MIG vs. TIG vs. Stick vs. Flux-core Welding
Welding is a broad field with tens of welding processes, each used when it's best suited. You can see everything from laser and resistance to cold welding in professional applications.
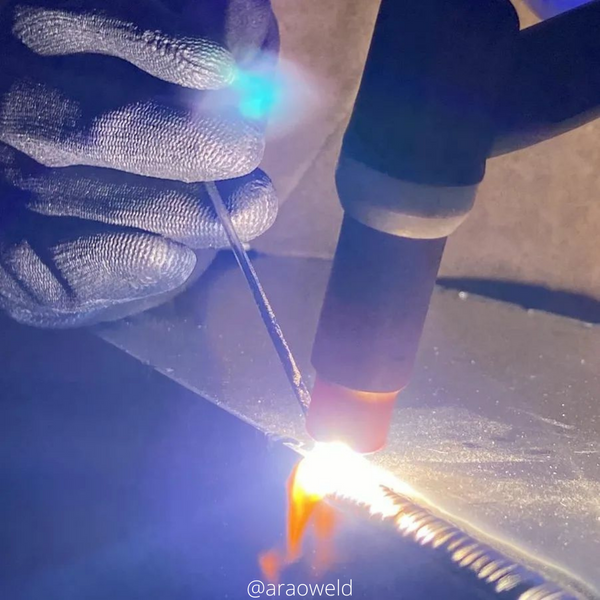
But the four most prominent and most widely used welding processes are MIG, TIG, Flux-Cored, and Stick welding processes. These are manual, but they can also be automated.
This article discusses these four processes from a hobbyist and a beginner welder perspective. You will learn what they are, how they work, their advantages, disadvantages, and when to use each of them.
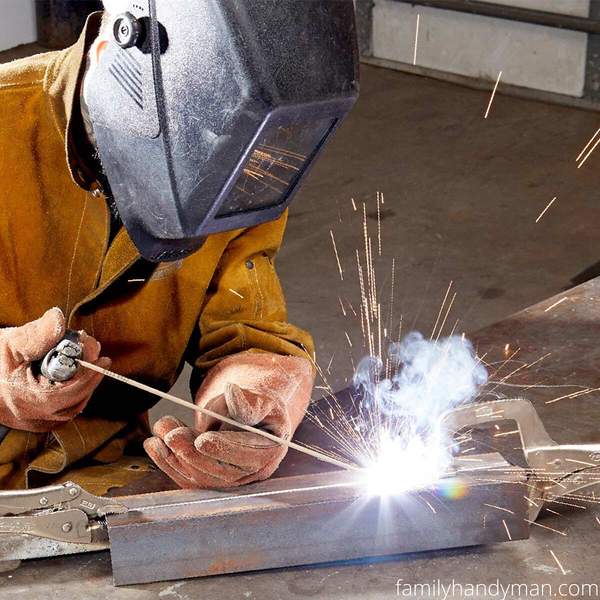
Some Fundamental Points About Welding
Before we get started, let's go through some fundamentals in short. There are different types of welding used to join metal together. The four welding processes we will explain in this article are all arc welding processes. They use electric arc and electrical resistance to melt the base and filler metals and make a welding joint.
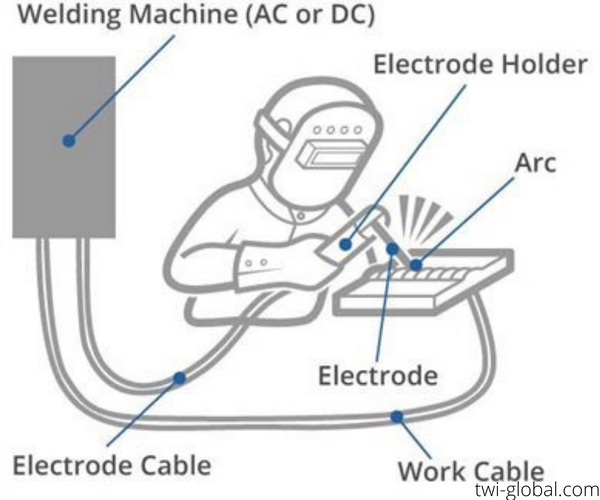
Any arc welding process requires weld pool protection from the atmosphere's elements like nitrogen and hydrogen. These atmospheric elements cause porosity and cracking if they enter the weld pool. Additionally, the shielding gas modifies the arc behavior and the transfer of the filler metal to the joint.
MIG and TIG use a shielding gas, while stick and flux-cored arc welding processes are gasless. Stick and flux-cored rely on flux which releases the shielding gas while burning to provide the isolated atmosphere around the weld puddle. The MIG and TIG don't produce slag, while the stick and flux-cored arc welding leave slag as the residue of the burned flux.
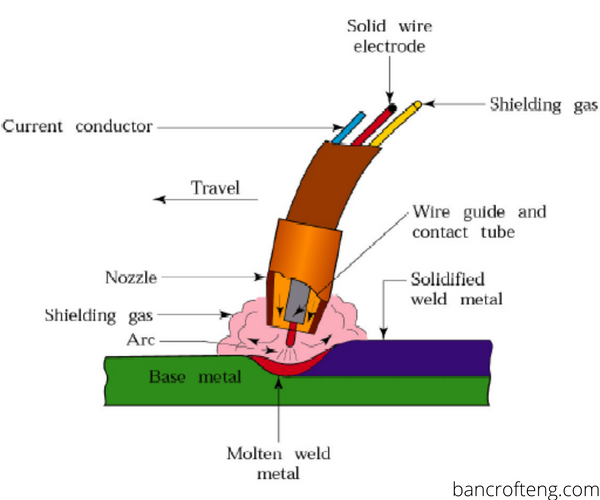
To run any of these processes, it's necessary to have a closed electrical circuit. A ground clamp must be attached to the welded metal piece while the torch/electrode holder completes the electrical circuit when making contact with the metal piece.
