How Pulsed Welding Works
Pulsed welding has revolutionized how we join metals by providing greater control over the welding process and producing stronger and more precise welds. This innovative technique rapidly alternates the welding current between high and low levels, creating a pulsing effect allowing greater control over the heat input and welding speed.
Pulsed welding has proven particularly effective for welding thin materials, such as aluminum and stainless steel. It is used in a wide range of industries, from automotive manufacturing to aerospace engineering.
In this article, we'll explain how pulsed welding works and explore its many benefits and applications.
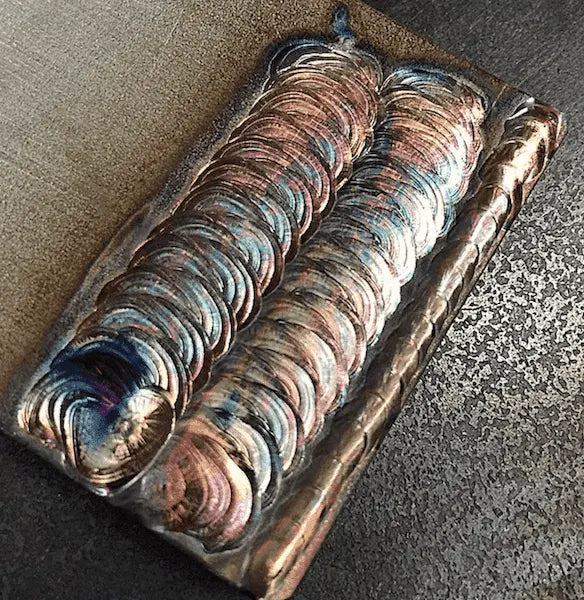
What Is Pulse Welding, And How Does It Work?
Pulse welding is a form of welding in which the amperage alternates between a high and a low point. Unlike Constant Voltage (CV), where the current is represented by a straight line, pulsed welding drops the current when extra power is not needed, cooling off the process.
As a result, the overall heat input is lower, while you still get proper penetration when required. The effects of pulsed welding are most noticeable on thin metal sheets and weld metal with relatively low heat conductivity, which is prone to distortion, burn-through, and other defects caused by high heat. The ability to tailor the welding current waveform is courtesy of inverter technology, which made it widely available even to budget welding machines.
To further understand how pulse welding works, we'll talk about the main pulse welding machine settings:
- Pulse frequency
- Peak current/Background current
- Pulse percentage
Pulse Frequency
Pulse frequency is one of the first settings you will encounter when setting up your welder. It represents the number of pulses per second, expressed in Hertz (Hz). For example, setting the pulse value to 1 Hz means you will get one pulse from peak to background current in one second.
The frequency values in modern welders range from 0.5-200 Hz, but industrial-grade machines can even achieve 500 pulses per second when needed. The frequency can significantly impact the results and appearance of the weld, so it is crucial to set it right.
- Low pulse settings of 0.5-1 Hz produce an outstanding weld appearance, and it is often used when looking for that stacked dimes weld. You dab the filler metal during the peak current, remove the rod and advance the torch during the background period. You can use it to practice TIG welding rhythm and repair uneven TIG weld beads.
- A 2-10 Hz soft arc setting, is excellent when you need a broad weld puddle. However, it results in a lower penetrating weld, which is most suitable when welding outside corner joint or cap pass in multi-pass welding.
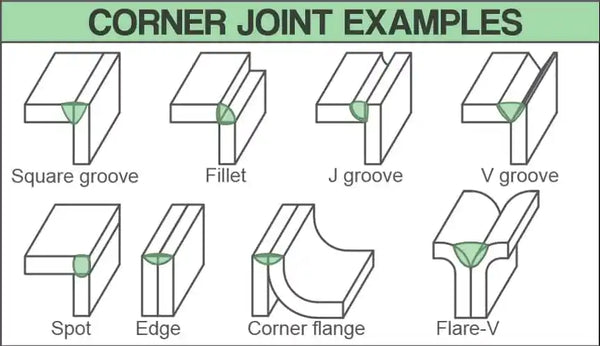
Source: https://engineersblog.net/what-is-square-corner-joint/
- A 10-30 Hz will produce strobe arc light, which many find unpleasing to look at. Even though you can experiment with it, this frequency can be highly disorienting.
- The default range of 100 Hz is a great starting point for any beginner. If you are new to pulse welding, we recommend starting at 100 pulses per second, then experimenting with lower or higher values.
- Over 100 Hz, you get a stiffer arc that is completely opposite to a soft arc. The weld bead is narrow, but you get deep penetration, better arc control, and faster welding speed which is essential when welding thicker metals.
