How To Select Air Compressor For Your Plasma Cutter
Plasma cutting is a metal cutting process that uses high-velocity ionized gas to slice through conductive materials. During the process, the plasma cutter gas is a crucial component.
While you can use hydrogen, oxygen, nitrogen, or argon as a hobby metal fabricator or DIY enthusiast, you will likely use compressed air, the cheapest and most suitable option. However, you will need an air compressor to get the gas supply.
If you are new in the world of welding and cutting, you may be wondering how to select air compressor for your plasma cutter. Although it might be confusing initially, we'll explain everything you need to know before buying an air compressor for your plasma cutter.
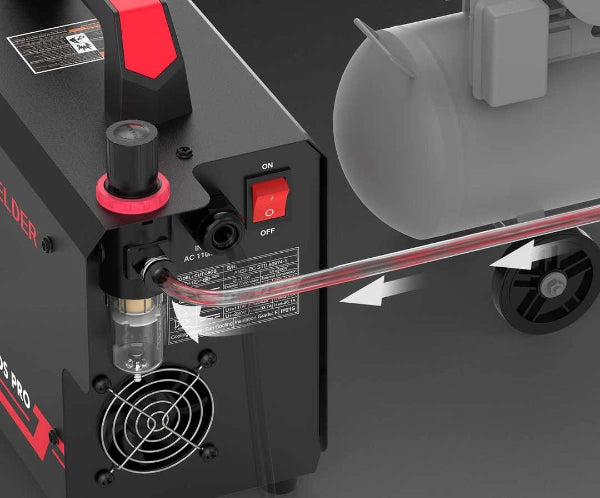
Plasma Cutting And Compressed Air
The cutting process is based on plasma physics and the power of extreme heat. This metal-cutting process uses the advantages of the fourth state of matter, plasma.
Plasma forms once the gasses that make steam are exposed to high energy and ionized. Ionized gas contains positively charged ions and free electrons, allowing it to conduct electricity, respond to magnetic fields, and emit light.
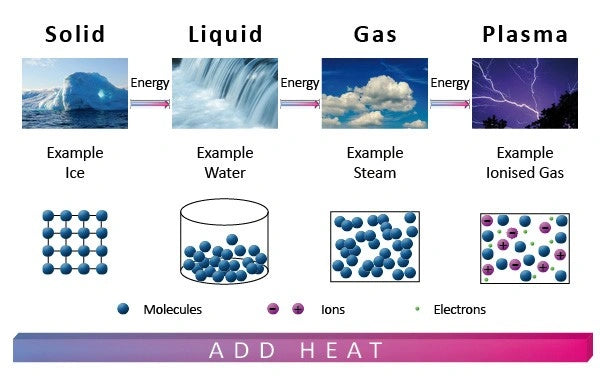
Source: https://www.iasgyan.in/daily-current-affairs/plasma-the-fourth-state-of-matter
In your plasma cutter, a gas such as compressed air, nitrogen, argon, or shop air is forced through a small nozzle orifice inside the torch, increasing its pressure. An electric arc jumps between the electrode and the base piece, giving energy to the gas and creating a plasma jet or plasma stream.

This plasma stream can reach temperatures up to 40,000° F, which allows it to pierce through the workpiece and blow away the molten material. This power makes plasma-cutting a highly powerful and versatile process for cutting any conductive metal.
Do I Need an Air Compressor To Run the Plasma Cutter?
To create a plasma arc, you will need a pressured gas supply, and air is just one of the most common and cheapest choices for low-current cutting of mild steel, stainless steel, or aluminum up to 1 inch thick. Therefore, you will need a clean and compressed gas supplied by an external air compressor.
The compressor supplies pressured air to the cutter to produce a cutting jet. This gas also cools down the torch and consumables to extend their lifespan. Additionally, compressors supply a constant stream of compressed air, which is crucial in achieving high-quality results and allowing you to work flawlessly without any breaks.