In welding applications electricity flows in one of two ways:
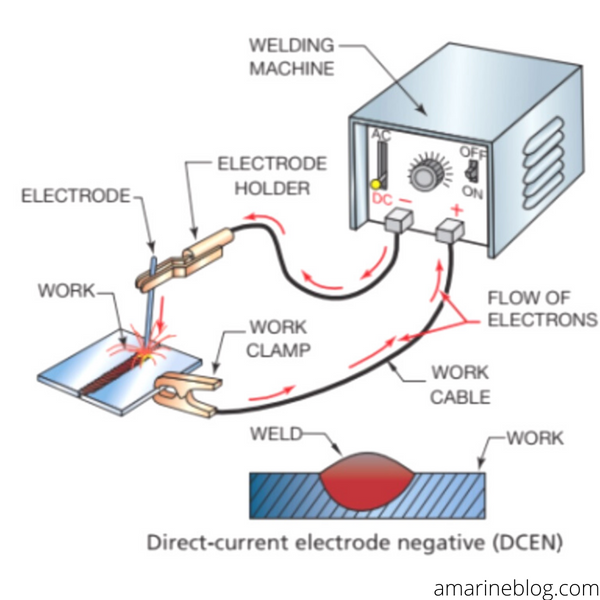
- DCEN (Direct current electrode negative) - Electrode lead is attached to the negative terminal of the welding machine. Ground clamp lead is connected to the positive terminal. Electricity travels from the negative to the positive. The electricity starts its path in the welder, travels through the electrode first, it's attracted by the positive ground clamp attached to the metal piece, and the arc finally makes the jump from the negative electrode to the positive metal piece.
- DCEP (Direct current electrode positive) - Electrode lead is attached to the positive terminal of the welder. Ground clamp lead is attached to the negative. Electricity travels from the negative to the positive, as is the law of physics, so there is no change there. The current starts in the welder, travels through the ground clamp first, enter the metal piece, and when the positive electrode touches the metal, the current jumps from the metal to the electrode, causing the arc to form.
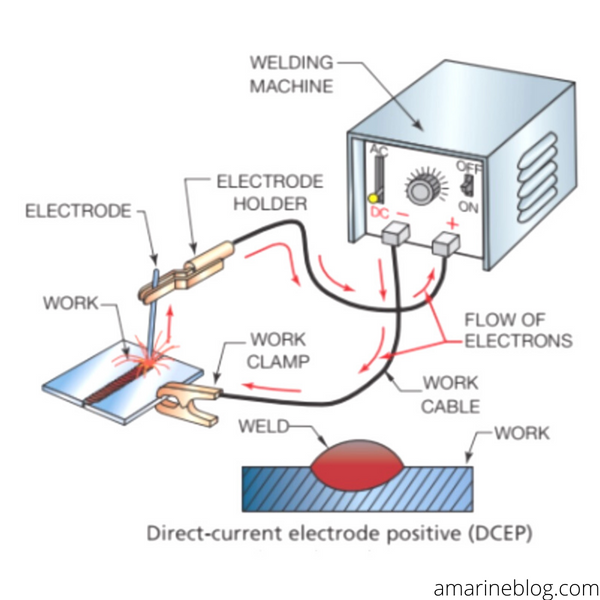
The resistance to the electrical current flow causes the metal to melt, but there is a substantial difference if we are using DCEP, DCEN, or AC (switching between DCEN and DCEP many times in a second).
If these fundamentals are not making much sense to you now, don't worry because once we apply this to specific welding processes, it will all fall into place.
MIG or Metal Inert Gas Welding Process
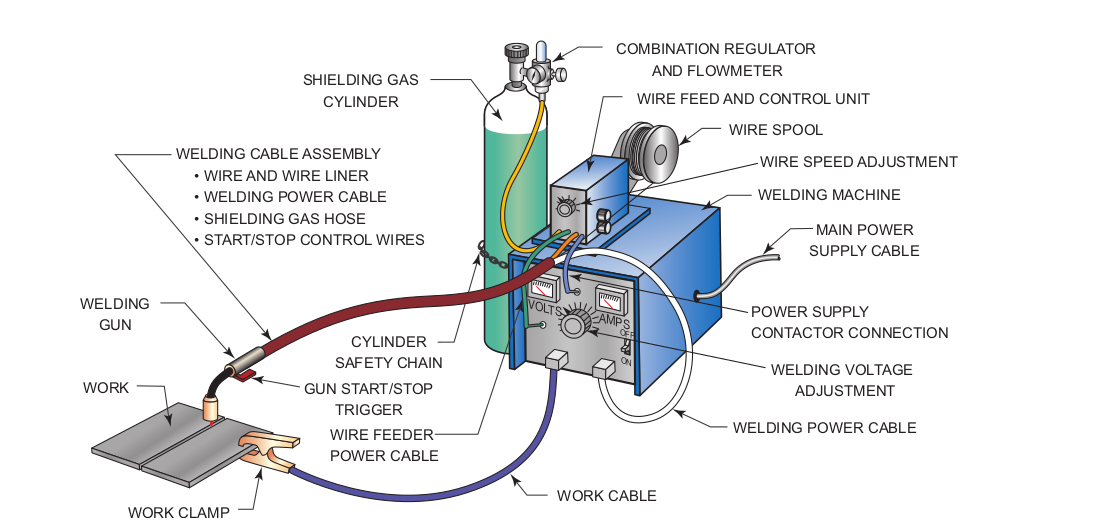
Source: Welding principles and applications book by Larry Jeffus
MIG or GMAW (Gas Metal Arc Welding) is the easiest welding process to learn. It's used by hobbyists and professionals alike.
In short: the MIG welding process uses a wire feeding system, and the fed wire acts as a filler metal and an electrode. The process requires a shielding gas, supports multiple modes of metal transfer, can weld thick or thin materials, and has a good metal deposition and welding speed.
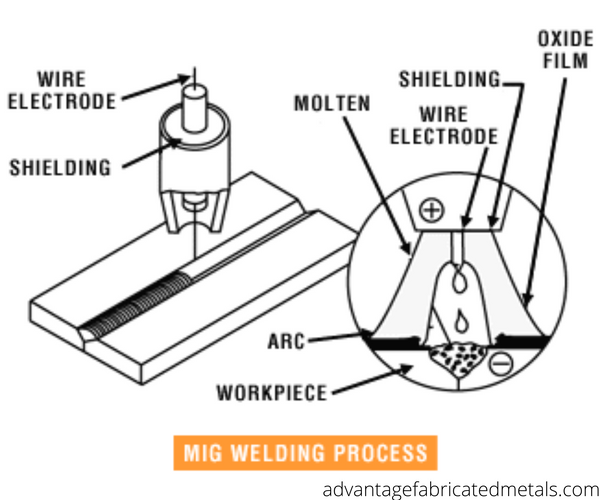
The MIG is one of the most widely used processes everywhere in the welding industry. It doesn't leave any slag behind, but it requires the shielding gas. The gas is typically Argon and CO2 mixture, but it can be pure Argon for better arc quality or pure CO2 if welding on a budget.