Peak Current/Background current
Peak amperage is the upper end of the welding current in the pulse duty. It is the amperage you would set on your regular welder without a pulse feature, so there is nothing fancy about it. The background is what makes pulse welding unique.
This base or background amperage is the low point of the pulse cycle, where the current turns to reduce the overall heat input. For example, if you set the frequency to 50 Hz, the current will alternate 50 times between peak and background amperage in the second.
The background amperage is usually represented in the percentage of the peak amps. For example, if the peak amperage is set to 100A and the background current is 40%, the primary current will alternate from 100 A peak to 40A background in one pulse. Due to possible confusion, some latest machines will allow you to set the background current in amps rather than percents.
Pulse Percentage
The pulse percentage is similar to the AC balance settings, and it represents how much time the current spends on peak and background amperage during a single pulse. The ratio is, by default, set to 50%, which means that 50% of the pulse cycle will be spent on the peak amps, and 50% of the pulse will be spent on the base amps.
The higher the percentage you set, the more time arc spends in the peak current. More time spent in peak current means more penetration and vice versa. These settings go up to 90%, where it is almost all peak current, down to 20%, where the arc spends most time in the background amps. For beginners, we recommend starting with a 40-60% pulse percentage and working it out according to your needs.
Pulsed TIG Welding
Pulse mode is one of the essential features of any modern TIG welding machine, and you can find it with YesWelder YWT-200DC Lift TIG Spot TIG Welder. Pulse welding in Gas Tungsten Arc Welding will allow you to tweak some of the most crucial welding variables, like depth of penetration, heat input, bead width, and weld appearance, by setting the frequency, current, and percentage. However, pulse TIG welding performs best when welding thin materials and metals that require lower heat input.
YesWelder YWT-200DC Lift TIG Spot TIG Welder
By adjusting the frequency, amperage, and percentage, TIG welders can successfully weld thinner or thicker sections and get exceptional weld aesthetics and reliable welds. Pulsed TIG welding is ideal for precision welding, as it provides greater control over the welding process. Additionally, pulsed TIG is effective for welding dissimilar metals, such as aluminum to stainless steel.
Our dedicated article on Pulsed TIG welding will help you learn more about it.
Source: https://yeswelder.com/blogs/news/pulsed-tig-welding-weld-thin-like-a-pro
Advantages Of Pulsed TIG welding
Pulsed TIG (Tungsten Inert Gas) welding offers several advantages over traditional welding methods. Here are some of the key benefits:
- Greater control: Pulsed TIG welding allows for precise control over the welding current, which also affects the amount of heat input, welding speed, and penetration depth. When tuned right, you can get lower heat input while retaining the good penetration required to produce solid welds.
- Improved quality: The pulsed TIG welding technique produces cleaner and more precise welds than traditional TIG welding. It results in stronger and more aesthetically pleasing welds that require less post-welding finishing work. You get outstanding results by coordinating the TIG torch movement, filler rod feeding, and pulses.
- Reduced heat distortion: Pulsed TIG welding generates less heat than traditional TIG welding, which reduces the risk of heat distortion, warping, or cracking of the material being welded. This is especially important when welding thin metals.
- Versatility: Pulsed TIG welding can be used on a wide range of materials, including aluminum, stainless steel, and nickel alloys.
- Efficiency: Pulsed TIG welding minimizes secondary operations, as it is completed more quickly than traditional TIG welding, which can result in cost savings and increased productivity.
Pulsed MIG Welding
The pulsed MIG process is an advanced form of welding that represents a modified spray transfer. It combines the fundamentals of pulsed welding, where current oscillates from peak to background amperage, with spray metal transfer as a non-contact method.
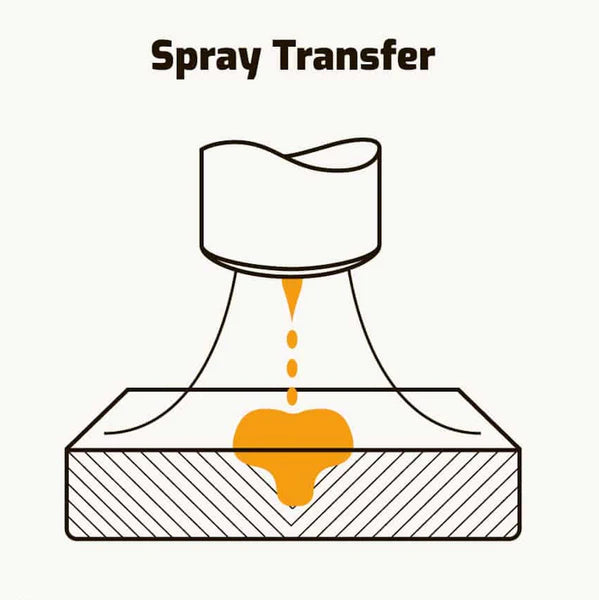
Source: https://weldguru.com/welding-transfer-modes/
During the peak cycle, the high current pinches the droplet of molten metal from the wire and transfers it into the weld joint. Once the current goes to a background cycle, the amperage is lowered so metal transfer does not occur. Background current maintains the arc, and limits the heat input to the weld seam, allowing the weld to cool to avoid burn-through or distortion.