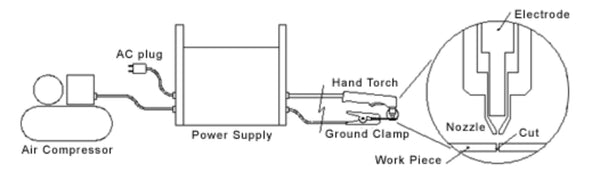
Source: https://www.plasmacam.com/archive/cnchow
However, you can also buy a plasma cutter with a built-in air compressor. These machines have small-sized built-in compressors that provide enough compressed air for light-duty plasma cutting, typically on sheet metals.
Their most significant advantages are portability and versatility, allowing you to cut on the go but with limited power and time. Still, if you have a plasma cutter with a built-in compressor, you don't need to buy another compressor, but some advanced units will let you use both, depending on your needs.
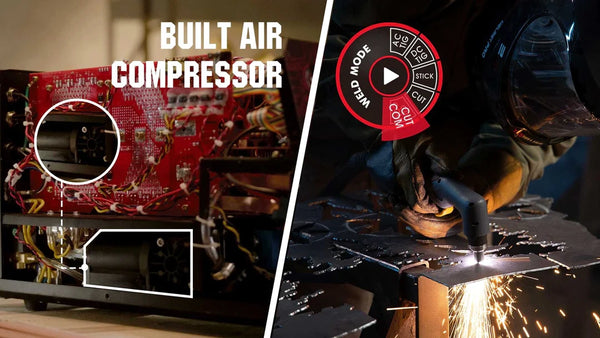
FIRSTESS CT2050 has a built-in compressor and can also connect to an external one.
How Does An Air Compressor Work?
An air compressor is a relatively simple but handy device that provides a compressed air source for your plasma cutter. The air compressor draws the surrounding air through its inlet valve.
Next, the air is driven into the chamber at high pressure utilizing a piston or a rotary screw. As the volume decreases, the pressure of the air increases. The pressurized air is then cooled and stored in a tank or reservoir.
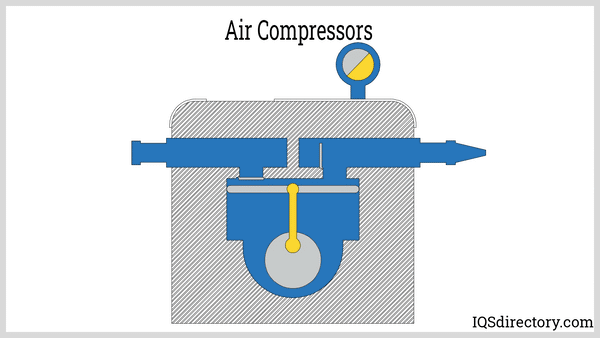
Source: https://www.iqsdirectory.com/articles/air-compressor/industrial-air-compressors.html
The size of the tank will dictate the amount of compressed air that can be stored and used for your plasma-cutting operation. A pressure regulator allows you to set the airflow for your cutting, and then compressed air goes through the hoses, into your filter, and eventually into the plasma cutter torch.
How To Choose an Air Compressor For Your Plasma Cutter?
Now that you are familiar with the importance and working principles of air compressors, it is time to learn how to choose the right one. Even though straightforward devices, air compressors have various specifications that should match your plasma cutter's needs.
The first step in choosing a suitable compressor is reading the manufacturer's instructions. Each manufacturer states the airflow and pressure needed to operate at optimal power. For example, YesWelder Cut55-DS Pro requires 72.52PSI (0.5 MPa) pressure and 7.5CFM flow, but there is more, so let's dive further.
The Size Of Air Compressor
As noted above, air compressors draw the surrounding air, compress it, and store it in a tank for further use. The tank size will depend on the plasma cutter's air needs and your needs or the amount of cutting you will be doing.