How it Works
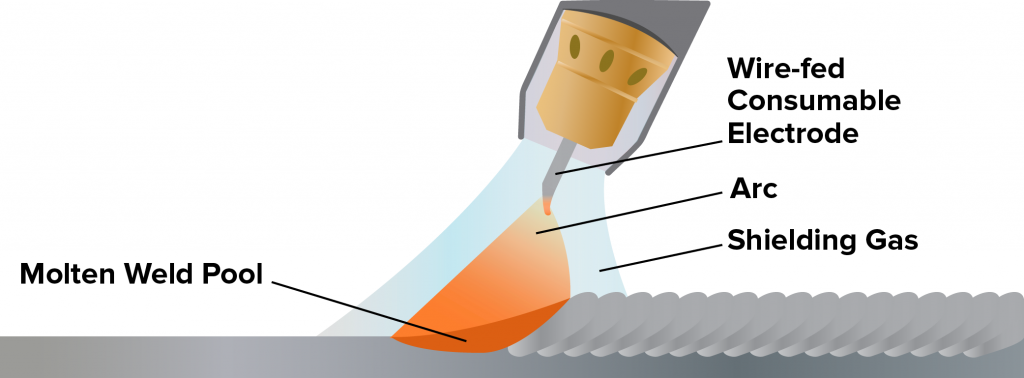
Source: https://www.weldingsuppliesfromioc.com/blog/stick-vs-mig-vs-tig-which-process-is-right-for-you/
A MIG welder has a wire feeding system inside it which feeds the wire from a spool, through the special drives, and into the MIG gun through the lead. The wire is electrically hot and acts as an electrode and a filler metal. Gas metal arc welding requires DCEP, and if you accidentally use DCEN, the arc will be erratic, resulting in globby welds.
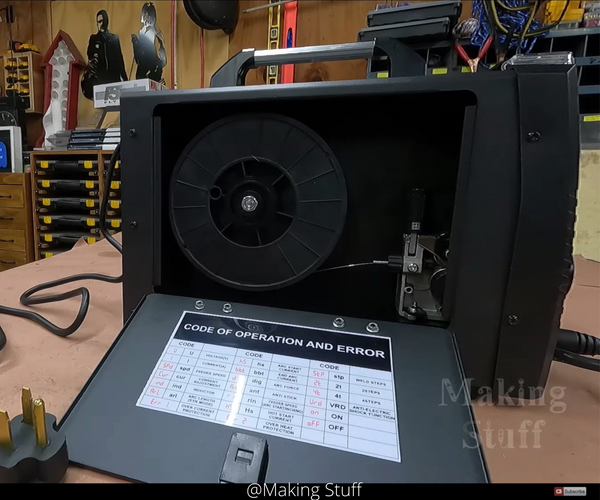
Besides the wire, the MIG gun also supplies the shielding gas to protect the weld pool. The gas cylinder is connected with the welder via a gas hose. The gas is released once you press the trigger on the MIG gun so that the tip of the MIG torch feeds wire and the shielding gas into the joint.
MIG welding is primarily used to weld steel, but you can also weld aluminum using a spool gun, or a special liner for the regular MIG gun. It requires 100% pure argon shielding gas for aluminum welding.
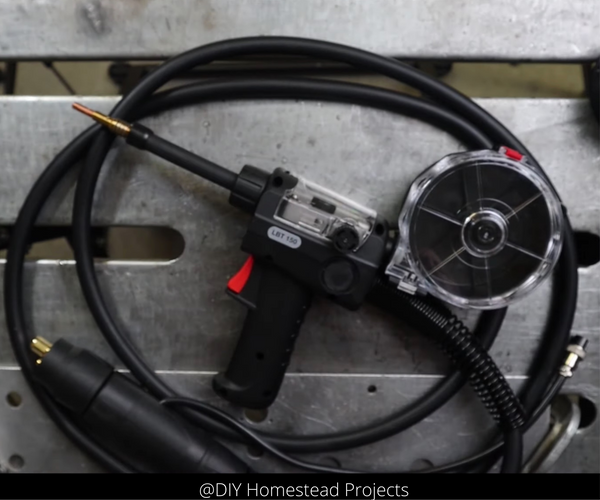
The Downsides
One of the downsides of MIG welding is that it can't be used in windy conditions. Wind can easily blow away the shielding gas and expose the weld puddle to the atmosphere, causing weld defects in the process. In such conditions, flux core arc welding and stick welding are preferred.
The wire used when MIG welding doesn't contain enough additives to combat dirt, oil, rust, and other contaminants well. That's why this welding process requires precleaning to the shiny metal if possible. The ER70S-6 wire contains additional deoxidizers and can help when welding dirtier or rusty metal. Even so, MIG welding doesn't handle welding dirty metal.
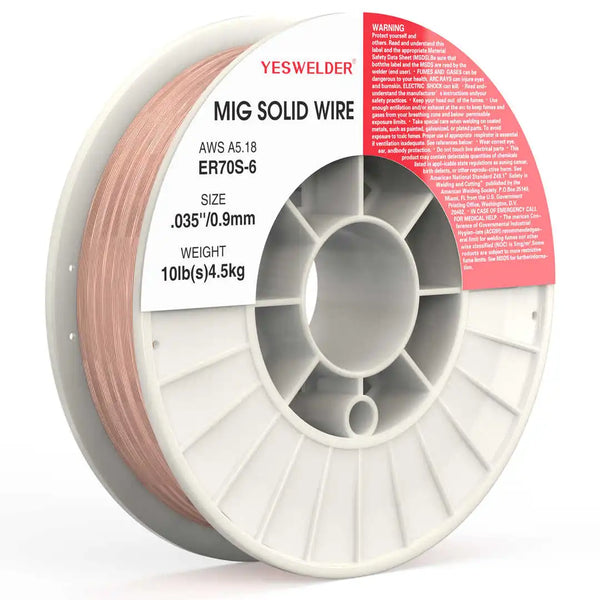
What's Best About MIG Welding
The MIG welding process can be learned in two weeks and improved upon from there. The welds are simple to lay, and the push/pull techniques define the results. Pushing the gun ahead of the puddle produces lower penetration while pulling/dragging the gun away from the deposited metal produces deeper penetration.
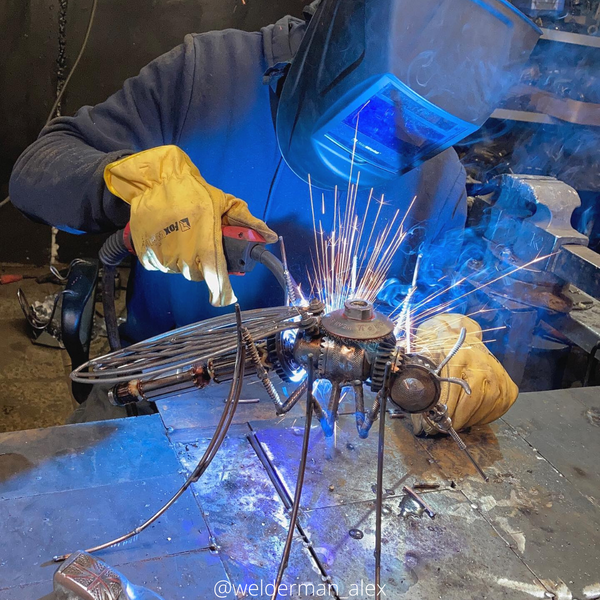
While the MIG creates some spatter, there is much less of it than with the flux core and stick welding processes. The welds produced with MIG are high-strength and have a great appearance, requiring little to no post-weld cleaning. Thanks to continuous wire feeding and shielding gas, MIG welding can produce long welds with little downtime, unlike with the TIG and stick welding, which require constant breaks.
