However, E6013 rods show better results when the weld appearance is essential, but they require an adequately cleaned surface. In addition, 6013s offer a bit more shallow penetration compared to 6011s.
Choosing the right polarity is as important as matching filler metal. For thin metals, DCEN (Direct Current Electrode Negative or DC-) is the better choice as it offers lower penetration compared to DCEP. With DCEN, the electrode holder is connected to the negative side (-) connection of the welder.
Weld Preparation And Welding Method Required To Weld Sheet Metal
While SMAW is known for excellent results when welding through dirt or rust, you want to clean surfaces when dealing with thin metals, especially when working with E6013 electrodes. Also, leaving a large gap is not recommended, as pieces will distort, so a nice fit-up is required.
Since it is challenging to control heat input with SMAW, you will need extra attention with thinner material. That explicitly applies when using longer welds. Using the skip welding technique with a number of intermittent or stitch welds can help minimize distortion and evenly distribute the heat.
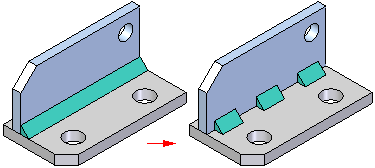
Source: http://www.soliddna.com/SEHelp/ST5/EN/i_v/stchweld1c.htm
In addition, you can clamp the pieces and use tack welds with an added backing bar that can serve as a heat sink. Sometimes electrodes can coil up and down, so you could use the used electrodes or provide tighter support. Going slow will result in a burn-trough, but you should do more than run through the weld.
In the end, welding thin materials with Shielded Metal Arc Welding comes down to finding a sweet spot where the electrode would ignite but perform without burning holes through pieces.
Stick Welding Medium-Thickness Metal
Stick welding is one of the best, moderately straightforward, and cheapest methods to weld medium-thickness mild steel. These applications usually include on-field repairs, maintenance, farm work, and hobbyist and DIY work.
As a medium-thick metal, we consider plates up to 1/4” or 1/2" since you will rarely get a chance to weld anything thicker than that in your shop. Stick welding medium-thickness metal is certainly more forgiving than welding sheet metal, but you will still need some time to master the technique for the best results.
Without further ado, let's see what to do with medium-thickness weld metal.
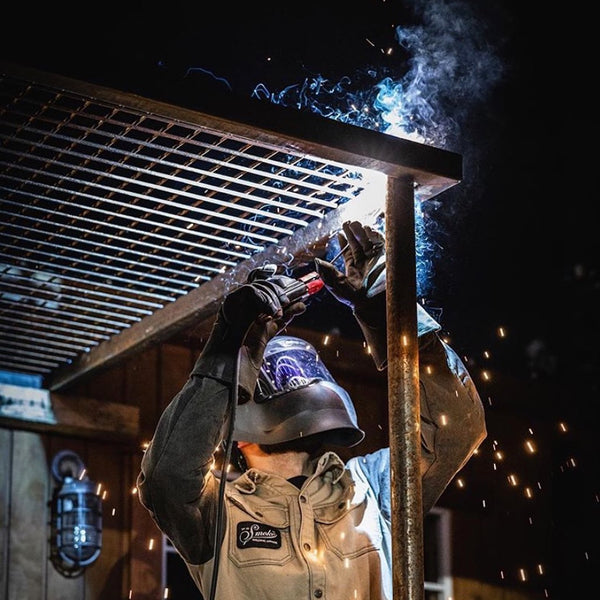
Photo by @upinsmokeweldingapparel
Equipment For Medium-thickness Metal
The best part about medium-thickness metal is that you can weld it with an ordinary 160 amp stick welder, which is usually cheap. So our top pick is undoubtedly the YesWelder YWA-160 IGBT Inverter Stick welder.
This lightweight, portable and affordable machine can be used to weld up to 5/32" steel when plugged into a 220V outlet. Besides the attractive price tag, this machine is packed with features such as Arc force, hot start, and VDR protection to help you deal with your everyday medium-duty projects. These features will help you start and maintain the stable arc from the start to the end of the application, which is crucial for the highest quality Stick welds.