Overall, for the light to moderate cutting jobs, you will need a 20 to 30-gallon tank. This is enough for your DIY and hobby cutting around the garage or fabrication shop, as it won't run out too fast. However, industrial cutting requires at least a 60-gallon air compressor. This will allow operators to work continuously without taking breaks, which is essential for achieving high efficiency.
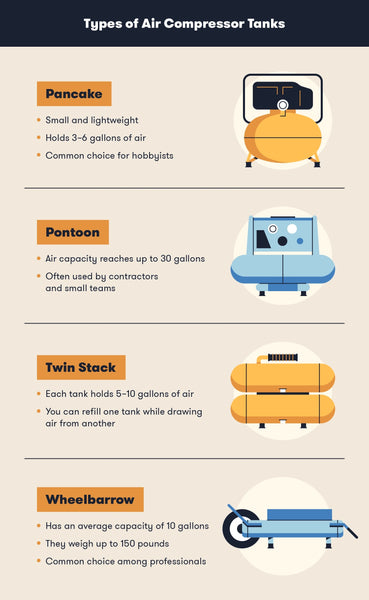
Source: https://www.bigrentz.com/blog/what-size-air-compressor-do-i-need
Even though the bigger, the better is a good approach when choosing an air compressor, remember that larger tanks take up more space in your shop or garage. They also affect portability, so you'll be tied to your compressor at some point, which is not always the best choice, especially if you do outdoor work.
Compressor Airflow
The airflow of the compressor measures the volume of the air delivered by your compressor and is measured in CFM (cubic feet per minute ft3/min). Each plasma cutter has different airflow requirements required to operate at the specific power and duty cycle.
Matching the CFM of both compressor and plasma cutter is crucial in achieving high-quality cuts. But remember that manufacturers usually state the minimum requirements.
For example, a YesWelder Cut55 that requires 7.5 CFM will work fine with an 8 CFM compressor, but for hobby projects or cutting an occasional piece of steel. But if you plan to work a lot with your plasma cutter and make longer cuts, ensure your compressor provides at least 1.5 or 2 times higher CFM than the cutter requires.
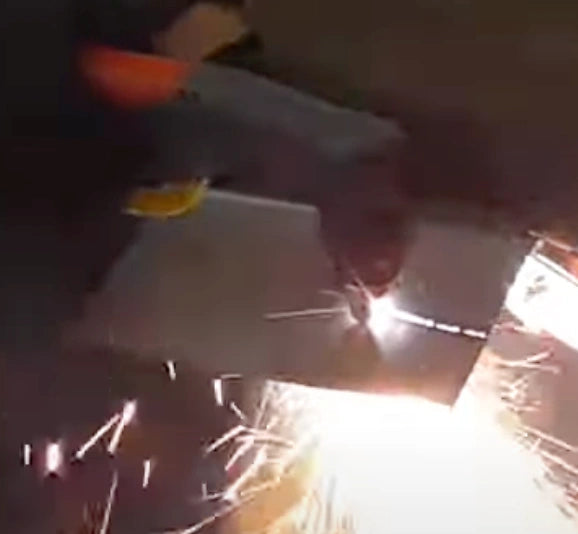
Therefore, if you decide to work with Cut55 on the cuts that take more than a minute or cut pieces close to maximum thickness, you'll need a solid air compressor that can supply 11.25-15 CFM. Insufficient airflow will cause a loss of cutting power and inconsistent arc, so if you notice these issues, you should increase the power and flow.
Air Compressor Pressure
In addition to the flow, you should also match the air pressure of the air compressor and your plasma cutter. The compressed air pressure is typically given in PSI (lb/in2) or MPa (N/m2). One MPa equals 145 PSI, and some international plasma cutters, including the YesWelder Cut55, provide customizable pressure units, allowing you to select the more convenient unit.