Flux-Cored Welding Process or FCAW (Flux Cored Arc Welding)
The flux-cored welding process is similar to MIG but with some crucial differences. This process is great for hobbyists and professionals, just like MIG welding, but there are many reasons why you would want to use one over another.
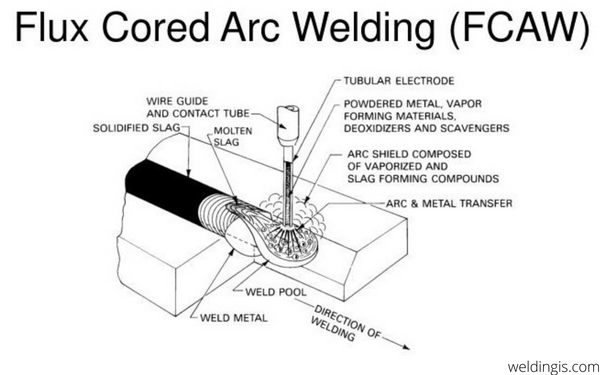
In short: the Flux-cored welding process uses a wire feeding system, just like MIG. The wire acts as an electrode, filler metal, and contains a flux in its core. The flux in the hollow center of the flux-cored wire reacts with the welding arc to form a shielding gas. That's why the wire is called self-shielded flux-cored wire. FCAW leaves slag behind, produces more heat than MIG, and is not best suited for the thinnest materials.
How it Works
Almost any MIG welder can run an FCAW process but not every FCAW machine is capable of MIG welding. That's why dedicated FCAW-only welders are sometimes called "wire feeders."
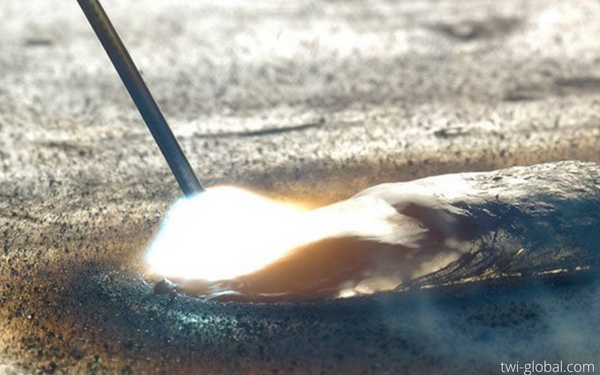
The wire is fed from inside the machine through the knurled drives into the MIG gun. The wire is electrically hot, and upon making contact with the metal piece, it starts the arc, which melts the metal and the wire, burning the flux in the process. Unlike MIG, the FCAW must use DCEN polarity.
The burned flux emits gasses and shielding compounds into the weld puddle, protecting it from the atmosphere and contaminants like rust, oil, and grease. The flux-cored wire produces slag that sits on top of the finished welds that need to be removed with a chipping hammer. The flux core wire can have different slag systems like rutile and basic, each with pros and cons.
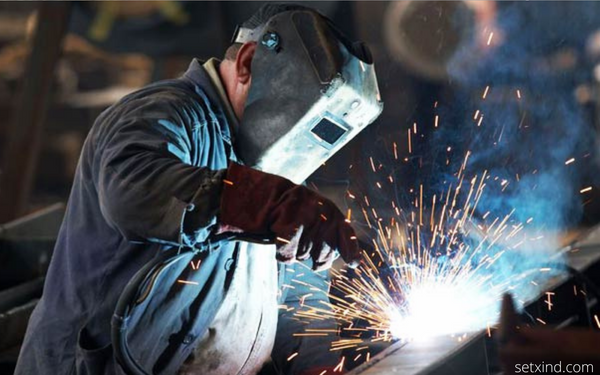
FCAW is primarily used to weld steel and stainless steel, but also for cast iron, and hard facing/surfacing alloys. Aluminum and other nonferrous metals can't be welded with it.
The Downsides
This process produces significantly more smoke than MIG or stick welding, making it difficult to see the weld pool. Additionally, this requires increased ventilation when welding indoors.
Due to a higher heat input than MIG, the FCAW is not recommended for welding thinner than 20 gauge. It is easy to burn through, especially since the weld pool is challenging to see.

The welds produced with the FCAW method don't look as good as when welding MIG, and often require post-welding clean up. Plus, removing the slag between each pass further increases the necessary time to complete a joint.
What's Best About FCAW Welding
Removing the need for a shielding gas cylinder makes the FCAW cheaper to run than MIG and more portable. It allows welding outdoors with heavy wind thanks to the slag protection that can't be blown off like the shielding gas.
This process allows for higher wire deposition rates, more penetration, and joining thicker materials. The added compounds in the wire's flux allow FCAW to weld dirtier metal than MIG. While clean metal is always preferred when welding, the FCAW handles impurities better thanks to deoxidizing and scavenging elements added to the flux-cored wires.
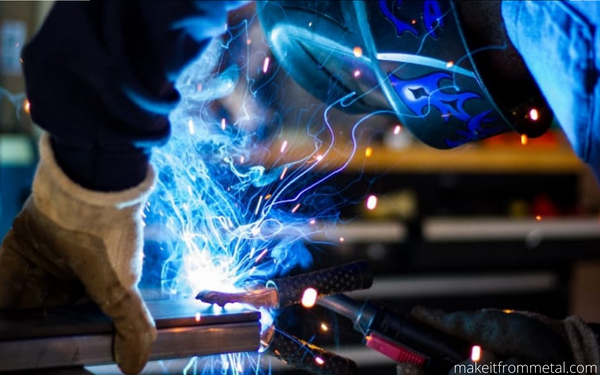
Flux-cored wire can easily be broken off by hand at the tip of the welding torch, unlike solid MIG wire that requires wire clippers. The MIG welding gun doesn't need a nozzle because there is no need to direct the shielding gas to the weld pool. Removing the nozzle makes it easier to weld hard-to-reach spaces and better view the welding joint.