Filler Metal (Electrode) Selection
As the thickness of the base metal increases, you will need to use a larger diameter Stick electrode. The correct stick welding rod size is the largest one that fits in the joint, ensuring proper penetration and fusion, the most common being 1/16, 5/64, and 3/32. Like with TIG welding, you want one step thinner electrode than the base metal. For example, 1/8″ metal will require a 3/32″ rod.
You have more room to select the electrode type than sheet metal welding, with commonly used 6010, 6011, 6013, and 7018. The best part is that the properties of the electrode can match your projects perfectly. For example, if you need more heat, you can use E6010, while E6011 provides a soft arc, minimal spatter, moderate penetration, and easily removable slag.
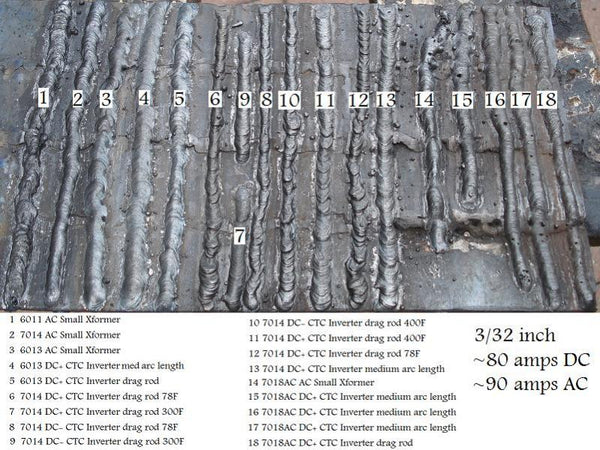
Source: https://weldingweb.com/vbb/threads/44592-Learning-to-Stick-Weld
As a beginner, consider starting with rutile rods such as E6013 and E7014. They provide significantly more forgiving results than cellulosic rods, such as E6011, or low-hydrogen rods, such as E7018. However, rutile rods offer lower-quality results, but you can use them to work your way up to mastering more challenging electrodes.
You should pay attention to the electrode polarity when making a selection. For example, particular electrodes, such as E6010, are designed for DCEP only, while its alternative, E6011, can work with both AC and DC current.
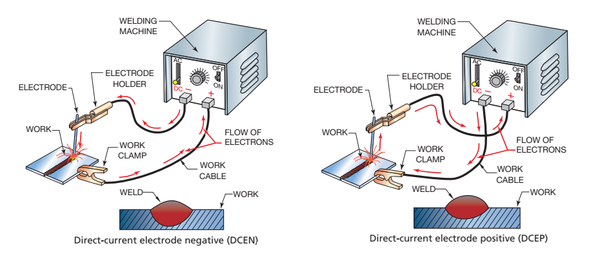
Source: https://amarineblog.com/2019/09/03/welding-current-types-dcen-dcep-ac/
In addition, keep in mind that inverter-based Stick welders can have issues with 6010s, causing inconsistent results with a highly unstable arc. Fortunately, that's not the case with YesWelder YWA-160, which is one more reason to recommend it.
Welder Settings For Medium Thickness Metal
The current and polarity should be the first thing you should consider when setting your welder for medium-thickness steel. Current and polarity settings will vary on the selected electrode and overall project requirements.
For example, DCEP (DC+) current runs 10-15% hotter compared to DCEN (DC-) and AC. Therefore, welding medium-thickness metal will, in most cases, require DCEP polarity. DCEN, as we said, is more useful in thin metal welding, while AC is commonly helpful when an arc blow occurs.
Arc blow is a specific welding issue that you might notice if the arc wanders off from the weld puddle due to the magnetics or thermal properties of the base metal. So if you feel like you cannot control it, you should switch to AC current, of course, if your stick welder and electrode allow it. However, welding with AC offers relatively low penetration, and alternating from the positive to the negative side can cause the arc to extinguish.