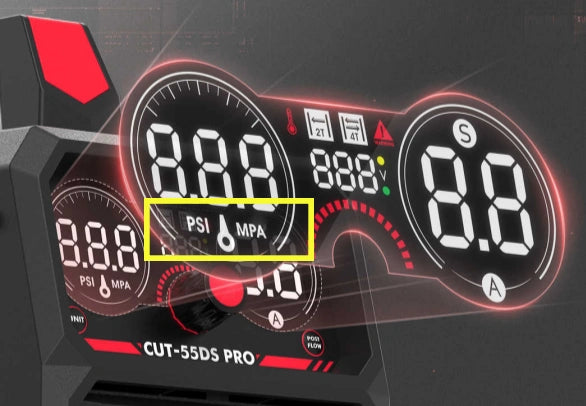
Cut-55DS PRO provide 2 pressure units to select.
To match the pressure of your compressor and plasma cutter, you must look at the specifications. For example, Cut55-DS requires a minimum pressure of 0.5 MPa or 72.52PSI to function correctly, so you will need a compressor capable of continuously providing more than 70 PSI. Larger, automated plasma cutting systems in the 130 to 800 amp range may require 115 psi (8 bar) or more.
Regarding pressure and airflow, you can always choose the more powerful compressor, as it will produce a stable supply even at the harsher requirements. However, keep in mind that more power means bigger and heavier units and also higher costs, so you'll need a sweet spot between the power, price, and portability.
Air Regulation
Matching the right amount of power (pressure and flow) is the first step in choosing the suitable compressor for your plasma cutter. But since most compressors provide much higher maximum compressed air output, you must control this power with an air regulator device.
Today, most plasma cutters, including YesWelder machines, have a built-in air regulator. This regulator helps you adjust the PSI according to the plasma cutter's power needs. However, if your plasma cutter doesn't have a built-in regulator, you will need an external device to help you control the pressure of the air you supply to it.
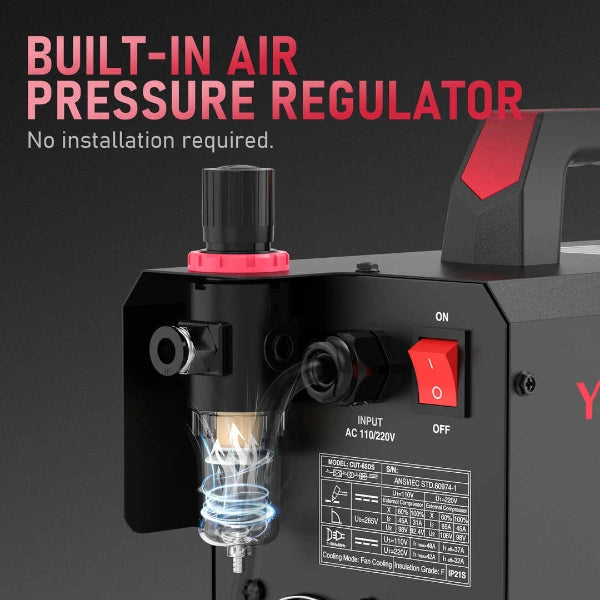
Too much pressure can damage internal components, while too little will create inconsistent results. Therefore, air regulation should be integral to your plasma cutter-air compressor system.
Clean Air Supply
Matching the power of your compressor and plasma cutter is crucial in achieving the advertised power of the cutter. Still, the quality of the cuts and your consumables will highly depend on the cleanliness of the air that your compressor supplies and this is often overlooked by many operators.
During the compression process, oil-lubricated compressors use oil to lubricate the parts and cool the compressed air. This oil is later separated and filtrated to produce the highest-quality results, but over time, small amounts of oil can get through. In addition, air can absorb condensation as it passes through the airline from the compressor to your plasma cutter.
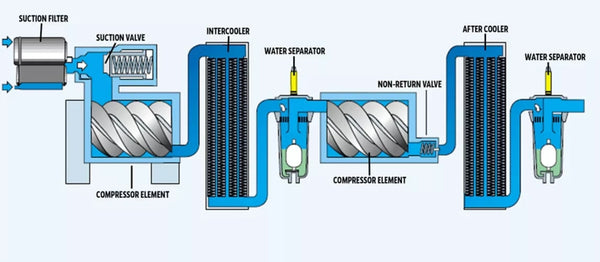
How does an oil-less air compressor work?