TIG or Tungsten Inert Gas Welding Process
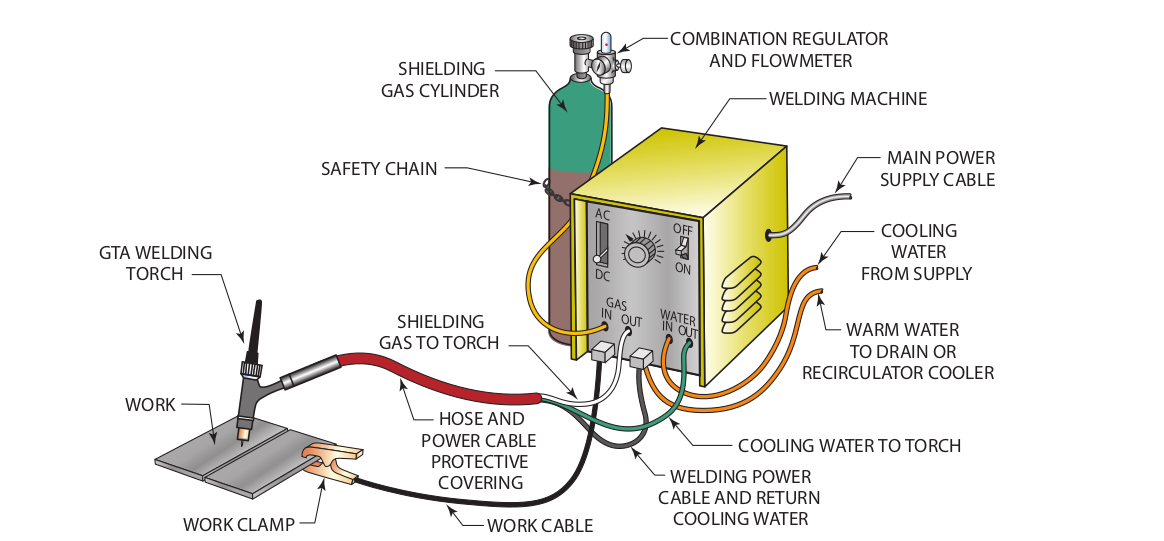
Source: Welding principles and applications book by Larry Jeffus
Unlike MIG or Flux core, the TIG welding process relies on the operator to manually feed the filler wire into the weld pool. This process is gas-shielded, like MIG, and it produces the highest quality welds of all manual welding processes.
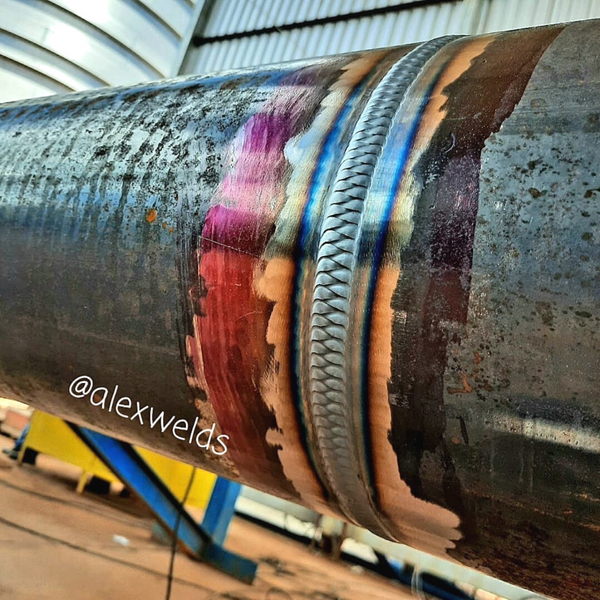
TIG or GTAW (Gas Tungsten Arc Welding), also called heliarc by oldtimers, is the most challenging process to learn. Welders who TIG weld are usually paid more, and this process is used when weld quality and esthetics are of the highest importance.
In short: the TIG welding process is gas-shielded, and the wire is fed manually. It uses a non-consumable tungsten electrode and works with DC and AC output. Welding with TIG is slower than other processes and requires a lot of skill. It produces the cleanest and most beautiful welds and joins the most comprehensive array of metals.
How it Works
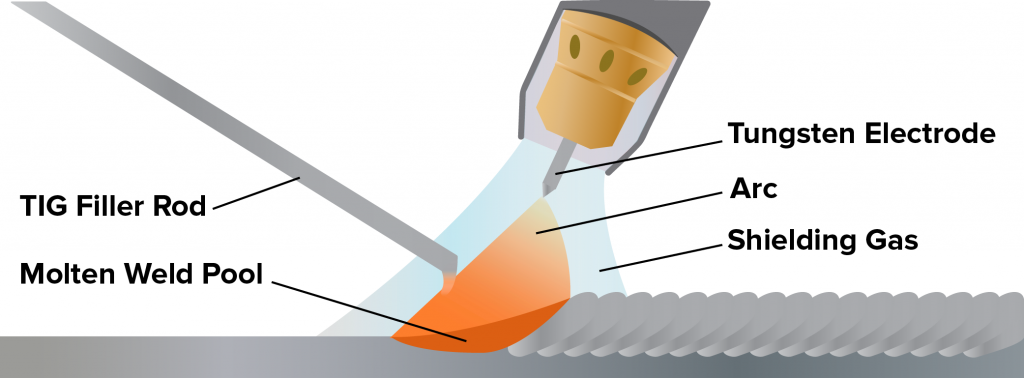
Source: https://www.weldingsuppliesfromioc.com/blog/stick-vs-mig-vs-tig-which-process-is-right-for-you/
The TIG torch comprises multiple elements, but the most important are the tungsten electrode and the cup. The tungsten electrode sticks out a bit from the cup and starts an arc via one of three ways: scratch start, lift start, and high-frequency (HF) arc start. The HF is the cleanest method because the arc jumps from the tungsten to the metal piece without any physical contact, avoiding weld pool contamination.
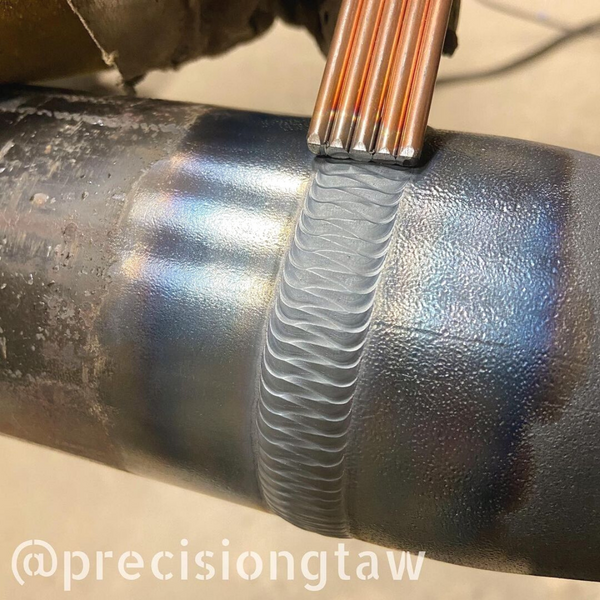
The tungsten electrodes vary in chemical composition, namely by the principal oxide's percentage. Every tungsten type is meant for specific use cases. The tungsten electrode's tip shape directly impacts the arc shape and the resulting weld. So, there are a lot of variables when it comes to the tungsten electrode alone.