Next, you will need to select the correct amperage. The amperage is usually stated on the box or enclosed materials of the electrode package. In addition, you can use a rule of thumb that says 1 amp for each .001-inch electrode diameter.
Low amperage will cause the electrode to stick excessively to the piece, eventually resulting in arc stuttering. Conversely, high amperage makes the weld pool extremely fluid and almost uncontrollable, with high arc sounds. While it is less likely to burn through medium-thickness metal, you should still pay attention.
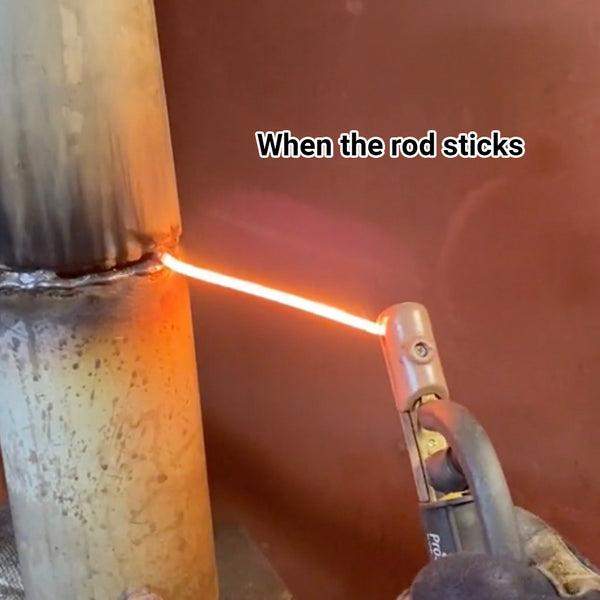
Photo by @coinsiieweldz
Weld Preparation And Welding Technique
Stick/Arc welding thicker metal certainly allows more weld preparation and design options, as pieces can be placed in horizontal, vertical, or overhead positions, with T-joint, butt weld, corner joint, and many more. Even though SMAW is much more tolerant of dirt, oil, or rust, cleaning the pieces is always a good practice.
Regarding the welding technique for medium-thick metal, there are certain guidelines but no specific rules. Therefore, SMAW allows welders to develop their own style and electrode manipulation as long as they follow specific steps.
Stick electrodes can be run using a stringer or straight bead, or weaving technique. Metals up to 1/4" usually don't have a large gap, so it is not necessary to weave with medium-thickness metal. Instead, you should pay attention to arc length, travel angle, and travel speed.
The arc length represents the distance between the electrode and the puddle. As a rule of thumb, it should not exceed the diameter of the core of the electrode. If you keep the electrode too close, it will stick and extinguish. Meanwhile, lifting it way up high will cause spatter, porosity, or undercut.
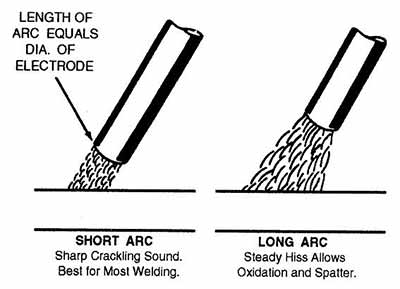
Source: https://www.cruxweld.com/blog/five-steps-to-improving-your-stick-welding-technique/
The travel angle is similar to other welding techniques, and it includes holding the electrode at 5-15 degrees and dragging (backhand) technique in horizontal and flat positions. Vertical up welding requires a push technique at 0 to 15 degrees.
Travel speed should be adjusted to the thickness of the metal. Low travel speed creates wider weld beads with shallow penetration. The electrode isn't fusing the two pieces; it just sits on top of the base metal. Meanwhile, fast travel speed creates narrow weld beads, again, with penetration problems and fear of undercut or underfill.
As a beginner, it might take time to master proper electrode manipulation, travel speed, and arc length, which is a reason SMAW is a bit more complex than MIG welding but still not as hard as TIG welding. However, once you master the technique, you will enjoy the versatility of successfully and quickly welding medium-thickness steel without shielding gas.