Source: https://www.screwfix.com/guides/tools/air-compressor-buying-guide
So, when the air reaches the plasma cutter, it is no longer clean and dry. Moisture and oil can cause severe damage to your consumables and affect the cutting results, so you will need an additional air filter just before the air enters your plasma cutter.
Luckily, some plasma cutter manufacturers, including YesWelder, are aware of this issue, so you get an air filter with your plasma cutter. Therefore, your air goes through a double filtration process to remove water, oil, and debris from your air supply, which saves you hundreds, if not thousands, of dollars by extending the life of your consumables and eliminating the need for grinding the dross.
Single Phase Vs. Dual Phase Compressors
If you browse the market, you can often see single-phase and dual-phase compressors. These fundamentally work the same, but dual-phase compressors have one more step in compression, which results in higher pressure.

Source: https://www.jmindustrial.com/blog/single-stage-vs-two-stage-air-compressors-what-is-the-difference/
- Single-phase compressors are relatively simple machines that intake the air, compress it, and send it to the storage tank. They can produce around 120 PSI, which is more than enough for hobby applications and plasma cutters. These are cheap and versatile for most medium-duty plasma cutting at home and DIY projects.
- Dual-phase air compressors have one more step of compression. They draw in the air, compress it, and move it to the second chamber. Then, they go through the compression process again inside the second chamber, producing rates around 175 PSI, and send it to the tank. These air compressors are more suitable for heavy-duty, industrial plasma cutting, so you won't need a dual-phase unit for everyday cutting.
Power Options
Like plasma cutters and welding machines, air compressors need an input power to run. Most air compressors work at the standard household outlet of 110V or 220V, but there are also dual-voltage compressors capable of working at both 110V/220V.
Before choosing the air compressor for your plasma cutter, make sure its voltage meets the requirements to match your power supply. If you are cutting sheet metal at 110V, you can also go for a 110V compressor, but anything thicker will require 220V.
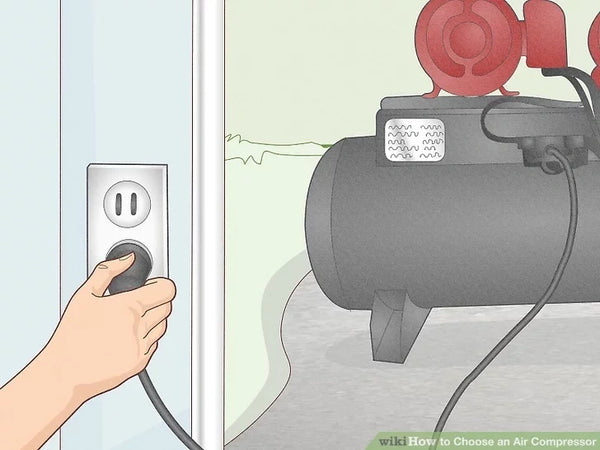
Source: https://www.wikihow.com/Choose-an-Air-Compressor
Noise
Remember that air compressors can be noisy due to friction and a power source (gas-powered air compressors). This can be distracting and inconvenient in both commercial and home applications, primarily if you work in smaller workshops or garages, so pay attention to the noise your air compressor produces.
In the world of air compressors, 40 dB is considered low noise, and some advanced machines are capable of producing this low noise. Meanwhile, 60 dB is considered the safest decibel level for compressors, and most budget-friendly compressors produce this noise. Still, some machines can produce over 85 dB, which can cause long-lasting damage to your hearing after being exposed for extended periods.
Size And Portability
As we noted, the bigger, the better, is certainly a good approach when choosing the air compressor for your plasma cutter, but you should also consider size and portability.