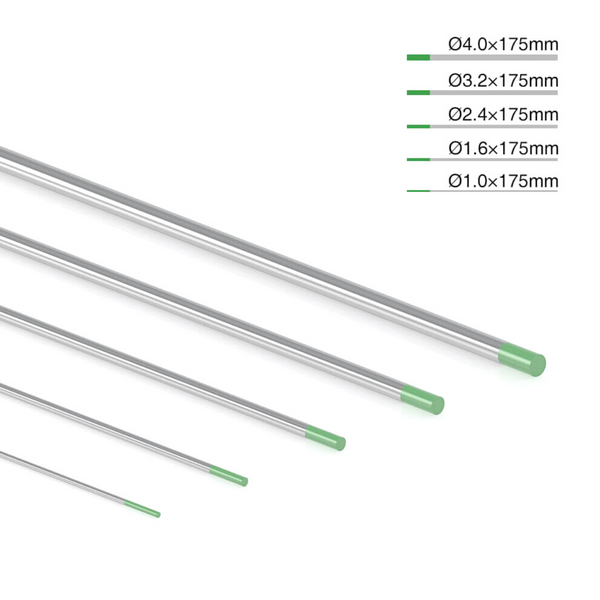
The TIG welding process is done using DCEN, DCEP, or AC, depending on the desired results, the used tungsten, and the welded metal. The AC current is used to weld aluminum because the DCEN and DCEP portions of the AC wave switch many times per second, and allow cleaning action (DCEP) and penetration (DCEN).

So, the DCEP part of the AC wave cleans the aluminum oxide, and the DCEN provides the necessary penetration. That's because the DCEN concentrates heat on the welded metal, while the DCEP focuses it on the tungsten electrode. However, when doing DC TIG, most of the welding is done on DCEN, not DCEP, because it will ball up your tungsten.
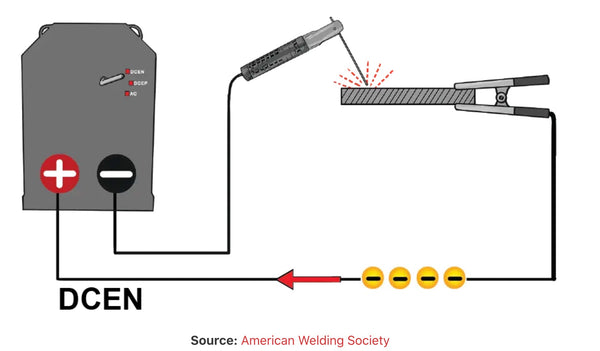
The cup on the welding torch concentrates the shielding gas over the puddle, and the heat-affected zone (HAZ). The gas is fed either through the TIG welder or directly to the TIG torch, and the most common shielding gas for TIG is pure Argon.
The concentrated heat will melt the base metal when you initiate the arc, while the shielding gas will protect it from the atmosphere. If a filler material is needed, you will feed the filler rod with the other hand by dabbing it into the weld pool and avoiding contact between the wire and the electrode.
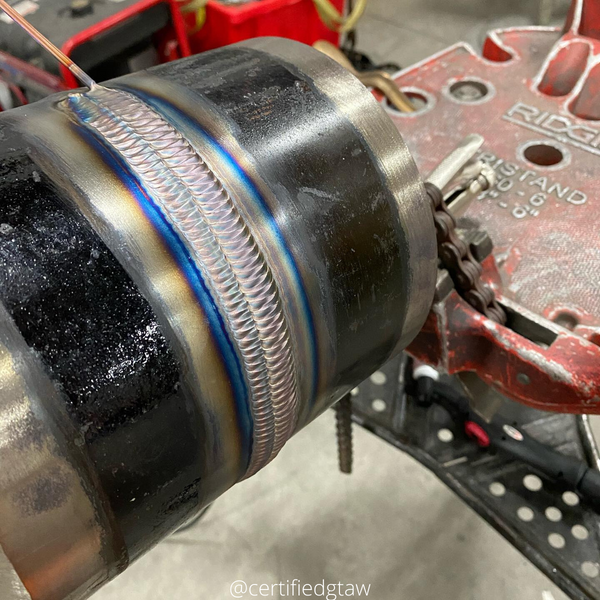
The Downsides
Requiring the use of the other hand and often a simultaneous action with the foot on the pedal to control amperage output, the TIG welding process is challenging to master. Plus, the narrow pin-like arc provided by the tungsten electrode outputs a lot of energy in a small area, making it difficult to control overheating and warping of the metal.
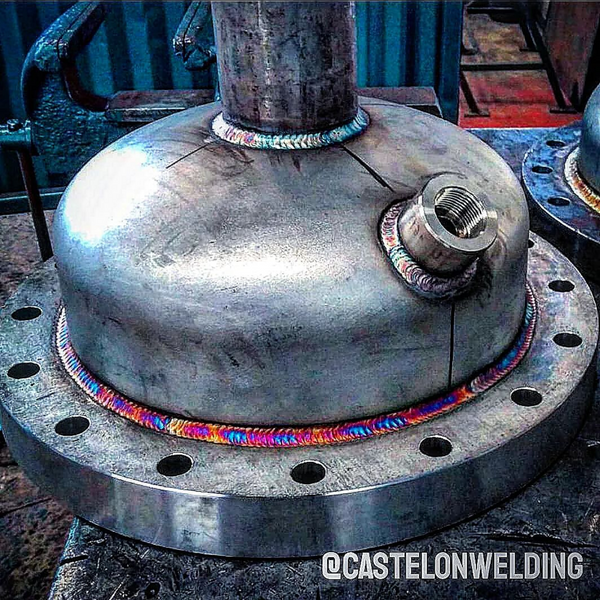
Thanks to the sensitive nature of TIG welding, the welded surface must be 100% clean. There can be no rust, oil, paint, or grease. This increases the joint completion time by adding more work in the pre-welding phase.
The TIG welding process is significantly slower than the MIG and flux-cored process because the filler rod is fed manually, and the filler metal deposition rate is lower.
What's Best About TIG Welding
The concentrated arc allows for much more precise welds. This also results in a narrow HAZ, making it easier to weld thinner metals, but this still requires a lot of skill to manage heat input.