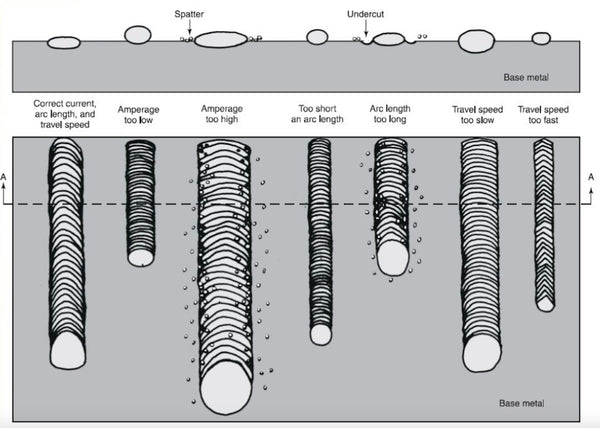
Source: https://slideplayer.com/slide/4214975/
Stick Welding Thick Metal
Stick welding is one of the most suitable and widely used methods for joining thicker metal in farm and ranch, on the field, and in plant maintenance and repair, pipeline welding, and shipbuilding applications. You should already know the reasons - high deposition and penetration, with low costs.
Welding 3/16" inch metal and larger with SMAW will require beveling the pieces and using multiple passes. While the same thing applies to any welding method, Stick and Flux core (Dual Shielded flux core) are the most cost-efficient processes to do so.
So, let's explain how it is done.
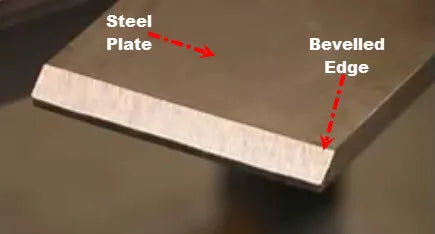
Source: https://slideplayer.com/slide/4214975/
Welding Equipment For Thick Stock
The main advantage of beveling the pieces is bringing a 1" to a reasonable gap of 1/8" or 1/4". At that point, you can use a typical 160-200 amp rated stick welder. If you browse the market, most industrial-grade stick welders don't have a high-rated output like with MIG or TIG machines.
Therefore, you can use the YesWelder ARC-205DS to weld thicker pieces successfully. The good side is that you can use the notorious 6010s, which are usually a must-have for root-pass on the thicker piece. The welder for industrial applications should have a high-duty cycle, allowing the welders to complete a single pass in one run.
Nonetheless, home-repair applications that include welding thick stock will be more than manageable with the 60% duty cycle that ARC-205 offers.
Electrode Choice
Stick welding thick plates will require a manageable size of electrodes since you are bringing the root at a reasonable thickness. As a result, you will need a 1/8-inch or 5/8-inch rod for the first, initial, or root pass and a 5/32 or a 3/16-inch rod for filler and cap passes.
To weld the root pass, an all-position cellulose E-XX10 welding electrode is used (6010, 7010, 8010). The standard travel speed is 12 inches per minute, with reverse (DC+) polarity. This approach creates a strong foundation for the upcoming welds with slag that easily falls off. If, in any case, an arc blow occurs, you can switch to its smaller-brother 6011s, which works with AC current, but offer somewhat weaker results.