Only one droplet forms and sprays into the weld during the pulse cycle. This allows you to control the weld bead and avoid high heat input, which is essential when welding exotic or thin metals. Additionally, pulsed MIG welding improves metal distribution, produces less spatter and fumes, and more aesthetically pleasing welds while providing higher wire feed speed and wire and gas savings.
Pulse On Pulse Welding
The pulsed MIG process goes even further by introducing another pulse on top of the pulse, which results in dual pulse or pulse-on-pulse MIG welding. The first pulse is your standard pulse with a peak and base amp. The second pulse turns the first pulse on and off.
During the on cycle, the second pulse turns on the first pulse, so the regular pulsed MIG occurs. During the off cycle, the second pulse turns off the first pulse. As a result, the current is so low that there is no metal transfer. As a result, the metal deposition to the weld stops, but the arc remains present.
The manipulation of pulses produces even more downtime between the high amperage moments. As a result, the weld is colder than the single-pulse MIG, so you will need higher amperage to get a more penetrating weld. However, dual-pulse MIG welding provides even better heat control and a good weld appearance. With it, you can produce those stacked-dimes welds on aluminum, which was reserved only for TIG welding in the past.
This advanced technology is usually found in more advanced machines, but luckily with YesWelder YWM-211P Double Pulse MIG Welder, you don't have to spend a fortune to get it. So if you want TIG-like welds with your MIG welder, do not hesitate to try pulse-on-pulse mode.
YesWelder YWM-211P Double Pulse Aluminum MIG Welder
Advantages Of Pulsed MIG Welding
Pulsed MIG welding offers a series of advantages over the conventional MIG welding process and standard metal transfer methods. The most important benefits of pulsed MIG welding are:
- Heat control: by initiating a background cycle, you prevent more heat from affecting the welded pieces and causing distortion or burn-through in delicate and thin pieces. That's why it is commonly used to MIG weld aluminum, but it can be useful on stainless steel, nickel, and other alloys sensitive to heat input.
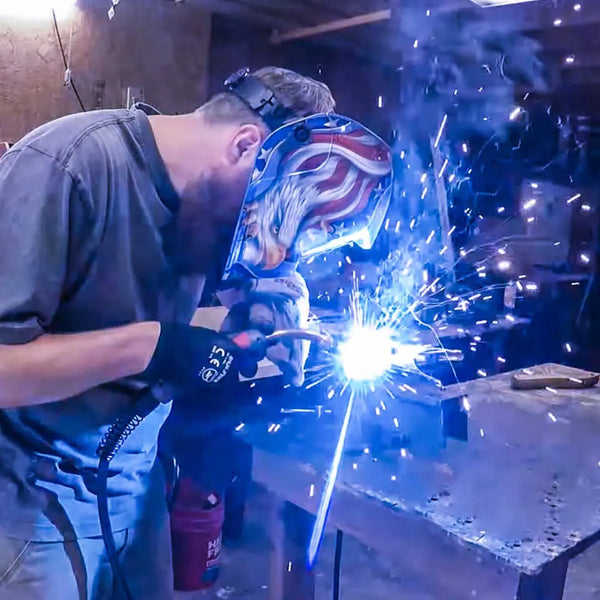
- Reduced spatter and fumes: pulsed MIG welding causes less spatter compared to traditional MIG and transfer methods. Less spatter means more wire deposited into the weld pool and less time spent cleaning, which affects the overall cost savings. Fewer fumes mean a safer and healthier environment for welders.
- Out-of-position welding: the background cycle of the pulse welding promotes cooling of the weld, which is great when welding in different welding positions. Faster cooling reduces the risk of weld wandering and dripping out of the puddle.
- Improved productivity: pulse MIG offers high deposition rates in all positions where dip or spray transfer is not applicable. Compared to other transfer methods, pulsed mode will help you get the job done quicker, which is essential if you are looking to cut the production costs.
- Weld quality and appearance: last but not least, pulsed MIG produces a more stable arc compared to traditional methods, which yields highly aesthetic welds. With pulse-0n-pulse, you can even achieve TIG-like welds with your MIG welder while retaining good weld characteristics.