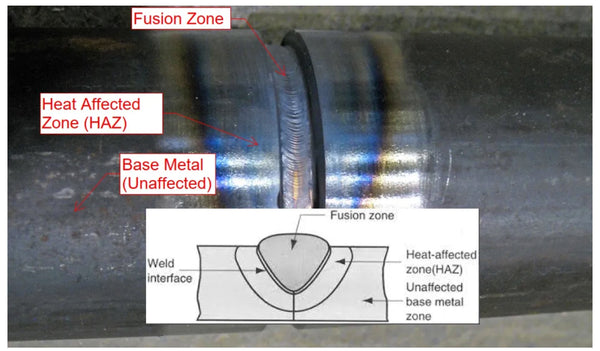
Photo by whatispiping.com
There is no slag to worry about since the TIG is a gas shielded process. Plus, there is no smoke, sparks, or molten metal flying around like with the flux core and MIG welding. This allows you to have maximum visibility over the arc and the weld pool, further improving the success of critical welds.
Gas tungsten arc welding is perfect for welding exotic metals and dissimilar metals together. That's why TIG welds more metals than any other welding method, making it the most versatile welding process. The TIG-produced welds are cleaner, stronger, and of higher quality than what's possible with MIG, flux core, or stick welding.
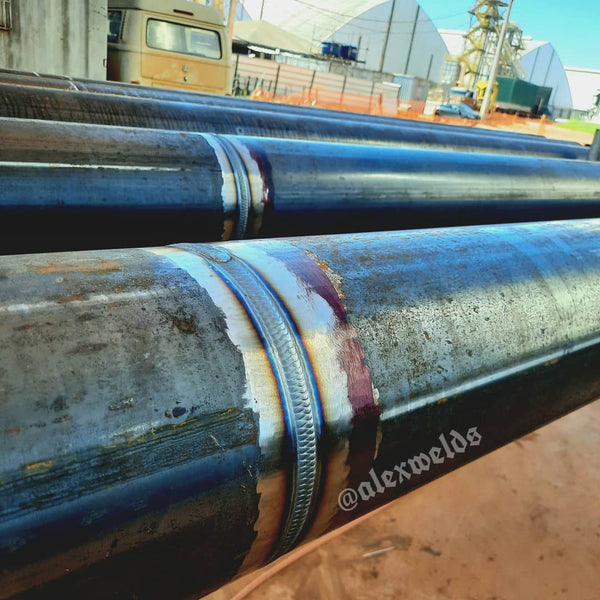
Stick Welding Process or SMAW (Shielded Metal Arc Welding)
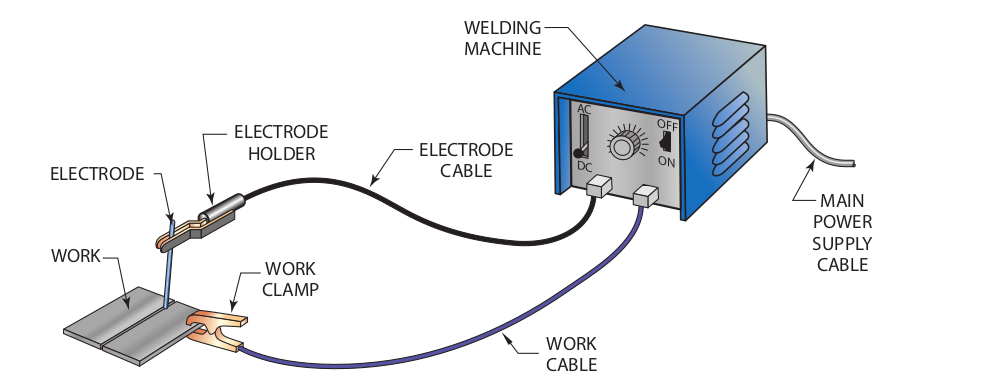
Source: Welding principles and applications book by Larry Jeffus
The stick welding uses a similar power source to TIG, which is why most TIG welders can stick weld as well. However, this process is nothing like TIG. It's dirtier, but faster and much cheaper to run, making it one of the most popular welding methods for hobbyists and professionals alike.
Stick welding is easier than TIG but more complex than MIG and flux core welding. The stick welder setup is straightforward, but the welding takes some getting used to because you have to maintain the arc while the rod is burning.
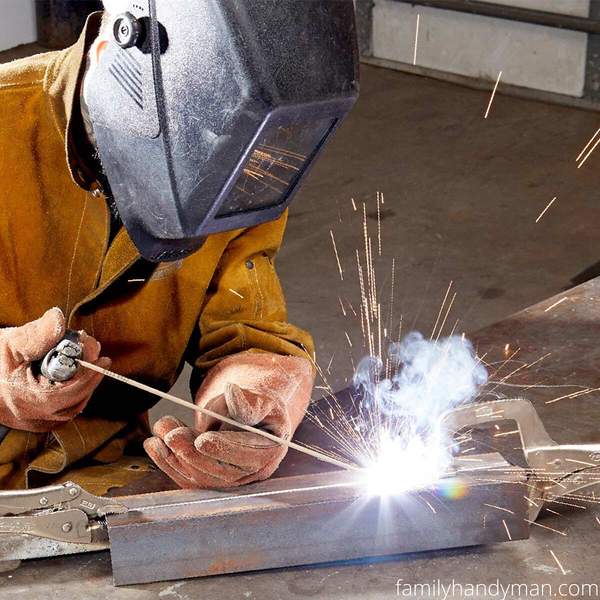
In short: The stick welding electrode melts while welded and acts as a filler metal and a source of a slag/shielding action, requiring no shielding gas. It's a very rugged welding method able to weld dirtier metal and works great in outdoor conditions. It's mostly used to weld mild steel and doesn't do well with thinner metals.
How it Works
The SMAW process melts the coated electrode and joins metals by heating them with an arc formed between the electrode's tip and the welded piece. There are many different welding electrodes, and they vary by the coating (flux) type and the filler metalcore. All electrodes have different use cases, but generally, E6010, E6011, E6012, E6013, and E7018, are used for most hobbyist welding.

Stick welding is done via DCEN, DCEP, or AC. Nowadays, most of the time, the DC is a preferred method. The polarity will depend on the welding rod and the required penetration. The DCEP generally provides a more stable arc when stick welding, but the DCEN is great when welding thinner materials or if you don't want to input maximum heat into the metal.
The Downsides
SMAW doesn't provide very nice welds, and there are a lot of spatter and molten globs that fall all over the welded piece. So, it takes additional work to grind/sand everything and improve how the joint looks post-welding.
Removing the slag by chipping and wire brushing also slows down the process, especially when multi-pass welds are required. Some electrodes have an easy-to-peel slag like the E6012 electrode, but others require more effort.