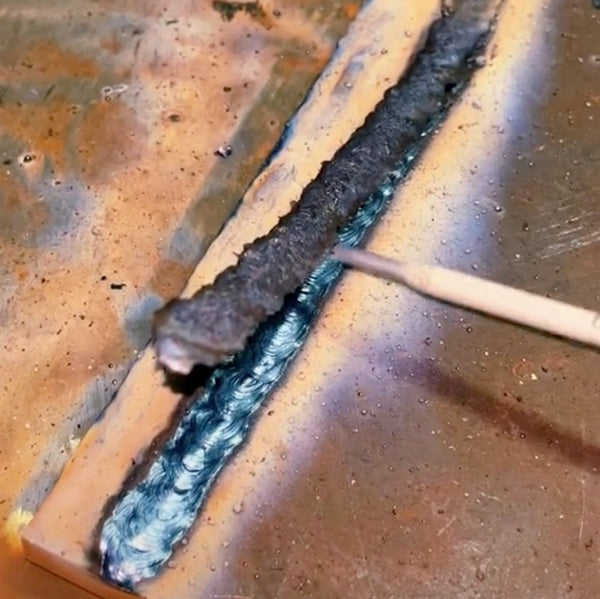
E6013 Slag Peels Photo by @darrinolszko
Upcoming fill and cap passes are usually done with E-7018 low-hydrogen electrodes. This is because 7018s produce strong, ductile welds that fill the opening nicely, making them the backbone of structural welding.
Weld Preparation For Thicker Pieces
Weld preparation for thicker piece welding is nearly as important as welding itself. For plates up to 3/16" thick, you should use a V-bevel to prepare the pieces. 1/2" to 3/4" pieces will require a U-bevel, which can take more filler metal to ensure stronger welds. Finally, pieces thicker than 3/4 inch will need a double V or U-bevel joint configuration.
The gap should be even along the entire piece of plate or pipe, and aligning the parts is crucial. Of course, cleanliness should be disregarded. Once aligned, you can use tack welds to keep everything in place, so you can start welding.
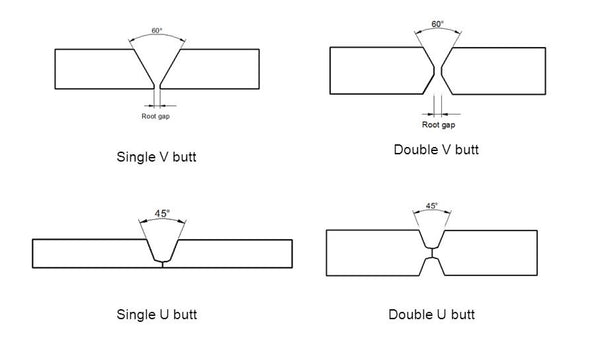
Source: https://slideplayer.com/slide/4214975/
Multi-pass Stick Welding Technique
Compared to medium-thickness plates, thicker pieces now have a larger gap between them, so you will have to use a weaving manipulation with a pushing technique for 3/16"-1/2" V bevels or a pull technique for U bevels larger than 1/2" to fill it correctly and get the solid weld bead. The weaving procedure requires more time and practice to perform. However, you can practice by clamping a pen in your electrode holder and drawing on a piece of paper.
Even though the 6010s produce a slag that easily falls off, cleaning it thoroughly before performing any other passes is crucial. Any leftover slag can cause slag inclusions that can interfere with the integrity of the weld, and they are hardly noticed without x-ray or ultrasonic testing.
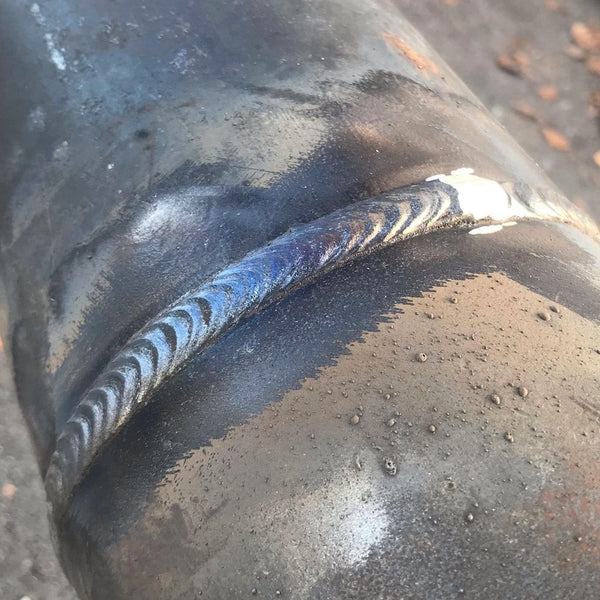
Weld with E6010, Photo by @sissou.san
After a root pass, you can opt to put a hot pass, performed within 5 minutes after completing the initial weld. The hot pass is used to correct some imperfections noticed in the root pass, taking 5-10% more heat to penetrate the first pass.