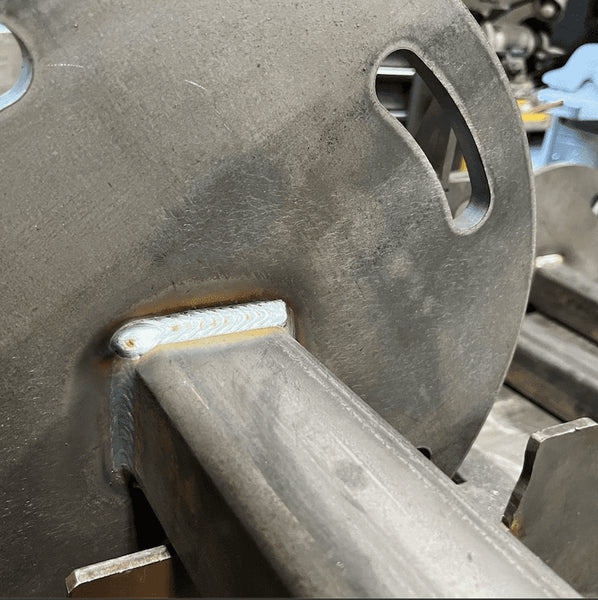
Disadvantages of Pulse Welding
While pulsed welding techniques offer several advantages over traditional welding methods, there are also some potential disadvantages to consider.
- Cost: Pulsed welding equipment can be more expensive than traditional welding equipment, which may be a barrier for smaller welding operations or those on a tight budget. Luckily, YesWelder is bringing even more pulsed welding equipment at reasonable prices.
- Complexity: Pulsed welding techniques require more skill and training than traditional welding methods. It takes time to master the various parameters and settings that control the welding process. That's why we recommend pulsed welders with synergic control, which offers a beginner-friendly interface.
- Limited applications: Pulsed welding techniques are only suitable for some welding applications. For example, they could be more effective when welding thicker materials or tight spaces. That's why it is essential to understand the fundamentals and benefits of pulse welding before using it for your everyday welding.
Conclusion
Pulsed welding techniques offer several advantages over traditional welding methods. Whether it is pulsed TIG welding or pulsed MIG welding, these techniques provide greater control over the welding process, resulting in higher quality and more precise welds.
The reduced heat input and welding fumes, as well as the decreased risk of heat distortion, make pulsed welding a popular choice across a wide range of industries. Additionally, the increased efficiency of pulsed welding can result in cost savings and increased productivity.
As welding technology continues to evolve, pulsed welding techniques will undoubtedly play an increasingly important role in the field of metal fabrication and welding.
🧐How Pulsed Welding Works - FAQ
1. What Is Pulse Welding, And How Does It Work?
Pulse welding is a form of welding in which the amperage alternates between a high and a low point. Unlike Constant Voltage (CV), where the current is represented by a straight line, pulsed welding drops the current when extra power is not needed, cooling off the process.
2. What is the advantages of pulsed TIG welding?
- Greater control: Pulsed TIG welding allows for precise control over the welding current, which also affects the amount of heat input, welding speed, and penetration depth. When tuned right, you can get lower heat input while retaining the good penetration required to produce solid welds.
- Improved quality: The pulsed TIG welding technique produces cleaner and more precise welds than traditional TIG welding. It results in stronger and more aesthetically pleasing welds that require less post-welding finishing work. You get outstanding results by coordinating the TIG torch movement, filler rod feeding, and pulses.
- Reduced heat distortion: Pulsed TIG welding generates less heat than traditional TIG welding, which reduces the risk of heat distortion, warping, or cracking of the material being welded. This is especially important when welding thin metals.
- Versatility: Pulsed TIG welding can be used on a wide range of materials, including aluminum, stainless steel, and nickel alloys.
- Efficiency: Pulsed TIG welding minimizes secondary operations, as it is completed more quickly than traditional TIG welding, which can result in cost savings and increased productivity.
3. What is the disadvantages of pulse welding?
- Cost: Pulsed welding equipment can be more expensive than traditional welding equipment, which may be a barrier for smaller welding operations or those on a tight budget. Luckily, YesWelder is bringing even more pulsed welding equipment at reasonable prices.
- Complexity: Pulsed welding techniques require more skill and training than traditional welding methods. It takes time to master the various parameters and settings that control the welding process. That's why we recommend pulsed welders with synergic control, which offers a beginner-friendly interface.
- Limited applications: Pulsed welding techniques are only suitable for some welding applications. For example, they could be more effective when welding thicker materials or tight spaces. That's why it is essential to understand the fundamentals and benefits of pulse welding before using it for your everyday welding.
Leave a comment