This welding method is slow, and requires you to make stops because your welding rod will get consumed frequently. This makes it more difficult to weld because you have to tie your welds and continue where you left off.
What's Best About SMAW Welding
The SMAW welding machines are more affordable than MIG and TIG welders. Plus, not having to purchase or rent a shielding gas cylinder and the shielding gas itself, makes stick welding a very economical method.
Using a slag system for shielding against the atmosphere, makes it a great process to run outdoors. Additionally, it's much more tolerable of rust and other contaminants, but it's always better to clean the metal before welding.
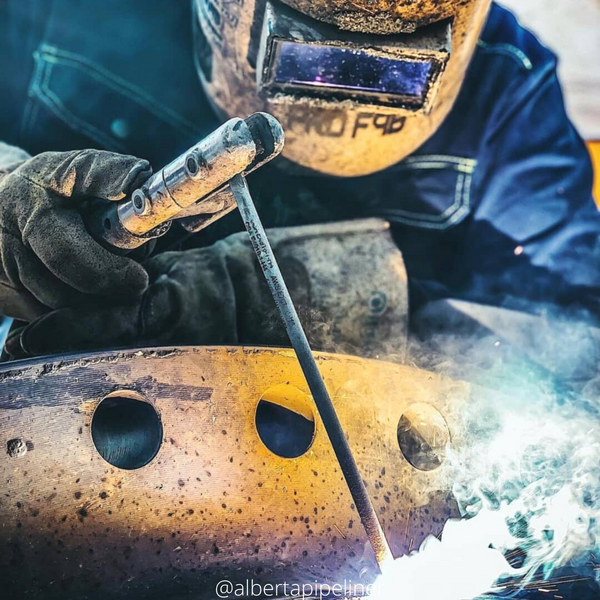
Conclusion
There is much more to be said about these four arc welding processes. So many variables like the metal type, electrode and wire selection, settings on the welder, and others, play a vital part in achieving proper penetration and making beautiful welds.
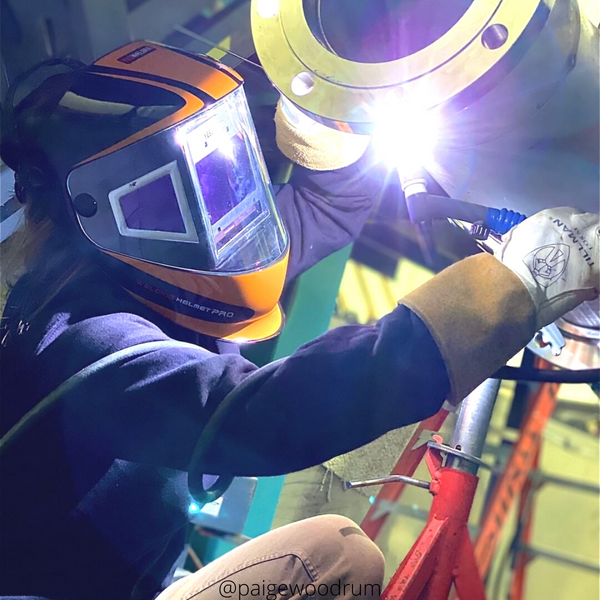
This article was a general overview of the most popular manual arc welding methods to help you grasp their differences, pros, and cons. For a complete beginner, it's probably best to start with MIG, and then try flux core, stick, and finally TIG welding. However, not everyone is the same, and many people begin with the TIG as their first welding process.
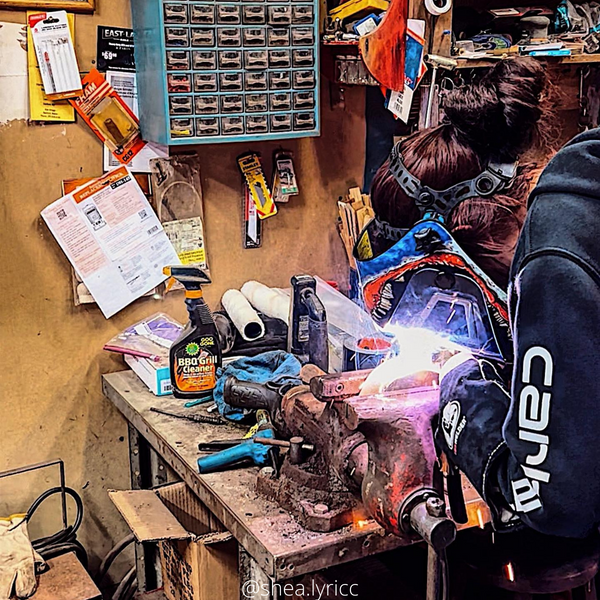
Thankfully, today there are many affordable multi-process welding units a beginner can use to learn all four. YesWelder MIG 205DS is our most popular model, that does all of the processes we discussed here and offers features suited for beginners, but with enough power to satisfy most welding applications.
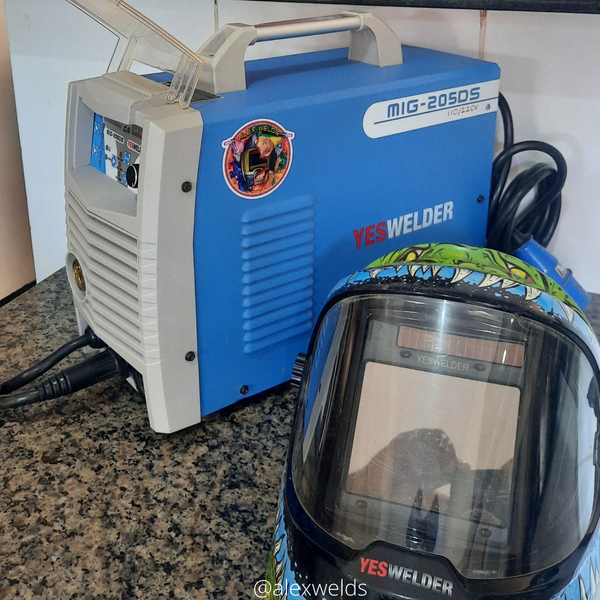
These photographs of welding are stunning. I’d love to have copies of them.
Ruby
Retired pipe welder.
I’ve been welding stick and mig for over 35 yrs but only for repair, some mods and the making of a specialty tools. Though I’m very far from being a professional welder I do pretty good. I bought your 205ds and can’t wait to dig into tig. This article ,as well as many others I’ve read fr Yeswelder ,is very informative and interesting to read. Besides you guys are loading me up with plenty of welding-ammo-words I throw at my Journeyman pipe fitter grandson, who is teaching now and smiles from ear to ear when I come up with his welding lingo. Lol. Thx again making welding affordable, fun, informative and interesting, again.
Leave a comment