Laying a foundation is a crucial part of making the strongest stick weld on the thick metal, and afterward, you will need to fill the gap. The filler pass is done with smaller diameter E7018 rods, but you can use any convenient electrode manipulation method.
Highly skilled welders usually use weaving techniques for cap weld to produce high-aesthetic TIG-like welds. However, you will be more than fine with a simple finish with 7018s.
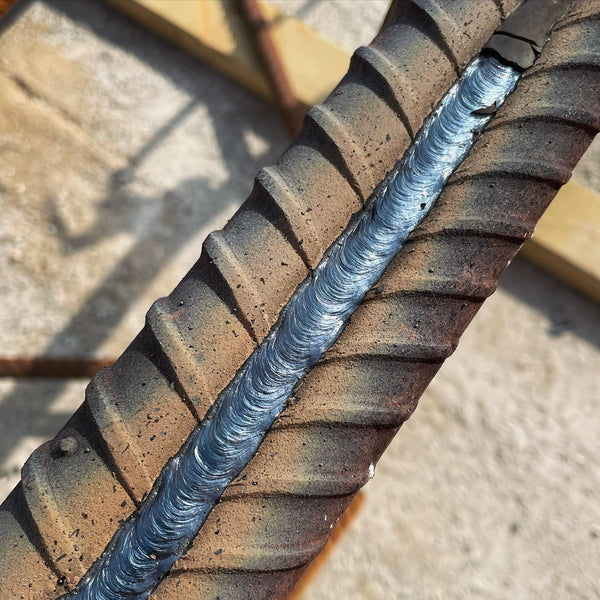
Weld with E6010, Photo by @wilsonanddaughterwelding
Finally, it will take some time to get the hang of the multi-pass Stick welding procedure. But once you master it, you unlock the ability to weld metal regardless of its thickness.
Final Thoughts
Stick welding is an extremely versatile process that will allow you to weld various thickness metals. The biggest advantage is that you can do it cheaply and quickly. As a result, modern repair and maintenance and structural steel welding would be impossible with it.
For you as a hobbyist, that means you can weld mild steel of various thicknesses, but as long as it is not thin. MIG welding sheet metal is significantly easier, while TIG welding provides the highest quality welds. Still, they cannot compete with Stick welding when it comes to the thick stock.
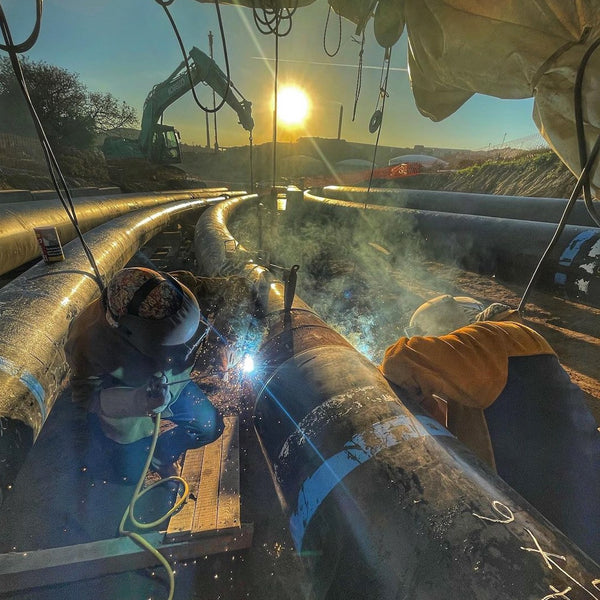
Leave a comment