For example, 20 amp plasma cutters are small portable machines suitable for sheet metal. Many favor them because they can easily be moved around the shop or garage. Due to their low output power, they will also have low compressed air requirements, so the last thing you want to do is match a light-duty machine with a powerful, large, and heavy air compressor that you will rarely be able to move around the shop.
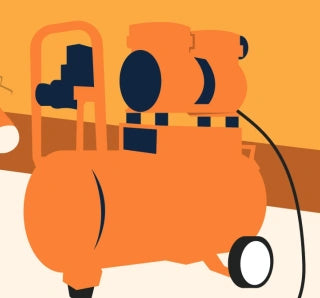
Source: https://www.bigrentz.com/blog/air-compressor-use
Meanwhile, heavy-duty plasma cutters rated at 80+ amps need a strong and large air compressor, usually fixed in the workshop. These are typically used to supply multiple machines such as paint guns, plasma cutters, and more, and they are built to withstand excessive use and provide consistent air supply throughout the cutting applications.
Price Of Air Compressor
The price of the compressor can closely relate to its power and size, so you will have to find the sweet spot. Once again, you don't need to spend a fortune on the large air compressor for light-duty, hobby, and DIY plasma cutters. Small, single-phase compressors that match the flow and pressure needs will do just fine.
If you want even greater versatility and a better money-to-value ratio for light-duty cutting, you can opt for a plasma cutter with a built-in air compressor. The price of these units is higher than the plasma cutter alone but lower than the added cost of buying both a plasma cutter and a separate air compressor.
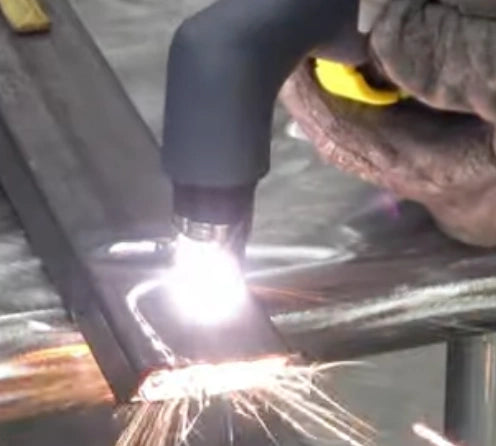
Finally, heavy-duty plasma cutters require a high-quality and powerful air compressor with a larger tank, which can be a costly investment. Still, these provide enough pressure and flow for heavy-duty plasma cutting, and they can power more tools at a certain price.
Final Thoughts
Plasma cutting is very closely related to air compressors, as they provide a consistent supply of compressed air, which is required to cut the desired pieces consistently. Air compressors today come with different powers, advanced compression options, and features, so choosing the right one can be challenging for beginners.
However, once you understand an air compressor's essential features and parts, choosing the right one can be much easier. All you have to do is ensure that the compressor provides enough pressure, airflow, and clean air supply to your plasma cutter, and you are set for success. Still, consider other factors such as noise, size and portability, power options, or price, as they can make your plasma cutting significantly more convenient.
🧐How To Select Air Compressor For Your Plasma Cutter FAQ
Yes, you need an air compressor to run a plasma cutter. The compressed air provided by the compressor is essential for creating the plasma arc that cuts through metal. Additionally, it helps cool the torch and consumables, prolonging their lifespan.
While some plasma cutters come with built-in compressors for light-duty cutting, for more substantial jobs, an external air compressor is necessary for consistent and efficient operation.
2. How to choose the size of air compressor?
When selecting an air compressor for your plasma cutter, consider the tank size based on your cutting needs. For light to moderate jobs, a 20 to 30-gallon tank suffices, ideal for DIY or hobby cutting. For industrial cutting, opt for a 60-gallon compressor for continuous operation and high efficiency. Remember, larger tanks occupy more space and limit portability, so balance your needs with practicality.
👏 You may be interested in the following:
Leave a comment